NASA’s Volatiles Investigating Polar Exploration Rover, or VIPER, is a mobile robot that will go to the South Pole of the Moon to get a close-up view of the location and concentration of water ice that could eventually be harvested to sustain human exploration on the Moon, Mars — and beyond. VIPER represents the first resource mapping mission on another celestial body.
If all goes as planned, VIPER will launch aboard a SpaceX Falcon Heavy rocket in November 2023. The launch is part of NASA’s Commercial Lunar Payload Services program, which contracts with commercial space companies to send vehicles to the moon to search for resources
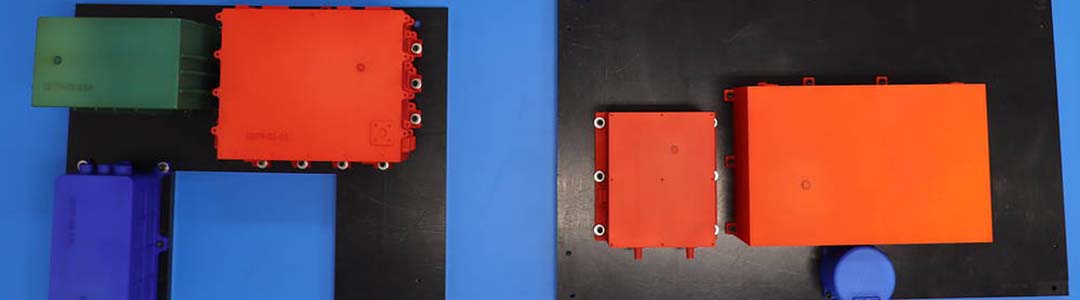
All the brightly colored plastic pieces might remind you more of something you’d find in a kids’ playroom than in a NASA clean room, but the team that built a full-scale replica of an early design of NASA’s Artemis water-hunting mobile Moon robot had some serious fun—while eliminating serious risk.
Using a mix of 3D-printed plastic and metal parts, the team walked through the meticulous and detailed process of assembling the science instruments and other critical rover components – like the wheels, lights, drill, and cameras – of NASA’s Volatiles Investigating Polar Exploration Rover, or VIPER. The rover is scheduled to be delivered near the western edge of the Nobile Crater at the Moon’s South Pole in late 2023 as part of the Commercial Lunar Payload Services initiative.
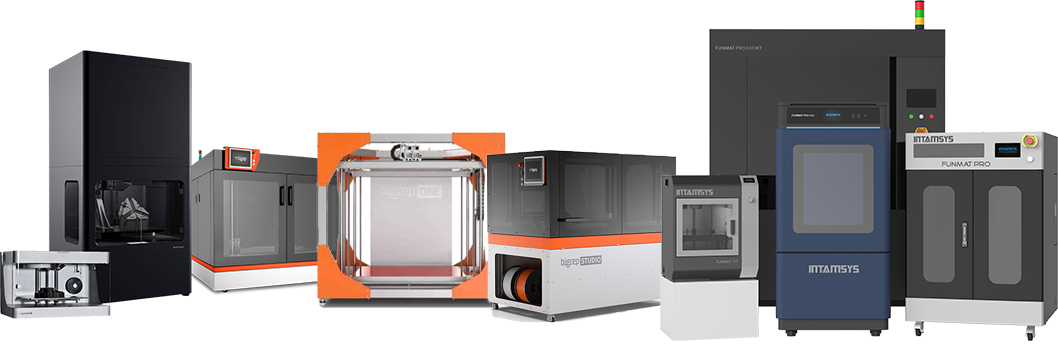
Piece by Piece
The golf-cart sized rover took shape during a recent practice build called the Surface Segment Assembly Pathfinder completed in the new clean room at NASA’s Johnson Space Center in Houston.
Composed of more than 100 parts and weighing in at 600 pounds, the pathfinder relied on a metal chassis and frame to give it strength and stability as engineers maneuvered it by crane or using a special lift-table. These tools provided engineers access to all the nooks and crannies in the belly of VIPER that they needed to reach to crank down fasteners, tighten bolts, and secure parts.
One unique feature of VIPER is its drill, which can reach depths up to three feet below the surface of the Moon in search of ice and other resources. Specialized training and equipment were required to elevate the rover so that the team could access and view the drill during the practice build.
“This pathfinder exercise allowed us the opportunity to make sure we have all the skills, tools, and accommodations in-place for VIPER’s flight-build, when keeping the pace will be especially critical,” said David Petri, VIPER’s system integration and test lead at Johnson. “Every detail counts, and this process helped reveal where the VIPER team could refine key design aspects to ensure a smooth build.”
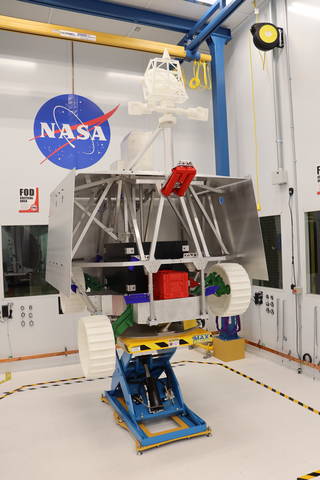
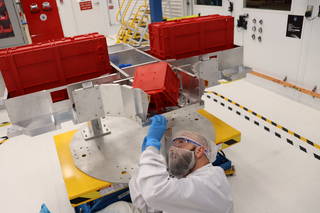
Credits: NASA/David Petri
It’s in the Details
The pathfinder build process revealed some tiny adjustments and improvements – like making sure the holes to connect separate parts align perfectly so bolts can slide through with zero resistance. The team encountered a few other challenges such as tool accessibility – and as a result made recommendations to slightly rotate instruments or move components so the actual flight-build will be easier.
“A good pathfinding exercise closely mimics the actual flight assembly and gives valuable experience as we capture each small step required to build the vehicle. This allows us to anticipate and work through potential roadblocks,” said Petri. “We’ve tested out our new facility and processes – and that’s important because even though building VIPER will be similar to things we’ve done for decades, every mission has elements that make it unique.
VIPER has recently passed his Critical Design Review, and now the actual flight parts and hardware manufacture will begin.
Original Source: https://www.nasa.gov/feature/ames/full-scale-artemis-rover-prototype-takes-shape