With Canyon, mountain bikes can be both efficient and sustainable. The innovative frame geometries are designed using topology optimization which is helped along by large-scale 3D printers that allow engineers to hold their creations in the palm of your hand within just days – not weeks or months like before!
Working with professional cyclists like Jan Frodeno, Alejandro Valverde, and Mathieu van der Poel as well as teams like the Canyon SRAM Racing Team provides new impulses for innovation and development. To realize their ideas, engineers like Johannes Thumm, Senior Design Engineer MTB at Canyon, make use of what large scale 3D printing can offer. His task: “My work is focused on making the most lightweight and most efficient mountain bikes for racing. Exactly the bikes I like to ride myself.”
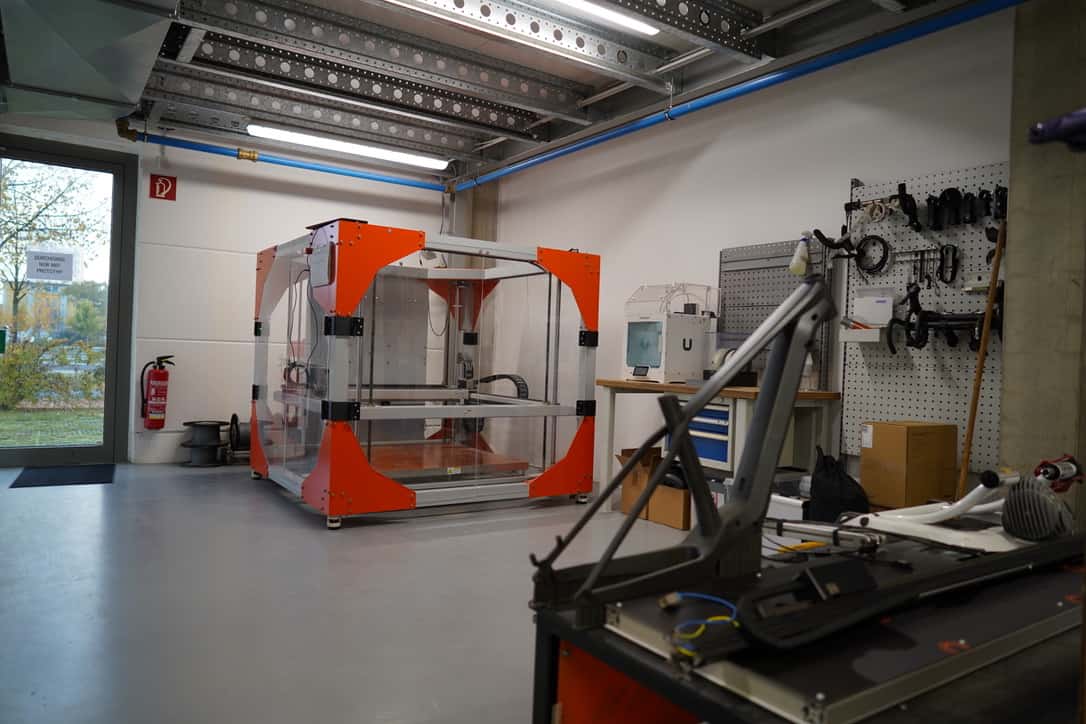
Additive Manufacturing Has Proven to be The Most Efficient Way to Produce Bicycles & Components
Until now, the development of a new frame concept used to be complicated, costly and most of all, time consuming. For a first prototype of a new frame, a mock-up would be welded from steel tubes. This could then be used to attach parts and check the frame’s geometry and appearance. If problems arose a new mock-up was required, which could take weeks or even months.
For carbon fiber frames, making a prototype was even more demanding. Each design iteration required a new milled mold in which carbon fiber can be shaped into the design prototype. . This is a time consuming and therefore expensive process — the mold alone could cost between 10,000 € and 25,000 € — and again, it might be weeks before a frame design can finally be evaluated to decide if changes are necessary or not.
This is where 3d printing comes into play. Using their BigRep ONE, engineers can print the frame geometries that had been designed on the computer within one or two days. In just a short while it is possible to have a frame in hand, to get a real feel for the product, and to compare it with one’s expectations. These design iterations greatly influence the decision to abandon a design or develop it further. Johannes Thumm: “We can simply design, print, check the frame, maybe do some modifications, print it again.”
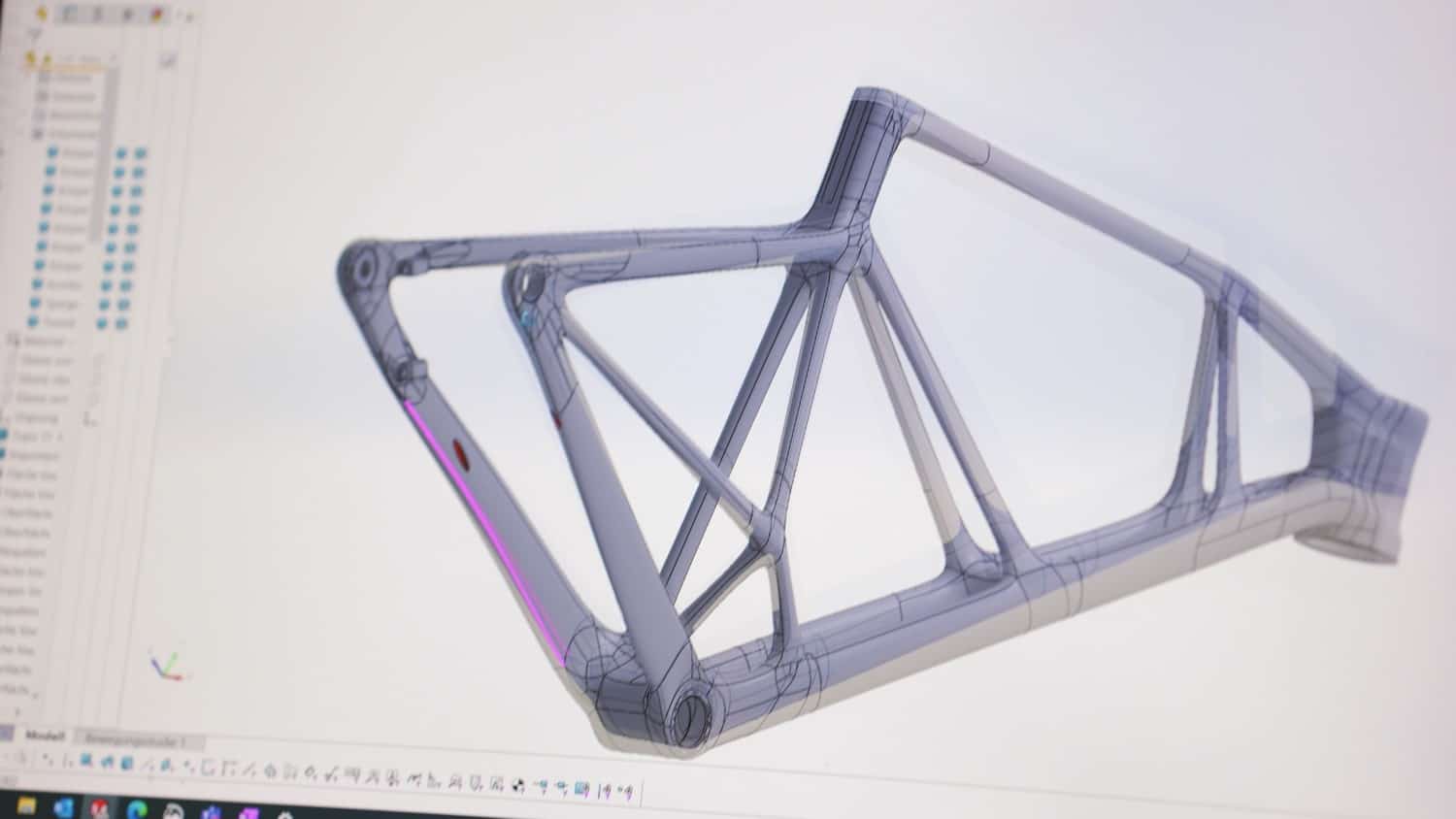
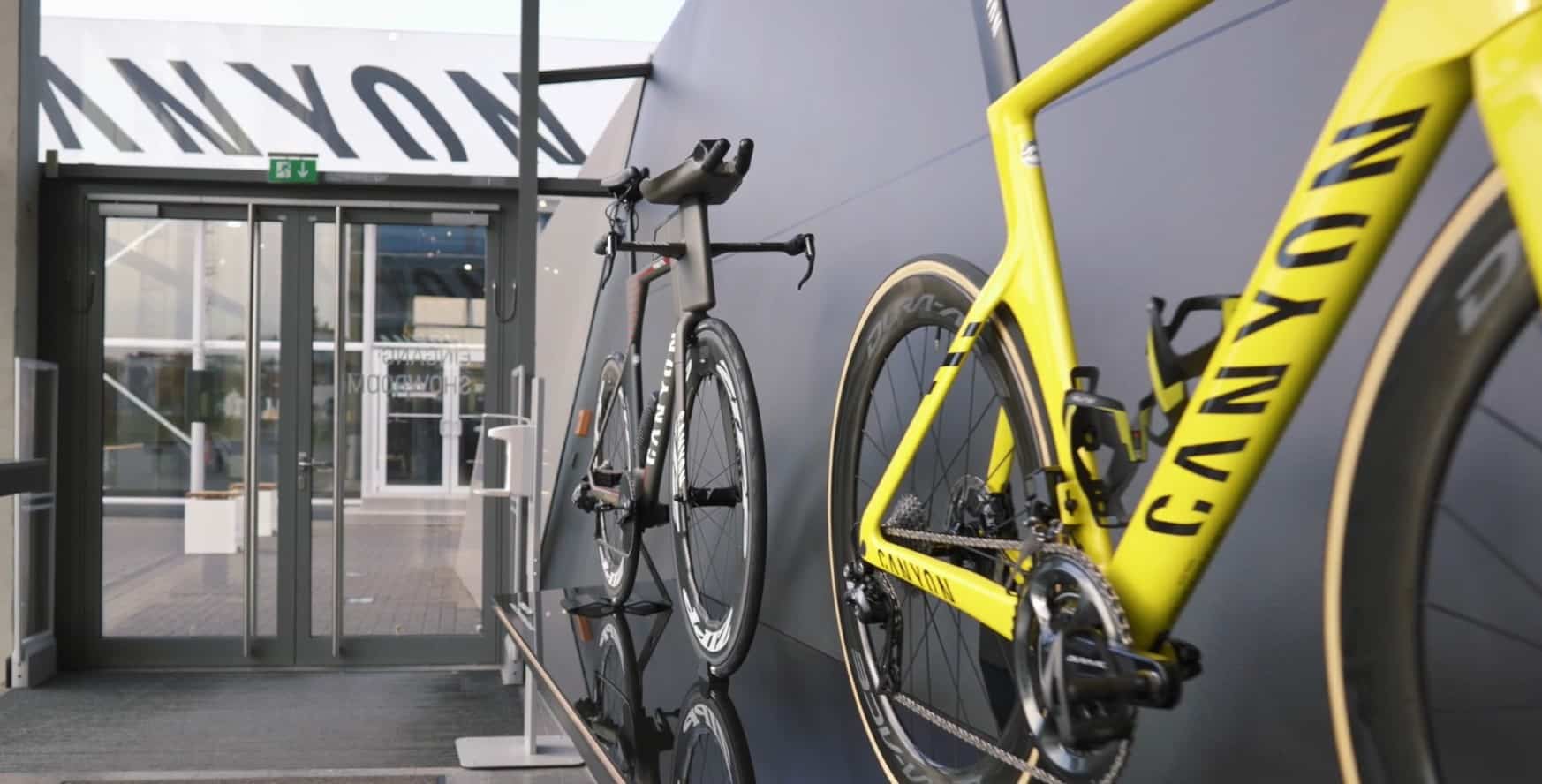
After a few post-processing steps like sanding, priming, and painting, the prototype looks like how the final bicycle frame will appear and is useful for collecting aesthetic opinions from colleagues and potential customers. In case adaptations are required, the 3D printer drastically shortens iteration cycles and, therefore, the time it takes until the next frame version is available. Costs for 3D printed prototypes are only a fraction of those made with conventional methods.
Development of sustainable frame concepts with the BigRep ONE
For an upcoming project, Canyon was forced to break new ground. The R&D department was tasked with developing a frame that should set a higher standard of sustainability, but this required solving several challenges. First, the frame should be made from only one easily recyclable material. Secondly, the frame had to be as rigid as possible for tough professional racing situations as well as improved handling for ambitious amateur rider. Finally, a maximum weight could not be exceeded.
To achieve all of these goals, Canyon used computerized topology optimization. After relevant boundaries had been set, the computer calculated the most ideal shape for the new bike frame. A number of changes and adaptations through many iteration cycles resulted in an optimized frame design that could actually be manufactured and was financially feasible.
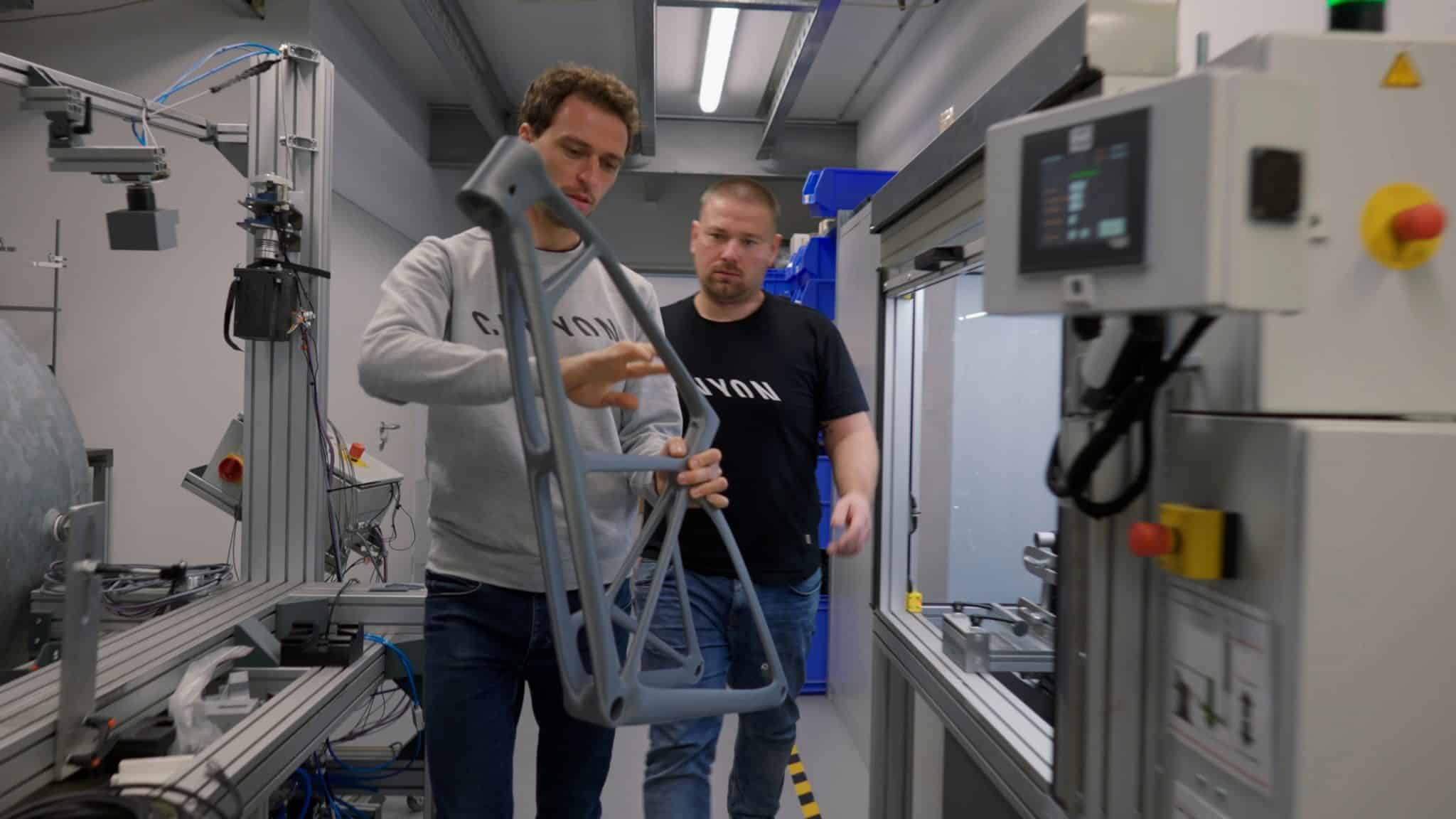
Without the 3D printer, iteration design process would not have been cost-efficient, or perhaps impossible. Johannes Thumm says, “3D printing already opened up so many cool chances to save time, to try new designs, extending all the possibilities of manufacturing.”
Future development of 3D printing in the bicycle industry
Aside from bicycle design, 3D printing will accelerate product development in many other industries. As product cycles become ever shorter and customers ask for more individualized products, additive manufacturing makes it possible to react quickly to changing market conditions. By combining computer-aided design processes and modern manufacturing technologies, products can be made which were previously unconceivable.
Original Article: https://bigrep.com/posts/design-innovative-mountain-bikes-using-3d-printing/
- Open and Safe
- Modular and Independent
- Semi-automatic print bed leveling
- Big, Bigger, the Biggest
- Spacious and Flexible
- Easy and Intuitive