Development of Quick Connect Prosthetic Joint
Triple amputee contracts NeoMetrix to help him further his triathlon competing dream.The Problem:
Rajesh Durbal is an ordinary man looking to pursue his dreams of being a world class triathlon athlete. Triathlons are all about speed and being able to transition from one sport to the next. The problem was Rajesh’s prosthetic joints took a lot of time to switch out for different foot attachments. For him to be able to really be able to compete, that transition time would need to be made a short as possible. In theory, new joints could be ordered and used as replacements. However, there were no other joints available for this type of situation, so a new design would need to be developed.
Traditional Method:
Traditionally, the original joints would need to be measured with calipers, from those measurements a CAD model would need to be created, and from that a model would be made. The model would be sent to a machine shop and manufactured into a prototype. If the joints did not work, the original joint would need to be remeasured, and the entire process would need to be repeated until a suitable prototype was made.
This can be incredibly costly. To keep remeasuring, redesigning, remodeling and remachining new joints over and over takes a lot of resources and a lot of time, and when machining joints out of metal, the costs add up very quickly.
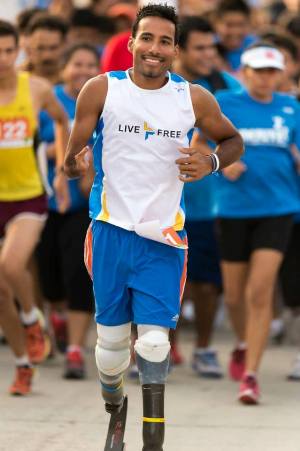
Rajesh Durbal using his new prosthetic joints
NeoMetrix Solution:
The NeoMetrix method of reverse engineering employs the use of 3D scanning technology for rapid and accurate data collection of complex geometry. The scanner of choice for this project was the Zeiss Comet L3D. Rajesh’s joints scanned into CometPLUS software. The captured data was directly output as a triangulated mesh or STL file.
This mesh was then imported into Geomagic’s Design X reverse engineering software, where it was used as the guideline for generating the new CAD model of the part. Cross-sectional sketches were developed based upon the scanned data and subsequently used to generate solid bodies through traditional modeling methods, such as extrudes, lofts & sweeps.
Design X also allows for comparison of the final model back to the original scanned data to ensure accuracy to the original part to ensure that the new joint attachments would fit snugly and securely
From there, the new quick connect joints were designed. However, instead of sending the new CAD model to the machine shop, we used our Stratasys Objet Connex 350 to 3D print the prototypes, saving Rajesh several hours and hundreds of dollars. Once we the prototype was perfected, the CAD model was sent to the machine shop and Rajesh had his new quick connect prosthetic joints.
NeoMetrix Advantage:
Reverse engineering through 3D scanning ultimately produces a more accurate part than traditional methods of data collection and manual modeling. This is particularly true for medical components that are comprised of complex contoured surfaces that are virtually impossible to measure by hand. A more accurate model then results in a more accurate connecting part which is more likely to fit properly when installed, reducing the need for costly rework and scheduling delays.
Rapid prototyping with 3D printing is vastly superior to machine shopping in that the time required to print a part is significantly faster, complex designs are easily handled, and the cost of materials is much cheaper. This ensures truly rapid prototyping, allowing a final product to be reached much faster than by traditional methods.
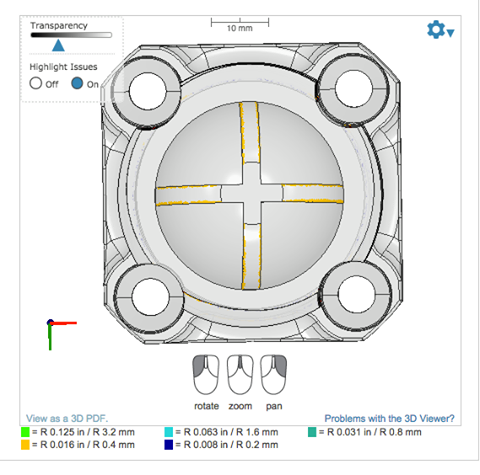
Joint Model
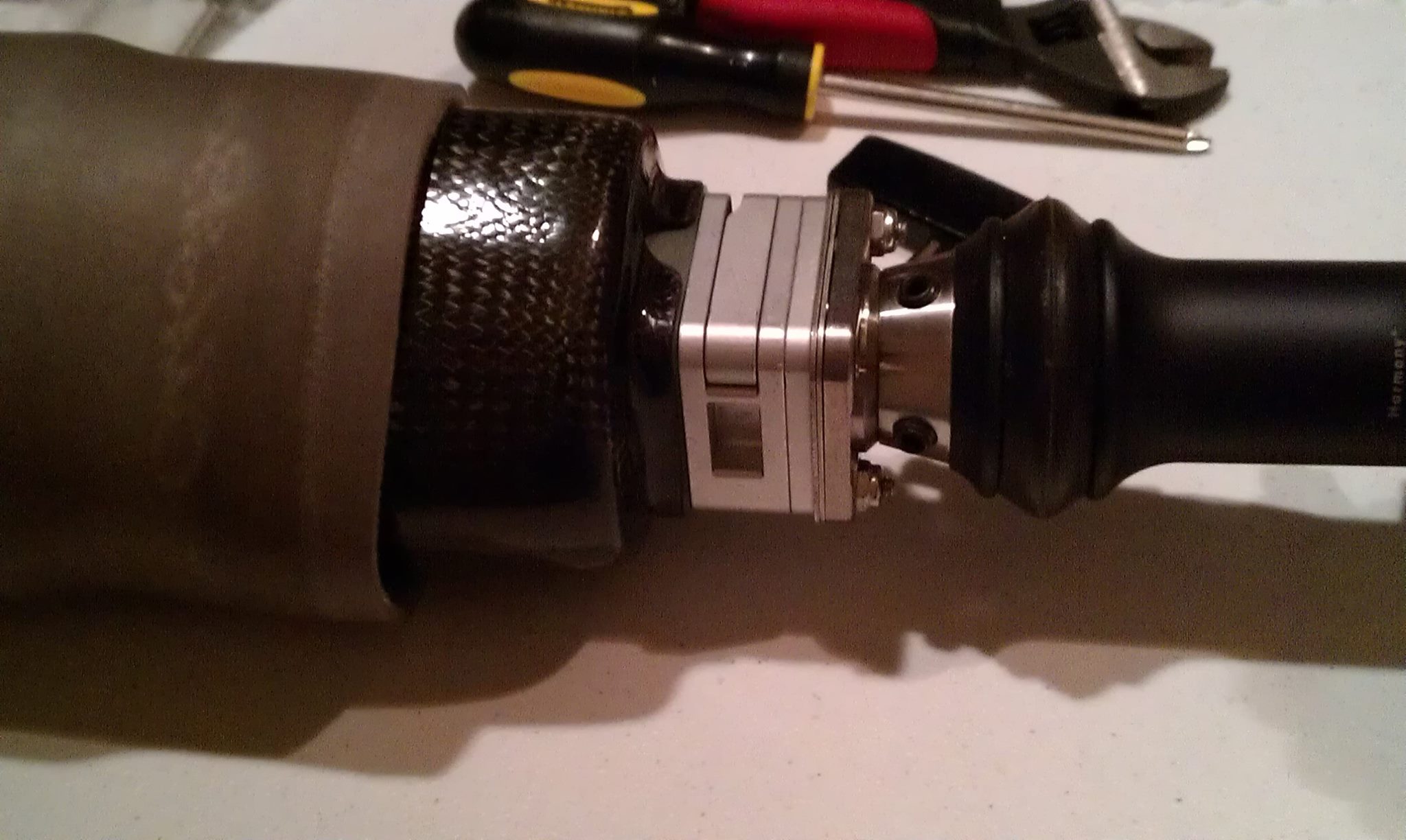
The Connected Joint