The Blowtech Group is a Scandinavian industrial concern, with two equal industrial plants, one in Norway and one in Sweden, that specializes in plastic blow molding. The blow molding of plastics operates on similar principles to glass blowing, but with industrial precision. The technique can be divided into two areas: technical shaping and package molding. It is of very practical use, particularly when producing polymer products of complex shapes. Examples of blow molded products range from the simple everyday shampoo bottle to air ducts used in vehicles.
The Need for a New Metrology Solution
In 2020, Blowtech Sweden decided to invest in a HandySCAN 3D from Creaform, who is represented in Scandinavia by MLT Maskin & Laserteknik AB. The objective was to get a small handheld tool to quickly carry out inspections and measurements in various places. The speed of measurement, getting results in a short time and the desire to use cutting-edge technology were the key factors to choose a 3D measurement solution.
Before having the HandySCAN 3D, the company had only two options for carrying out inspections:
- Send the parts to their sister company in Norway
- Ship the parts to an external service partner
Both options were far from ideal, as they were really time consuming; the measurement process could take several weeks due to shipping and lead time.
3D Scanning Advantages and Benefits
The process of plastic molding typically requires multiple iterations to fine-tune the manufacturing process. Plastic material shrinks during cooling and that changes the shape of the part. It can take several hours for the material to settle and for the final shape to be known. For each change Blowtech needs to know the impact on the final part after cooling. Only then can the machine settings be adjusted.
With the in-house capacity of a 3D scanner, each iteration is realized much faster.
Now, a plastic part is produced and cooled, scanned with the HandySCAN 3D and compared to the 3D documentation from the customer. If needed, the parameters of the production machine can be adjusted immediately. Another part is then quickly produced, then goes through this process again to get a clear picture of how the adjustments affected the part. This can be ongoing for several days.
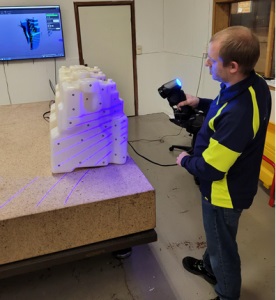
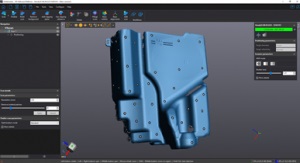
Before having the portable 3D scanner, this process could take weeks to complete as Blowtech had to send the part outside the factory for measurement. In terms of ROI, the time from the beginning up to the adjustment of the process was reduced by about 50%, and the cost for external measurements also went down.
The implementation of the 3D scanning technology was easy, and to ensure a perfect handling process, Blowtech split the users in two groups: some are in charge of the scanning only, others manage scanning and evaluation. The company mentions that it was very easy to teach new users, since everyone appreciates the modern, advanced and easy-to-learn technology.
For the future, Blowtech is looking for further process improvements, but the HandySCAN 3D will certainly be an important part of new project developments.
Original Article – https://www.creaform3d.com/blog/plastic-molding-firm-reduces-process-time-by-50with-3d-scanning/?fbclid=IwAR1nd0cEZ-5_8Rz5lGe0BvdFJt3BZN1zWXN-09M2ADCv-dWrIN8RXM8qKww
Ask us about 3D scanning services and equipment!
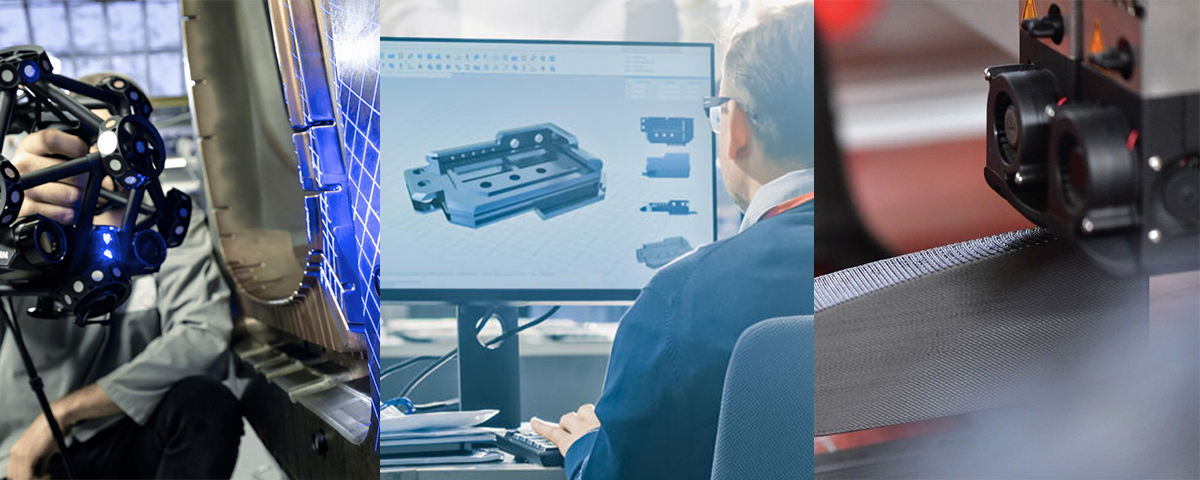