Reverse Engineering a Motorcycle Rim
The Problem:
A customer damaged his motorcycle wheel in an accident. If it was a standard off the shelf it would be no problem to get a replacement. However, the customer’s wheels are one of a kind and cannot just be bought. The only option is to have a new wheel fabricated, and no 3D data or drawings exist.Traditional Method:
Traditionally, the new wheel would need to be re-designed from scratch. The only point of reference is the damaged wheel, which would need to be measured by hand. With something like a wheel that has complex curves and geometry, to get accurate measurements can be almost impossible. It is a very time consuming process that still does not result in a perfect reproduction. A skilled artist would be able to get it very close, but this would be very expensive.NeoMetrix Solution:
Through the use of 3D scanners and reverse engineering software, we can produce an accurate replica. This replica will not include any of the defects due to the damage on the original wheel, but will have all the key geometry. The Creaform Handyscan is a handheld scanner that uses laser light and cameras to capture surface geometry. The object is covered in reference dots to assist the scanner with positioning, so no turntable or other reference fixtures are needed. First, reference dots are placed on the wheel. Then the wheel is scanned in 3 different orientations to ensure the capture of all geometry. Each scan is a mesh of triangles. These scans are then exported as STL files and are ready for import into reverse engineering software. The 3 files are then imported into Geomagic Design X, which is a powerful reverse engineering program. The 3 scans are aligned to eachother and merged into one clean scan. Using tools in Design X, then wheel is fully modeled from the scan data. This model is then exported as a 3D solid model and delivered to the customer.NeoMetrix Advantage:
Reverse engineering from scan data guarantees a much more accurate recreation of an object than any other method. Additionally, there is an immense amount of time saved with this method, when compared to traditional measuring and reverse engineering methods. The customer receives a 3D CAD model for what was previously a one-of-a-kind part with no easy way to make a replica or replacement. If he ever needs to make another replacement in the future, he has the file. Additionally, if modifications ever need to be made, the file can be edited in any major CAD software. The time and money saved up front is only a portion of the savings from getting a part 3D scanned and reverse engineered.
“My quote was incredibly cost-efficient. The services included, 3D imaging, reverse engineering, duplication, 3D modeling, drawings & outstanding technical assistance – which includes different format files for machining manufacturing – for all components of the complex wheel and the wheel components, as well future alterations to the wheel and it’s components dimensions as needed.”
-Steven Stiles, Customer
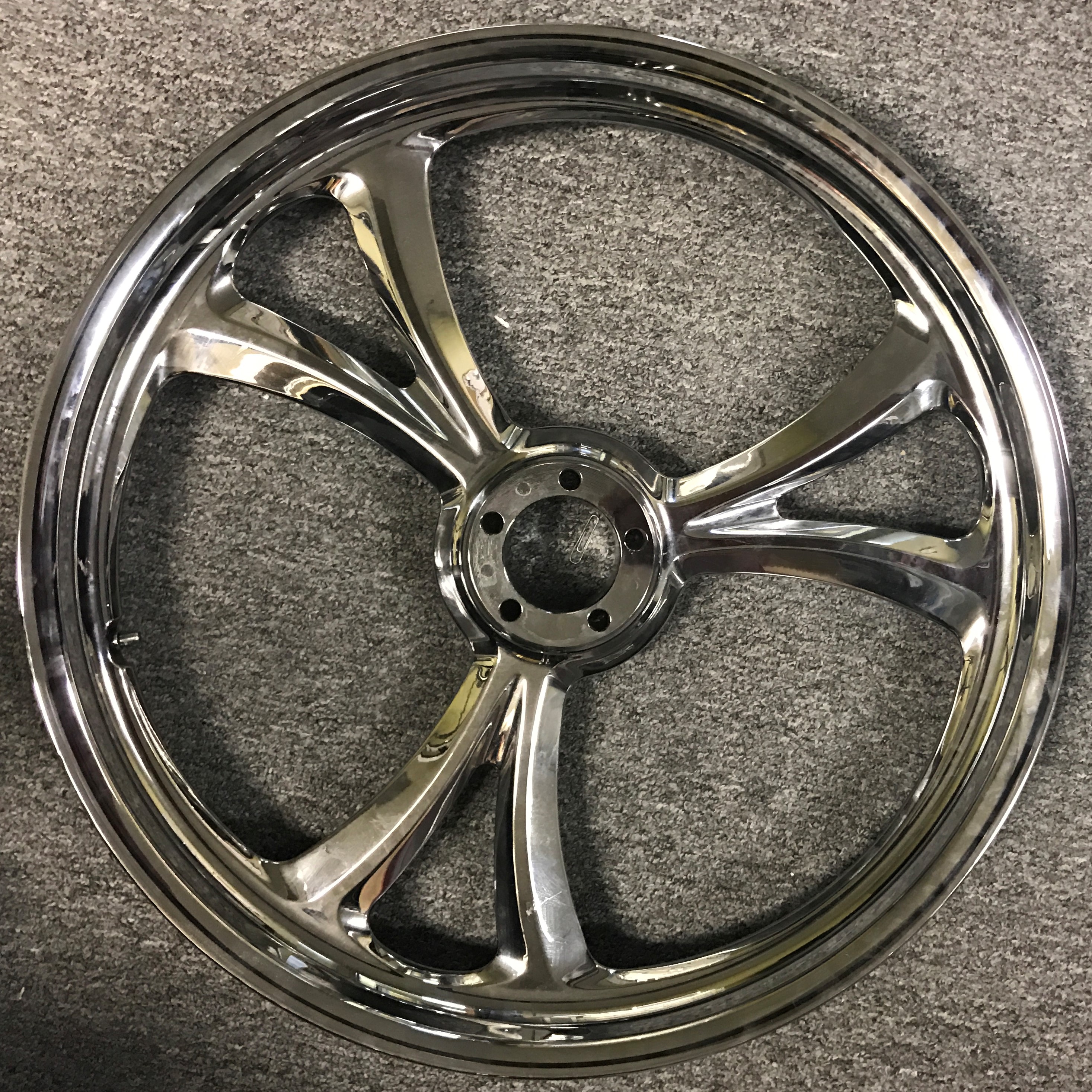
Original Motorcycle Rim
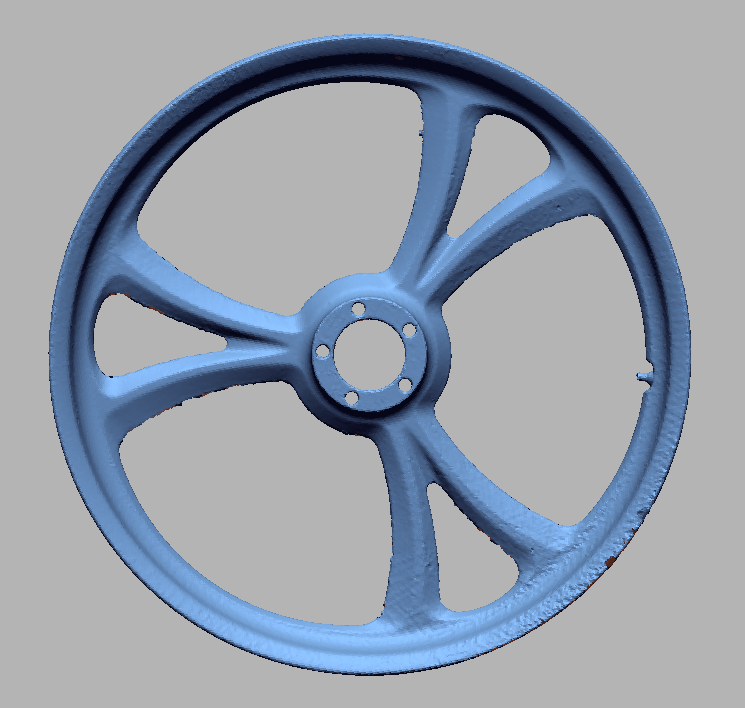
Scanned Data
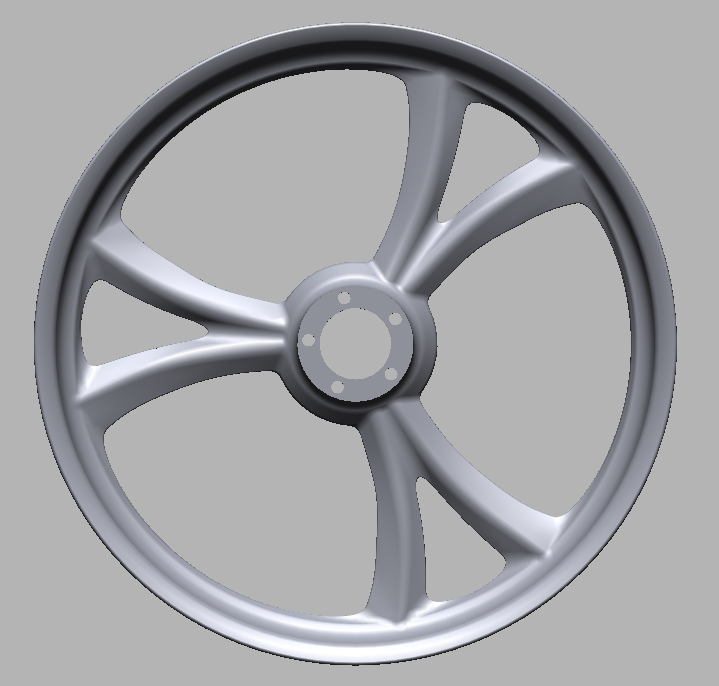
CAD Model
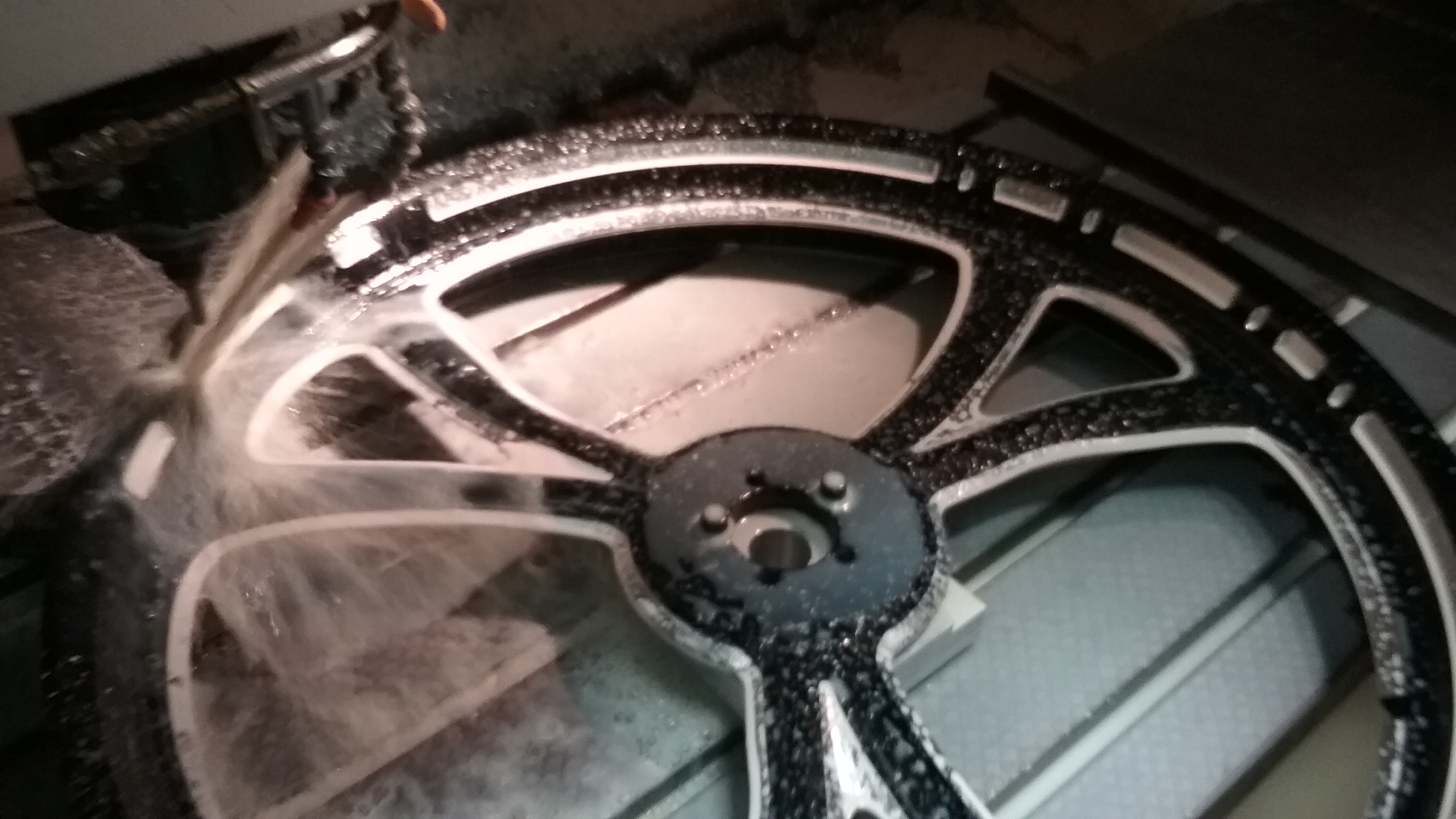