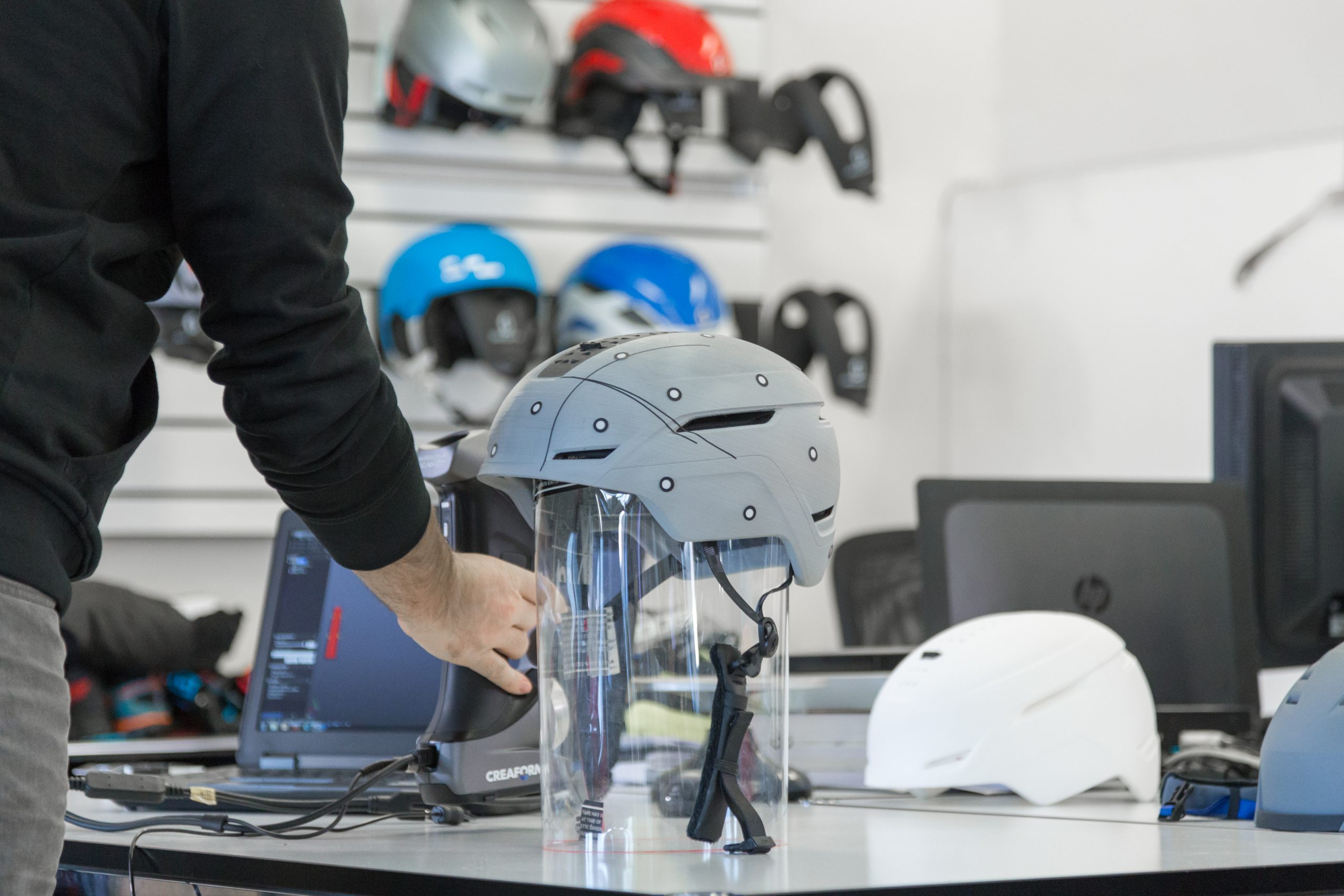
As 3D printing becomes more and more sophisticated, engineers and designers are increasingly relying on the technology to shrink their product development processes, quickly iterate new concepts, test prototypes, optimize designs and so much more.
In particular, 3D scanners, used in conjunction with 3D printers, offer the ideal turnkey solution for manufacturers and engineering services firms to effectively and quickly carry out product development projects and other industrial applications; by generating models from existing objects, companies can leverage the tremendous potential of 3D scanner-3D printer combos to revamp designs, create new parts to replace legacy components or even manufacture spare parts in a location that is closest to end-users.
While there are multiple inexpensive 3D scanners on the market, it is important to keep in mind that using low-end products for 3D printing prototypes or parts comes with a lot of disadvantages when compared with industrial 3D scanners. It is important to understand these inherent differences before acquiring a 3D scanner for any industrial application or industrial project.
For one, the complete 3D scan project duration, including the setup, scanning, and post-scanning operations can vary from one scanner to another. Industrial 3D scanners tend to require less time and easier setups. In addition, industrial 3D scanners have faster data capture and acquisition rates. For instance, the Go!SCAN 3D can capture up to 1,500,000 measurements per second.
This type of efficiency can be crucial when cycle times are short or when parts need to be printed quickly. In addition, the lack of capacity from low-cost 3D scanners to scan some surfaces or details can cause post-scanning processing to be six times longer versus industrial 3D scanners, such as Creaform’s industrial 3D scanners. This can, in turn, negatively impact team efficiency and timelines.
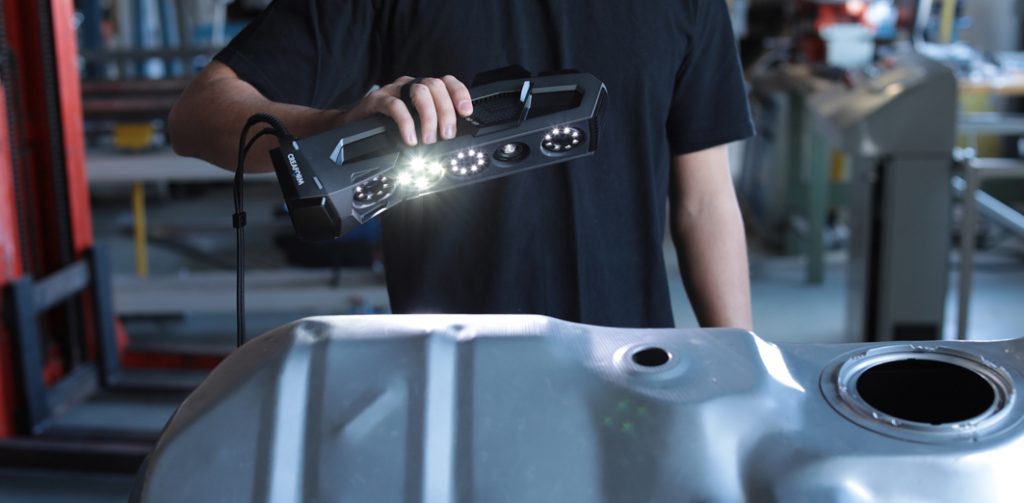
Another important factor when shopping for a 3D scanner? The level of accuracy required. For critical applications, including manufacturing new products and quality control—in which gaps as little as 0.05 mm can make a huge difference between a pass or fail—companies simply cannot rely on low-end 3D scanners to provide highly accurate results. A case in point? The HandySCAN 3D portable scanner has an accuracy of up to 0.050 mm (0.0020 in). That is a far cry from low-grade 3D scanners! For 3D printing applications, accuracy also means having more realistic scan models, as less surface noise is created. On low-end scanners, surface noise causes surfaces to be rough or details to be inaccurate or not perceptible.
The 3D mesh’s resolution is of equal importance. The last thing engineers and designers who work on complex projects need are low-resolution STL. Getting a higher mesh file resolution is totally dependent on the scanner capacity to detect small details but is also closely related to the equipment accuracy. Low-cost scanners tend to be unable to detect small details and instead often create incorrectly positioned or misaligned data, leading to an uneven, pixelated print. The Go!SCAN industrial 3D scanner provides a resolution up to 0.100 mm (0.0039 in), while low-end scanners can have over 10x less scan resolution capacity.
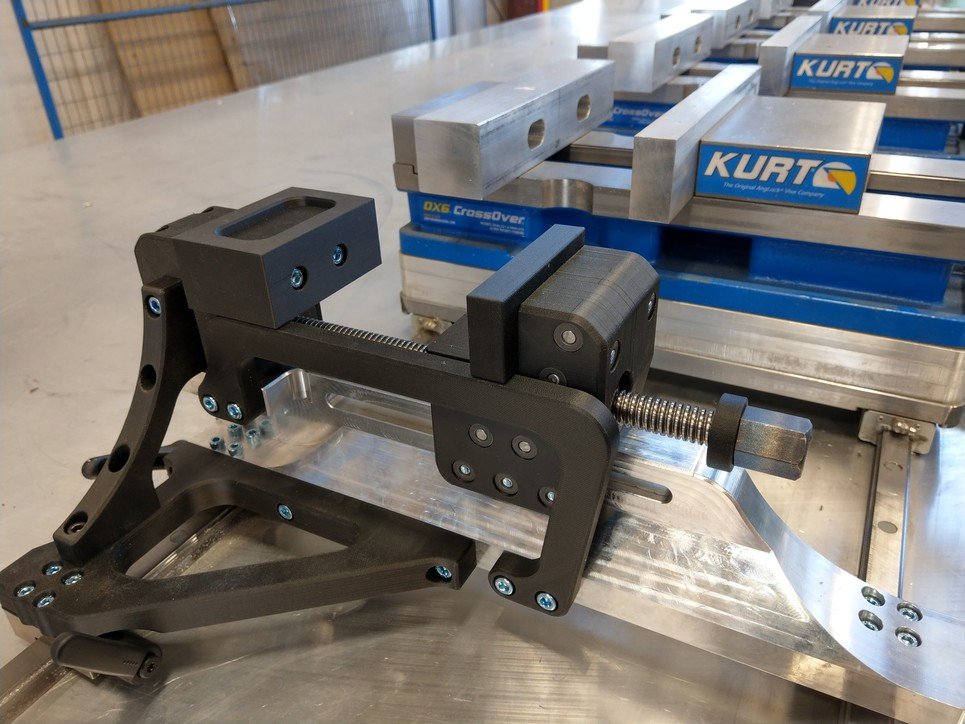
Versatility is the next thing to look for in your 3D scanner. High-end 3D scanners can scan a wide variety of different parts regardless of their materials, shapes, colors, or sizes. Some low-cost 3D scanners simply cannot capture data on materials such as machined parts and dark-colored surfaces. This means that unless you only need a 3D scanner for a very precise and basic application, you will limit your 3D scanning capabilities.
Contrary to low-cost 3D scanners, metrology-grade 3D scanners often come with easy-to-use software to facilitate finalizing 3D scan data to be sent directly to a 3D printer. Using scan-to-CAD software, such as VXmodel, users can edit meshes, ensure best-fit alignments, generate NURBS surfaces for characterizing freeform surfaces, and so much more. With such comprehensive features, engineers and designers can remain confident that whatever CAD files they send to their 3D printers, they will achieve the highest quality printed models they need for their projects.
At the end of the day, when choosing a 3D scanner to work with your 3D printer, you need to consider the industrial applications you work on. Low-end 3D scanners are ideal for simple, non-industrial applications and hobbyists. However, engineers and designers who work on industrial applications and need to print 3D models and parts can only rely on the levels of accuracy and resolution, and software features of industrial 3D scanners. While they may call for a more substantial initial investment—the performance and ROI are undeniable.