Here, precision meets performance as complex intake manifolds for aircraft engines are forged with unparalleled efficiency and accuracy.
Undertaking the project of crafting intake manifolds for a specific aircraft engine proved to be a significant endeavor for the institute. These manifolds, crucial components within engine systems, play a pivotal role in overall engine performance. Yet, their intricate design posed numerous challenges during development, including the complexities of mold-making, high costs, and the labor-intensive vibration welding process. Consequently, this resulted in prolonged lead times and decreased efficiency in product development.
In response to these obstacles, the institute embarked on its maiden voyage into direct production of intake manifolds utilizing FFF 3D printing technology. Following a thorough examination of various FFF 3D printer brands based on material performance, equipment capabilities, and service support, the institute selected the FUNMAT PRO 610HT 3D printer from INTAMSYS, paired with PEEK-CF composite material, for its product development and application.
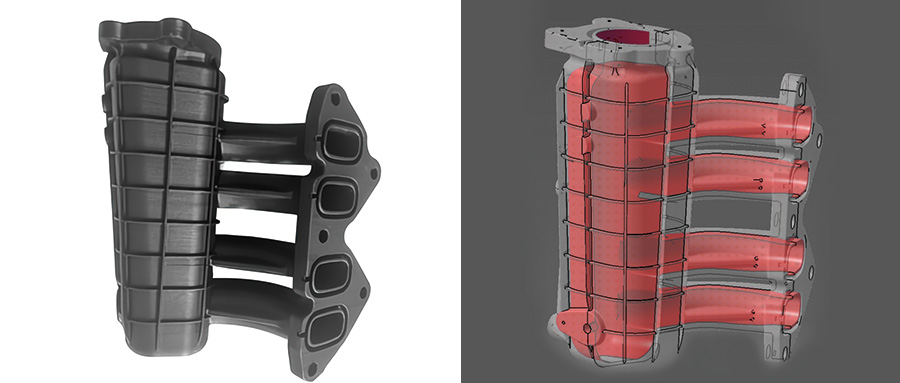
Final 3D Print
CAD Model and Internal Structure
As a high-performance FFF printing equipment, the FUNMAT PRO 610HT is mainly designed for printing high-temperature thermoplastic materials such as PEEK, ULTEM, and PPSU. It can handle a wide range of thermoplastic materials available in the market, including custom ones. Its constant temperature chamber ensures excellent performance when printing high-performance materials. With duel-nozzle heating temperature of up to 500°C and a chamber temperature of 300°C, it can print high-temperature materials without distortion, ensuring wrap-free printing while effectively melting most thermoplastics.
The final 3D printed component measures 218.4×216.4×95.4mm. Developed jointly by experts from the insitute and engineers from INTAMSYS, the design was optimized for manufacturing (DfAM), and printing processes were adjusted for the following improvements:

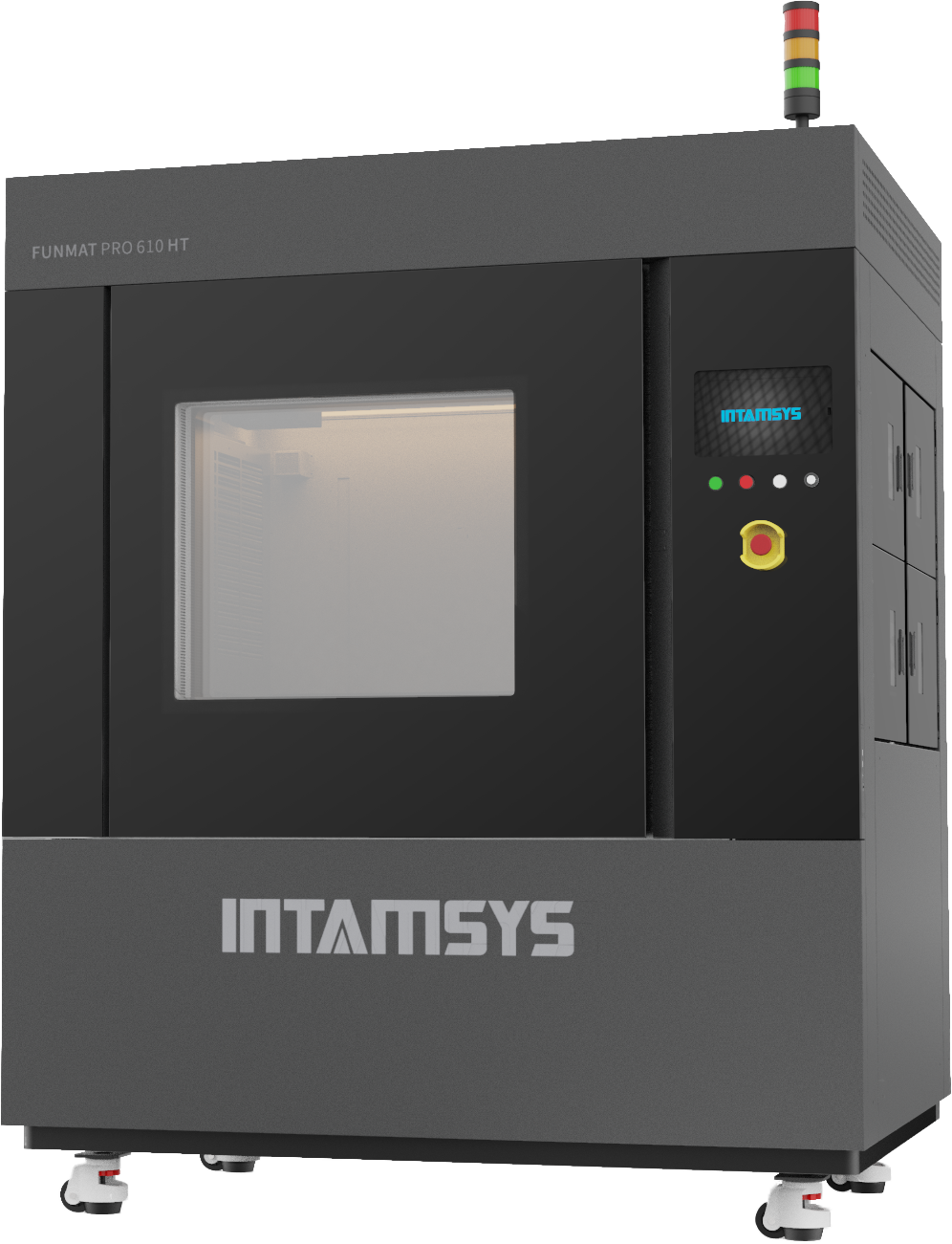
Get Started 3D Printing Like a Pro
This open platform is one of the key factors in selecting your preferred material, and have a choice because users have control over all parameters including filaments’ properties and printer settings. We encourage you to get in touch with us today for more details on how to get one of the top modernized 3D printers in your office, program, or facility — INTAMSYS 3D Printers.
When considering manufacturing efficiency, if this part were made using traditional injection molding processes, it would require tooling costs of about $27803, with a 45-day lead time for tooling. However, with 3D printing technology, the product can be seamlessly manufactured as a single integrated piece, reducing costs to only one-tenth of traditional methods, and shortening the production lead time to just 4-7 days.
EXPLORE INTAMSYS 3D PRINTERS
Not sure which 3D Printing solution is right for you?
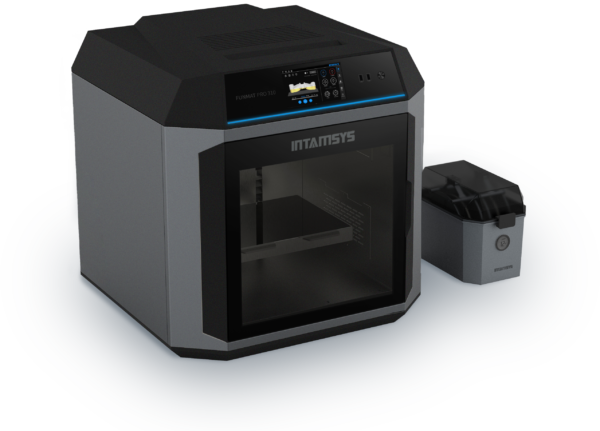
FUNMAT PRO 310
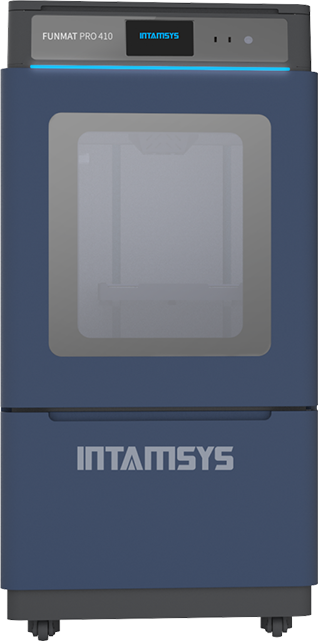
FUNMAT PRO 410
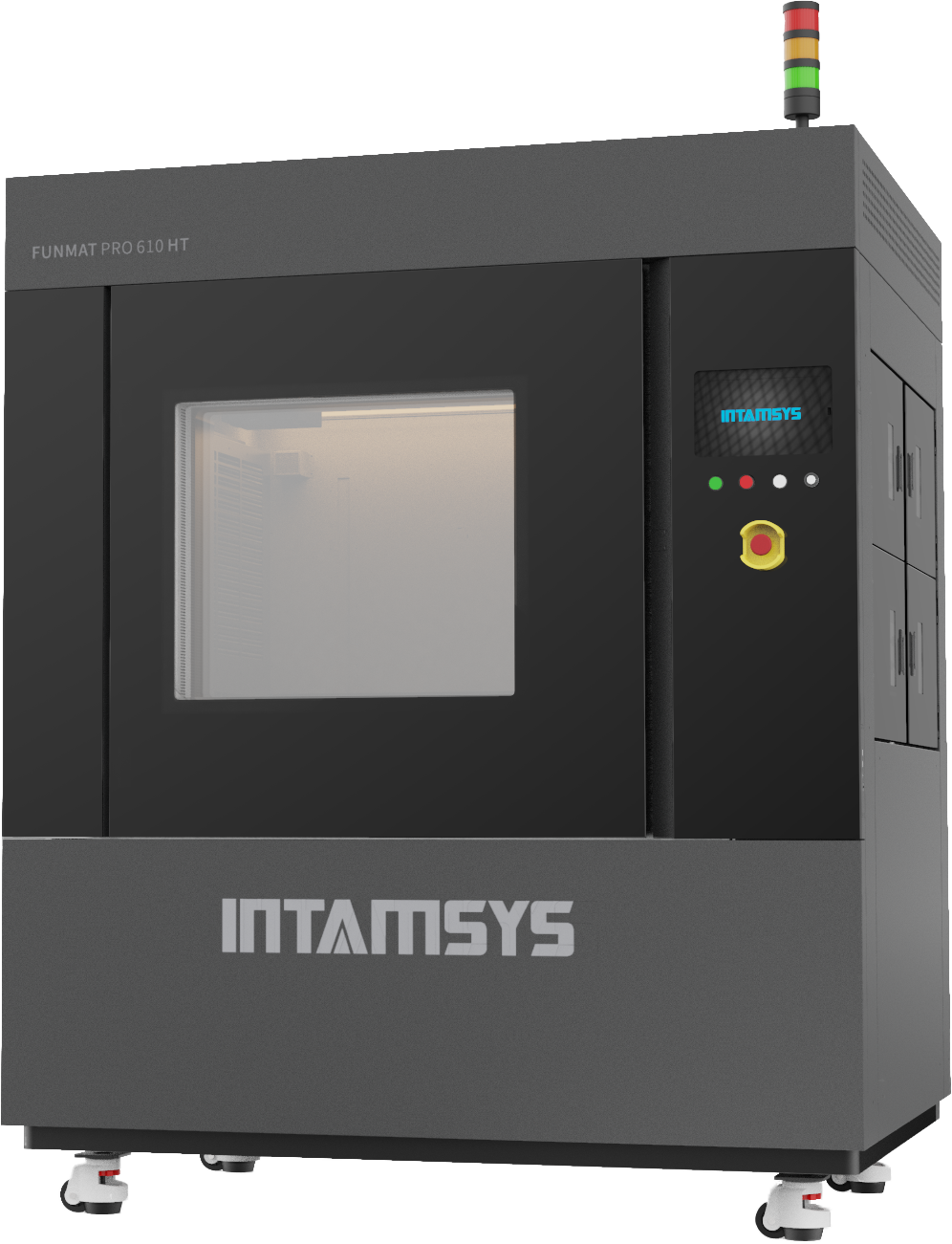
FUNMAT PRO 610 HT
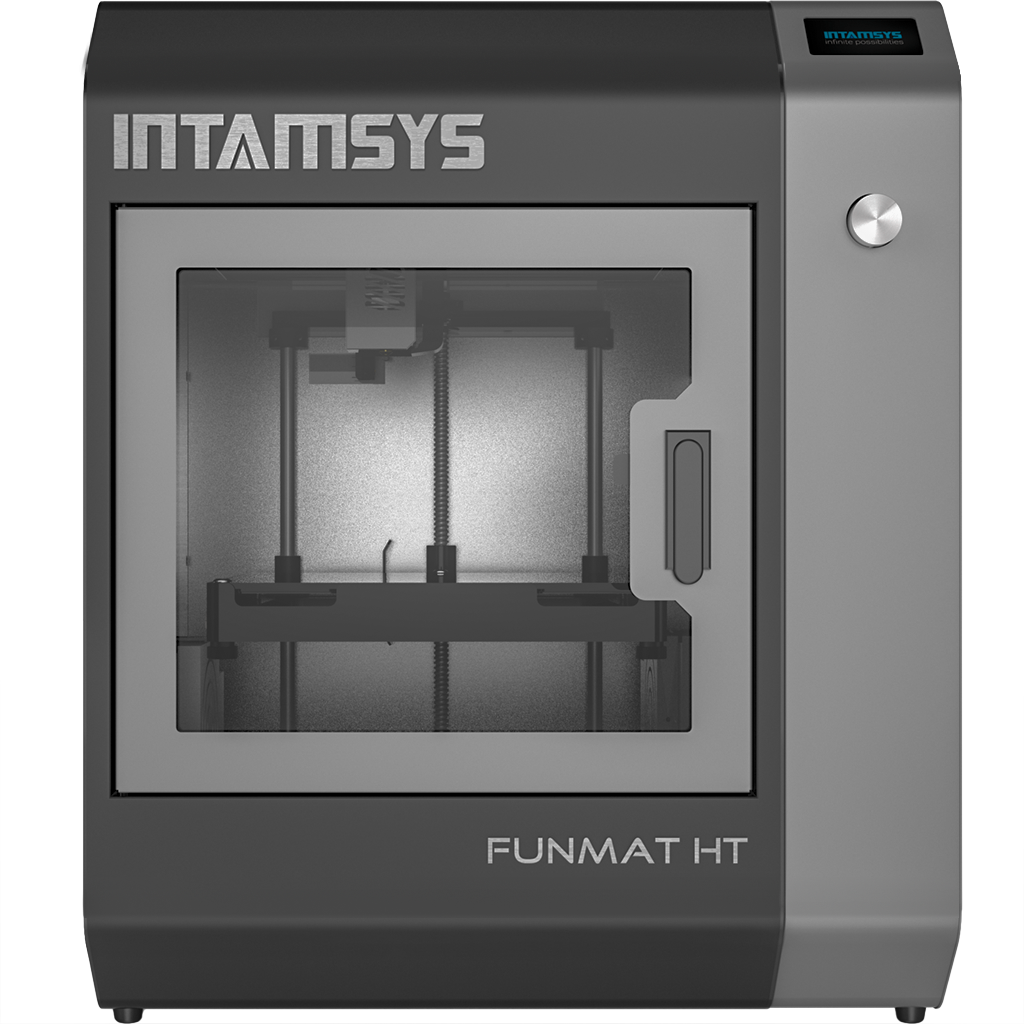
FUNMAT HT