A research team from the US Air Force (UAF) has successfully produced a surgical retractor using 3D printing.
The medical instrument created using a desktop 3D printer, is designed to be used in logistically challenging hostile environments where it is not possible to restock medical supplies using conventional methods.
It has been produced as a proof of concept, with the aim of establishing a digital library of 3D files, which could be used to produce 3D medical instruments. This would enable deployed medical personnel to download and produce a range of medical equipment, on-demand, anywhere in the field.
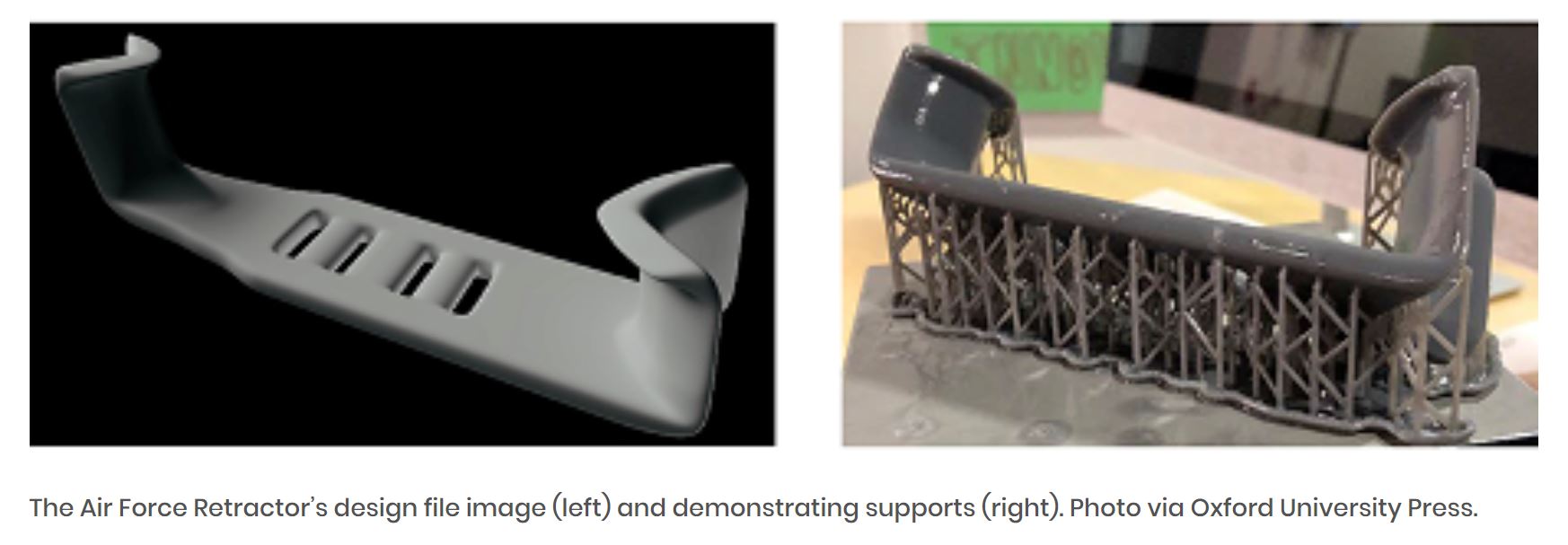
The “Air Force” retractor
A surgical retractor is an instrument used by field doctors to separate the edges of a wound or incision, in order to conduct surgery on an injured body part or limb. In what the US military describes as an anti-access or area denial (A2/AD) region, the dangers necessitate the need for such medical tools to be readily available.
The 3D printed retractor is therefore designed with field use in mind. It consists of two parallel blades of different sizes, with one designed for narrow wounds, and the other for cases requiring broader access. It has downward-angled curved blades at each end to facilitate entry and instrumentation, which has earned it the nickname of the “Air Force Retractor,” due to the similarity of the retractor blades to the swept wings of fighter aircraft.
The device was produced with grey resin, which is general-purpose and often used for prototyping. In order to gain FDA approval, the instruments will need to be produced on resins that can be sterilized such as Dental SG Resin; a durable biocompatible material for dentistry, has been identified as a strong and durable enough biocompatible material, and the team intends to use it in future iterations.
Using the free online design tools to create and modify the 3D file for the project, the team was able to produce the instruments with no formal training, and without incurring the associated training costs. These programs prepared the 3D model for printing, ensuring that the scaling, resolution, and orientation of the model were correct, and added supports during the printing process where necessary.
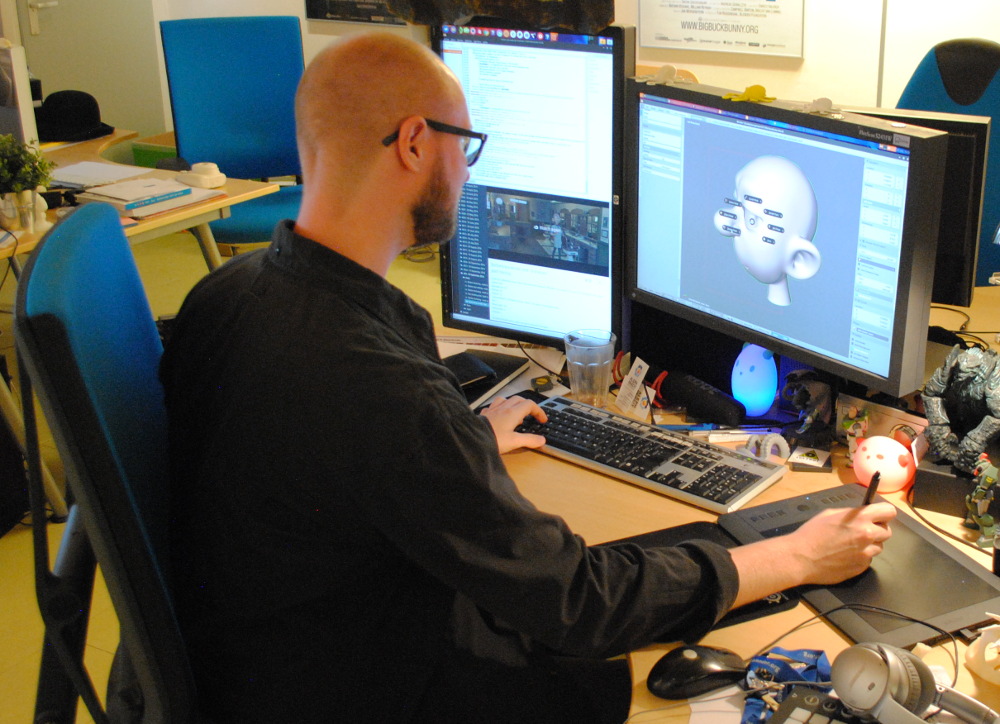
The next step for the program is to attempt to patent the technology and gain FDA approval to produce the instruments using stainless steel and a radiolucent polymer. The team ultimately aims to replicate the results of a different study, in which a spine localizer was 3D printed and assembled at a medical facility, by either establishing an online repository or creating locally stored files to produce other medical devices on demand.
The research team acknowledged that challenges exist to this strategy including production time, portability of the 3D printers, limits to the size of the instruments produced, and training required to use the printers. However, they remain confident that the technology could be used to replenish supplies within hours, or even create novel products such as prosthetics if the need should arise.
The findings of the project are detailed in a paper titled “An Example of 3-D Printing for Expeditionary Medicine: The Air Force Retractor,” which was published in the Military Medicine journal. It is co-authored by James A Chambers, Kenneth P Seastedt, and Jocelyn Raymundo-Grinstead.