So the question is whether or not to take on these projects with internal resources, or to use an outside service bureau. There are three primary factors that should drive that decision:
- Part Complexity
- Internal Tools Available
- Accuracy Requirements
- Frequency of Need
For example, very geometric parts can be easily measured by hand with readily available tools like digital calipers. If sub-micron level accuracy is not required this is a very valid, cost effective option.
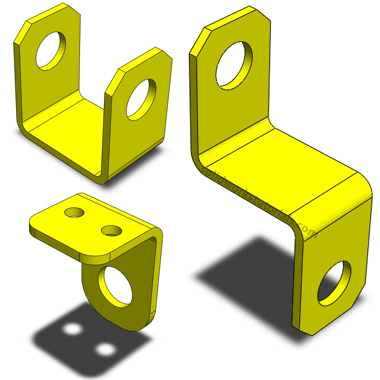
Simple Brackets – Hand Measured into CAD
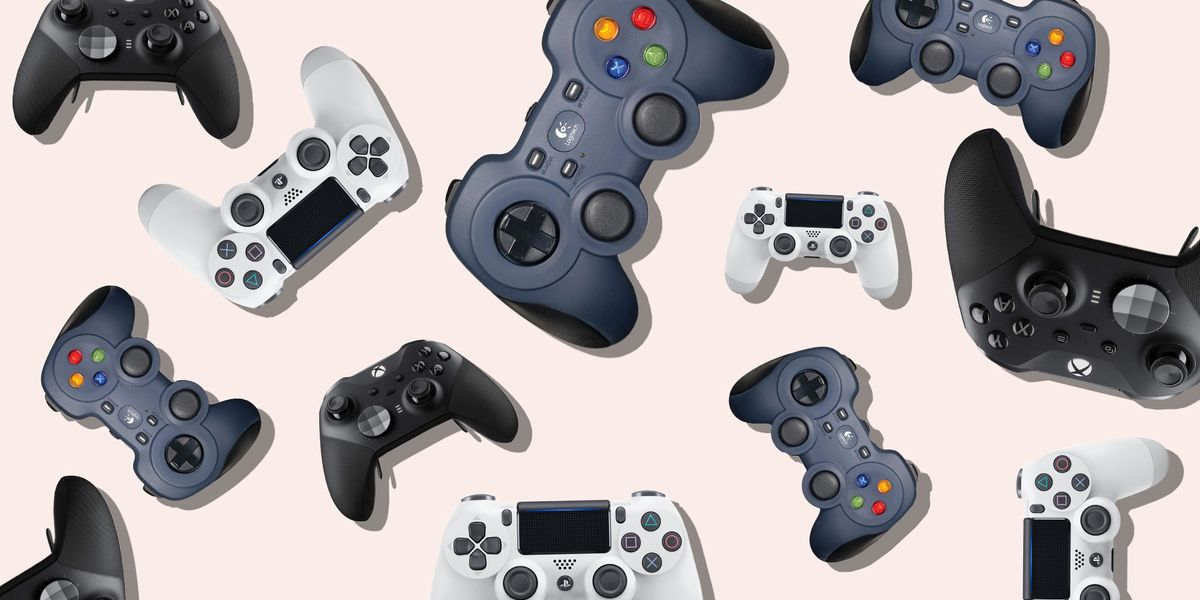
Complex Shapes Like Game Controllers
In cases such as this, it would be best to employ a 3D scanning system, like the Creaform HandyScan Black Elite. 3D scanners, like the HandyScan, capture millions of data points to fully define complex shapes, then output that data in either point clouds, or STL files, which can be used as a starting point for development of 3D CAD files. Dimensional accuracy varies from device to device, but professional systems, like the HandyScan can achieve results within ±.001 or better on small parts.
Once the raw data is captured, specialized software like Geomagic Design X can be employed to develop the CAD model. Design X has a comprehensive suite of tools for both managing the point clouds and STL meshes, as well as traditional and advanced modeling tools for the most complex geometry. Finally, Design X allows the user to compare the final CAD model back to the original raw scan data to ensure accuracy to the original part. That is something that cannot be done with parts measured by hand.
The challenge in employing this type of technology is that it requires a fairly significant investment, on the order of $50,000 to $100,000. This sort of investment may be cost prohibitive for smaller businesses, or for those that only occasionally have the need for this type of work, it may be best to employ a 3d scanning service bureau.
In summary, simple parts that can be easily measured with hand tools are good candidates for in-house reverse engineering, and can very likely be modeled with a reasonable degree of accuracy. However, very complex parts that cannot be measured by hand are better candidates for 3D scanning. If this need arises frequently, it may make sense to invest in equipment and software. If the need only arises occasionally, it’s probably best to utilize a service bureau that specializes in 3D scanning and reverse engineering.
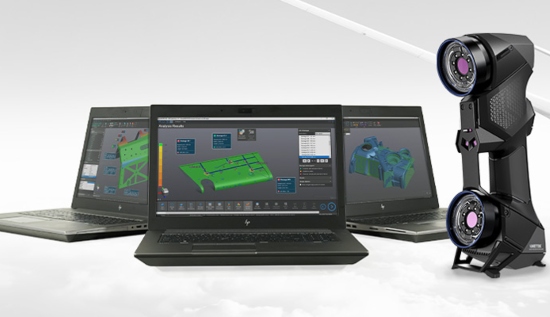
Professional grade 3D scanning solutions for metrology & engineering applications.