The brand’s Corvette, INDYCAR, NASCAR Camaro, and Silverado race teams have all contributed to the miles, leveraging 3D printing for components such as oil tanks, air conditioning cooling boxes, integrated hydration systems, headlight assemblies, and power steering pump brackets, among others.
“Chevrolet has a long history of technology transfer between our motorsports and production teams, and this is a perfect example of our approach,” said Jim Campbell, U.S. vice president of Performance and Motorsports at General Motors (GM), the parent company of Chevrolet. “GM’s 3D printing capability speeds up our learning cycles and, in turn, these racetrack experiences help our additive manufacturing team move one step closer the using 3D printed parts in production vehicles.”
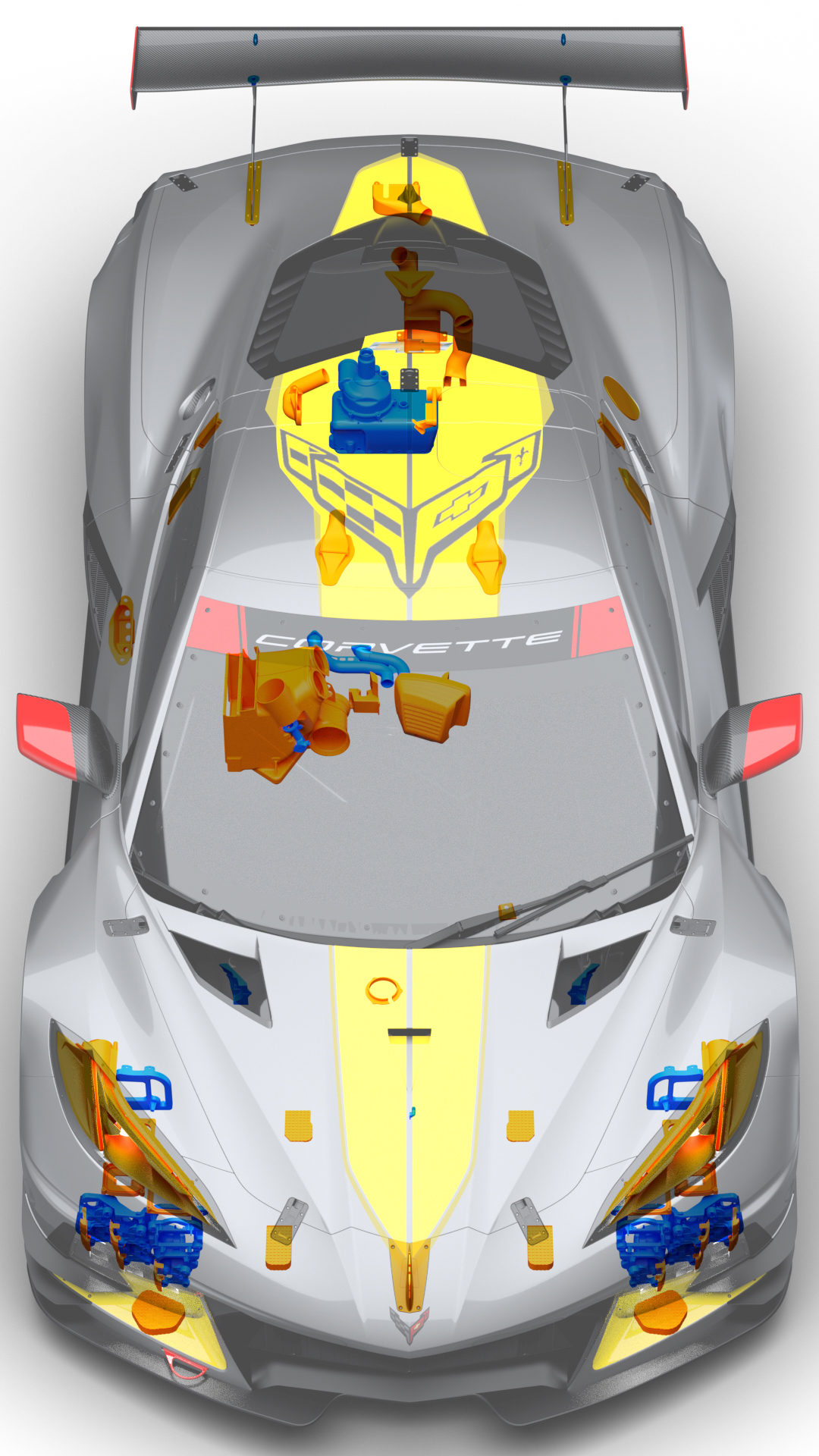
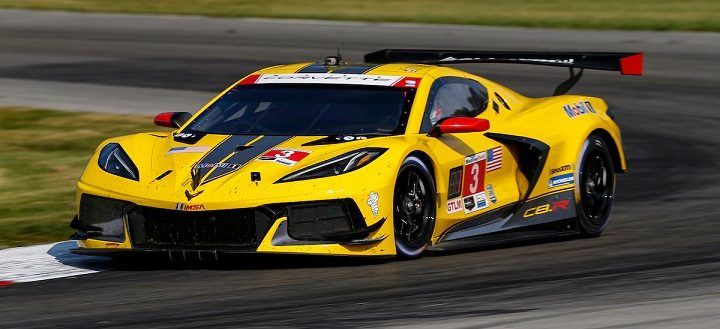
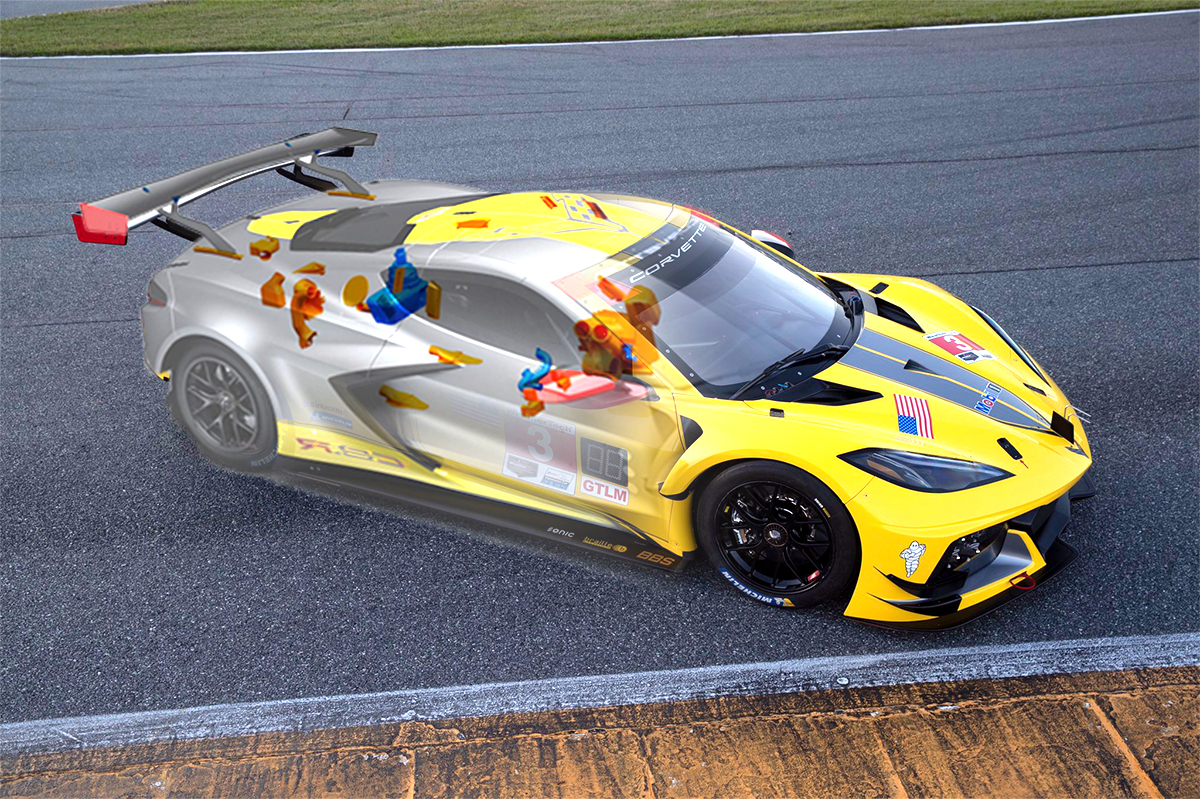
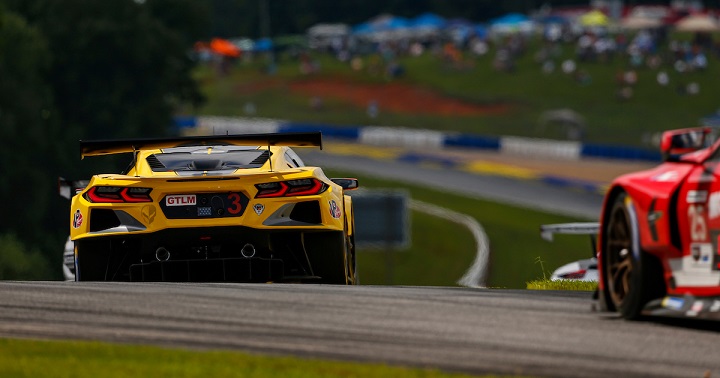
Two mid-engine Corvette C8.Rs debuted at Rolex 24 at Daytona on Jan. 25, 2020, each equipped with 75 3D-printed parts. Image via GM.
The Metal X greatly accelerates innovation,
delivering metal parts overnight using a new technology at a fraction of the cost. Create:
- Functional metal prototypes
- End-of-arm tooling
- Custom tools
- Complex bracketry
- Low-volume end-use parts
Chevrolet and 3D printing
Accumulating some 8,000 miles of competition in seven races this season, Chevrolet’s two new mid-engine Corvette C8. R race cars are each equipped with 75 3D printed parts, 50 of which were designed or printed in-house by GM. The C8. R debuted in January this year at the Rolex 24 at Daytona, finishing fourth in its maiden race. The vehicles contributed to a dominant racing season for Corvette, taking home five first-place wins and three 1-2 finishes.
Chevrolet’s INDYCAR program has also borne the fruits of leveraging 3D printing within its Indy V6 race car. The vehicle’s exhaust system contains 3D printed components to help eliminate failure points seen in traditionally manufactured components, in addition to reducing costs and increasing design freedom. Since the racing season kicked off at Genesys 300 in June, Chevrolet INDYCAR engines have racked up over 60,000 miles.
Meanwhile, Chevrolet’s Silverado off-road race truck features three 3D-printed parts made in-house by GM, including a carbon-fiber reinforced plastic rear damper shield designed to protect the truck from rocky desert terrain. Since October last year, the truck has seen 900 miles of competition across six races.
In NASCAR, Chevrolet engineers optimized the aerodynamic performance of its Camaro ZL1 1LE race car through extensive wind-tunnel testing, putting over 500 3D printed prototype parts to the test to develop the ZL1 1LE’s body. The car is also equipped with a 3D printed gear cooling duct, which has seen action in 27 races totaling 18,500 miles.
“By utilizing 3D printed parts, Chevrolet Motorsports is demonstrating the many benefits of additive manufacturing, including manufacturing efficiencies, mass reduction, parts consolidation, creativity and cost savings,” said Audley Brown, GM director of Materials Engineering, Additive Design and Manufacturing. “3D printed parts can offer equal strength and durability to cast or milled components, which is critical for product development and design.”
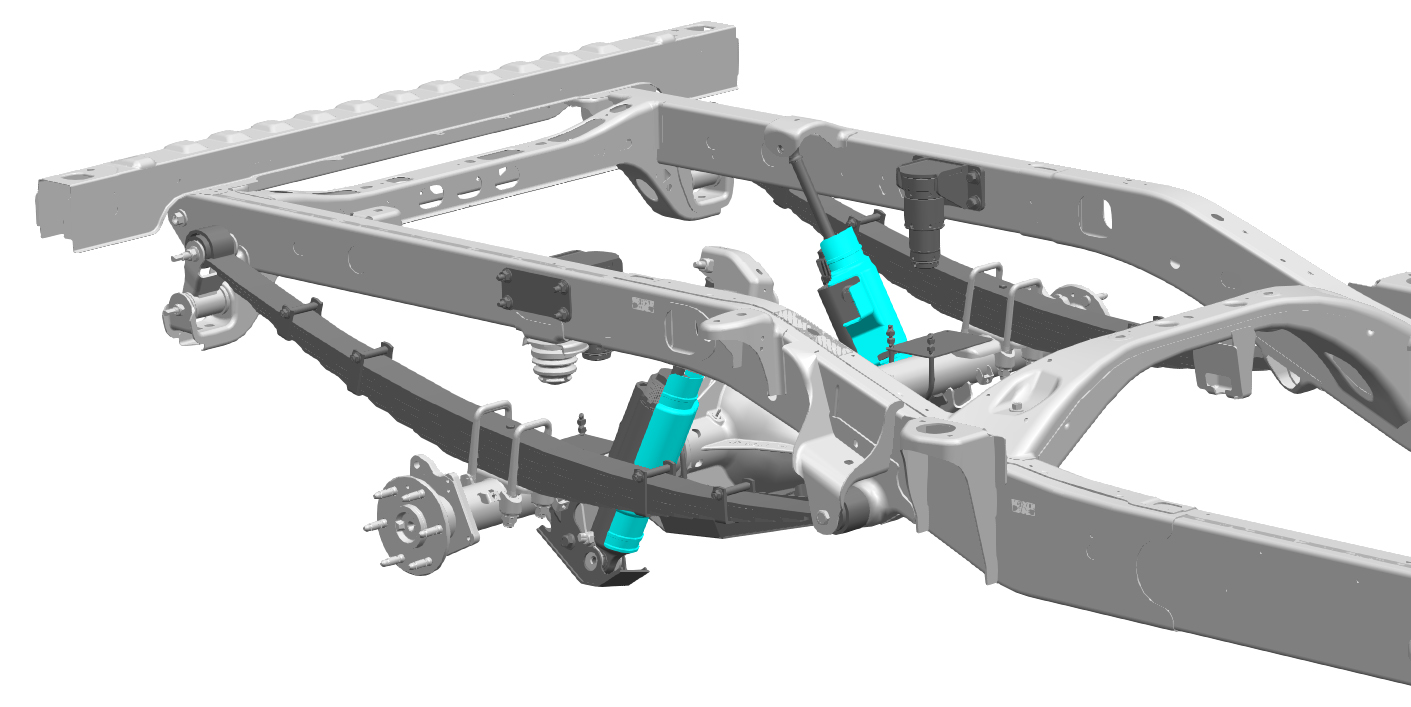
The Silverado race truck has three 3D-printed parts made in-house by GM, including the rear damper shields. Image via GM.
3D printing in Motorsports
3D printing has been a gamechanger for the motorsport industry in recent years, significantly reducing the costs of expensive bespoke, one-off components while providing a cheap and speedy method of producing prototypes for testing and research and development (R&D). And GM isn’t the only automotive firm leveraging the opportunities presented by additive manufacturing.
In the student racing realm, college team Hornet Racing improved the engine performance of its competitive car by 43% using Carbon DLS 3D printing technology in 2018. More recently, fellow Spanish student racing team ETSEIB Motorsport incorporated additive manufacturing to customize their electric cars for this year’s Formula Student, printing end-use cooling ducts for brakes via Fused Filament Fabrication (FFF).
In the UK, British engineering consultancy firm KW Special Projects (KWSP) secured funding last year to establish a 1,657 square meter Digital Manufacturing Center in Silverstone Park to provide automotive SMEs with access to additive manufacturing equipment and guidance.
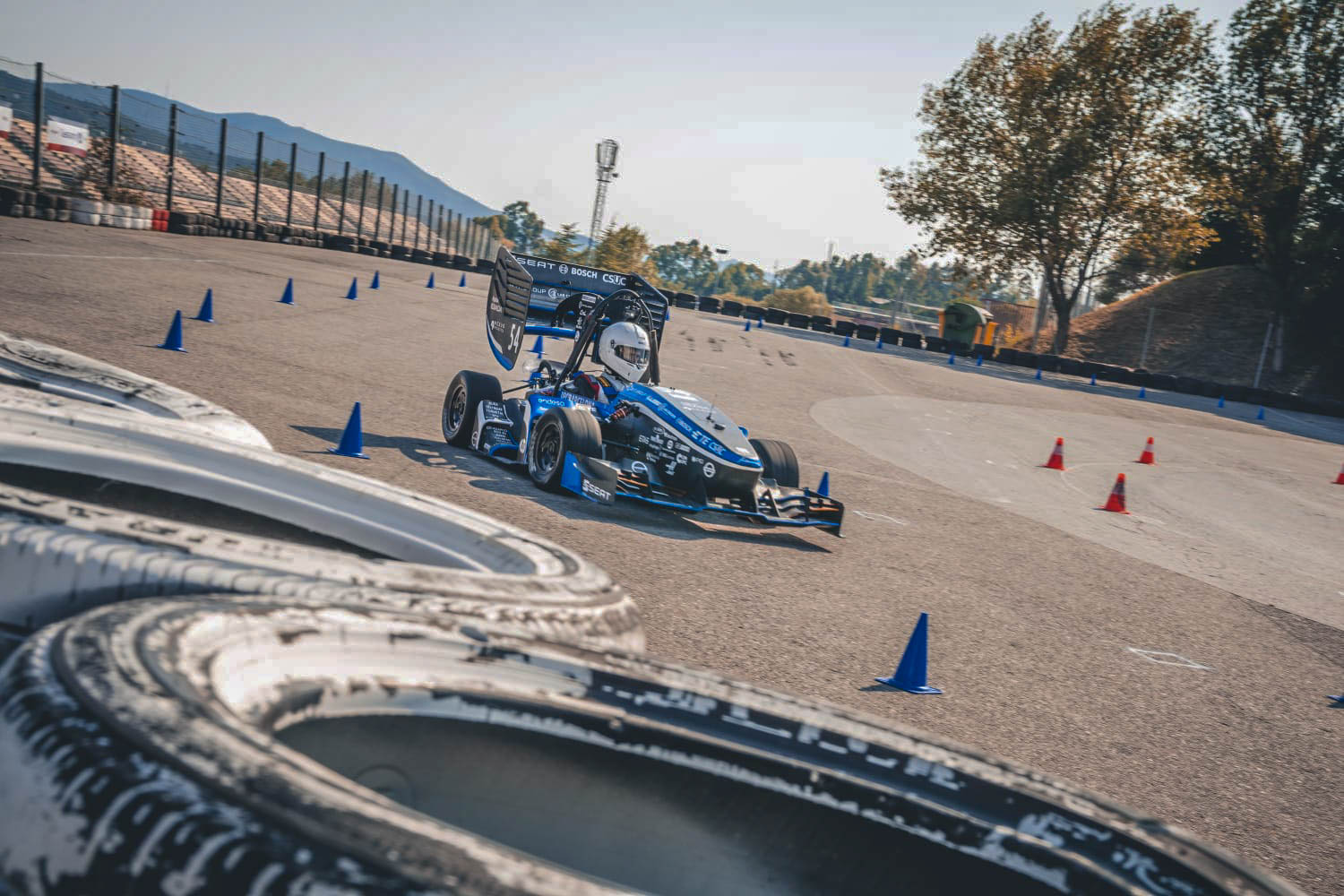
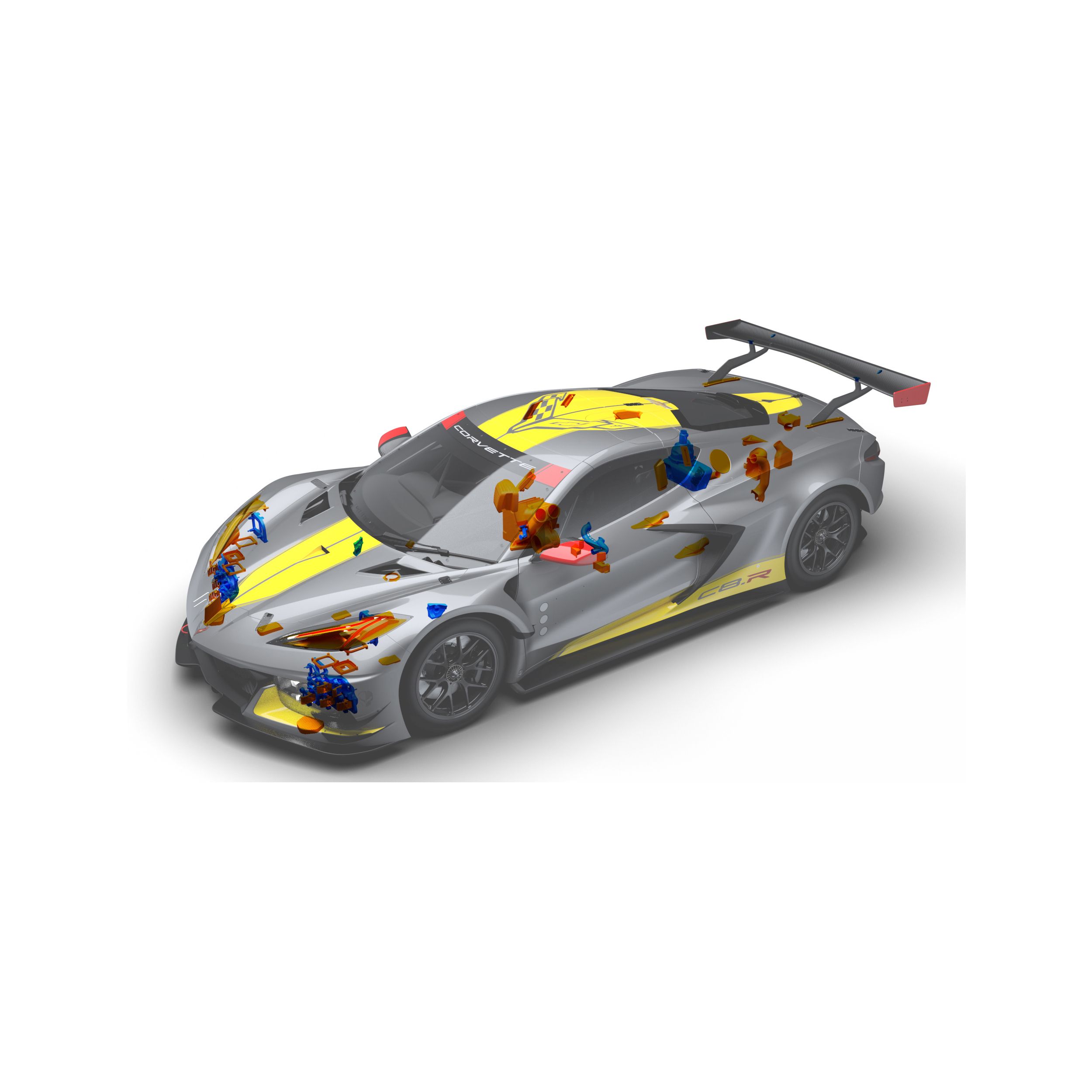