Problem:
Turbine components wear over time and require replacement. OEM’s typically charge a premium for spare parts and CAD data.
Traditional Method:
Cutting the blade into several pieces to generate the cross sections. Then the cross sections would be put into CAD. This method needs a donor blade which in many cases may not be available. It is also subject to human error while capturing and inputting the cross section data.
NeoMetrix Solution:
- Original blade is Scanned in house using the Konica-Minolta Range7 (Figure 1)
- Scan Data is registered, merged, and aligned in Rapidform XOR. (Figure 2)
- Multiple cross-sections are cut in order to develop a parametric solid in Rapidform XOR
- Final model is transferred to Solidworks using “Live Transfer” in order to maintain parametric history.
NeoMetrix Advantage:
- Complex contours and geometric features are accurately modeled in CAD.
- Solid model can be used for CNC machining, 2D Drawing development, and FEA analysis.
- Complete model history allows for future design changes.
Get Started Today!
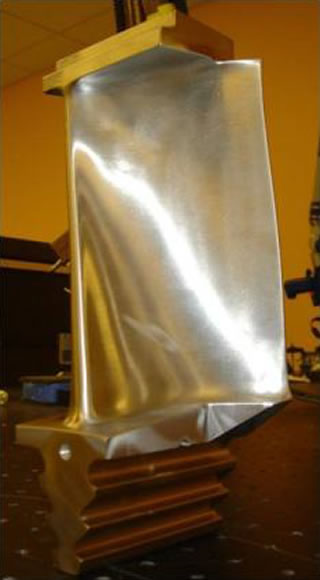
Figure 1 – Original Part
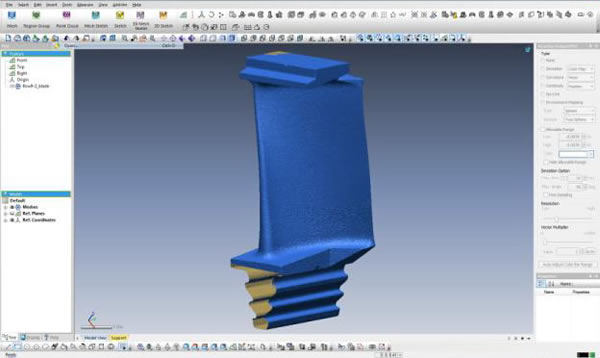
Figure 2 – Laser Scanned Data
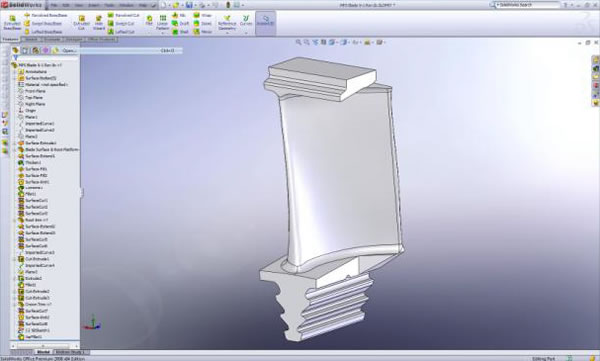
Figure 3 – Parametric CAD Model in Solidworks