3D Scanning, Modeling & Printing of Alligator Skull Mount
The Problem:
A custom fixture was required to display an American Alligator skull. The fixture was to be designed in a manner so as the skull would be oriented, and the jaws held open to a width which made the mount most visually appealing. A product such as this would be relatively difficult to find, and most likely expensive.Traditional Method:
To create a custom mount such as this, one would traditionally have to put actual labor time into building the components once the final design was achieved. If the desired material were plastic, a molding method could be used. For a single item, machining a metal mold would be out of the question, leaving one with the tedious process of creating a silicone mold from a pattern made of clay or wood. Another option would be soldering or welding metal rods together for the mount, but this again would require labor, the appropriate tools, and the unique skill for manufacture. While other methods of creating a custom assembly may be explored, most require labor and manufacturing expertise to fabricate.NeoMetrix Solution:
The project was started by assembling and fixturing the alligator skull with the jaws propped opened to the desired orientation for the mount. Creaform’s HandySCAN 700 3D scanner was used to digitize the skull. Key geometry could not be captured during this setup due to line-of-sight issues with the scanner, therefore complete scans of both the top and bottom jaws were taken separately as well. All data sets were then brought into Geomagic’s Design X software for alignment. The assembled scan was used as the object to which both top and bottom jaws were aligned, resulting in a complete data set of the alligator skull in 3D space. ANSYS SpaceClaim was used to create the actual mount for the skull due to its unique direct modeling process. The complete mesh of the skull was imported and, following a few design iterations, the final version of the mounting bracket was achieved. A Stratasys uPrint SE Plus 3D printer brought the components to fruition within a few short hours. Once removed from the build tray, the parts were assembled and attached to a wooden plaque. The skull was then mounted to the custom fixture, and displayed for public viewing.NeoMetrix Advantage:
Creaform manufactures the fastest 3D scanners on the market today, and none are more portable, nor as easy to use as the HandySCAN 700. Creaform’s acquisition software, VX Elements, allows for hassle-free mesh generation (no point clouds here!) This can decrease the time to obtain a useable mesh from what could be hours to minutes. ANSYS SpaceClaim was developed specifically to expedite the iterative design phase of product development. There could be no better test of this concept than fabricating a custom mount for an individual animal’s bone structure. By directly editing the model itself, instead of programming a history tree as you would in software packages of old, SpaceClaim dramatically reduces the development phase of a project. SpaceClaim’s engineers were clever enough to include the ability to reverse engineer from scan data (something severely lacking in most common CAD offerings), allowing the user to interface certain load-bearing portions of the mount perfectly with the organic jaw geometry. Having access to a 3D printer for manufacturing custom components gives the engineer almost limitless geometry options, and allows for quick, last minute design checks. In this project, the lower jaw support was slightly more flexible than desired on the initial design. A revision was made by quickly thickening the model in SpaceClaim, and the new part was pulled off the printer and assembled on the same day.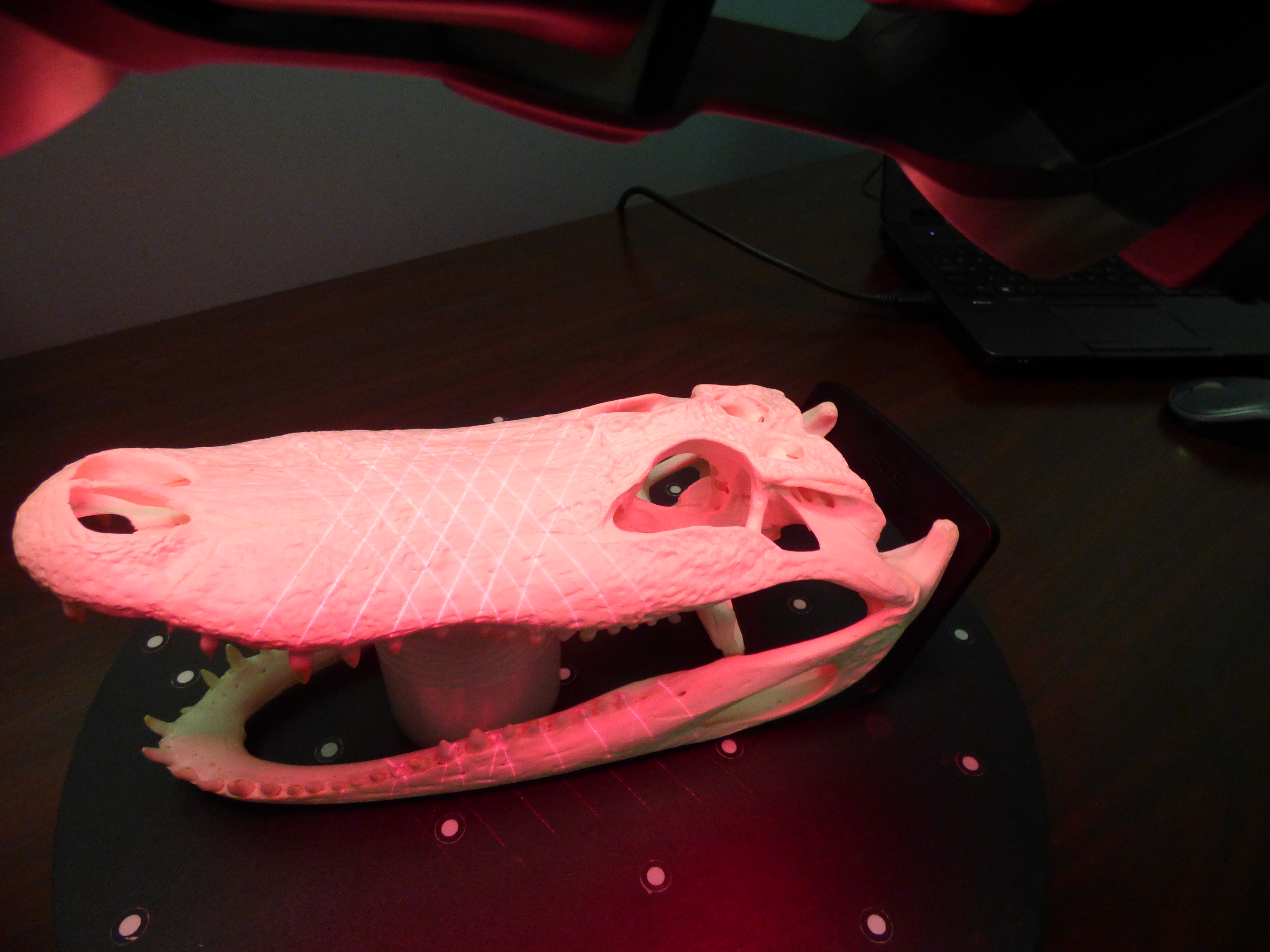
Alligator skull being scanned
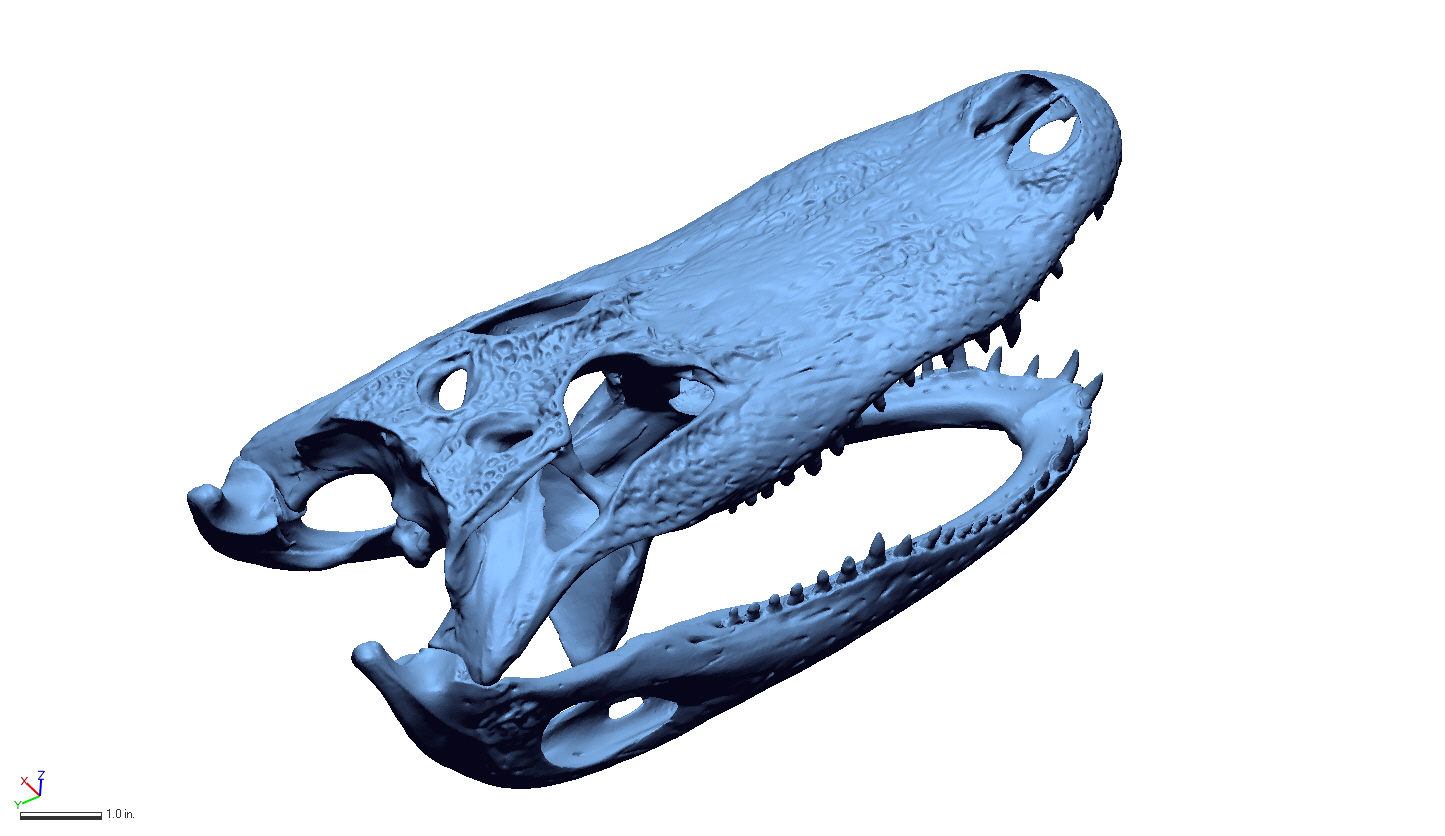
Alligator skull scanned data
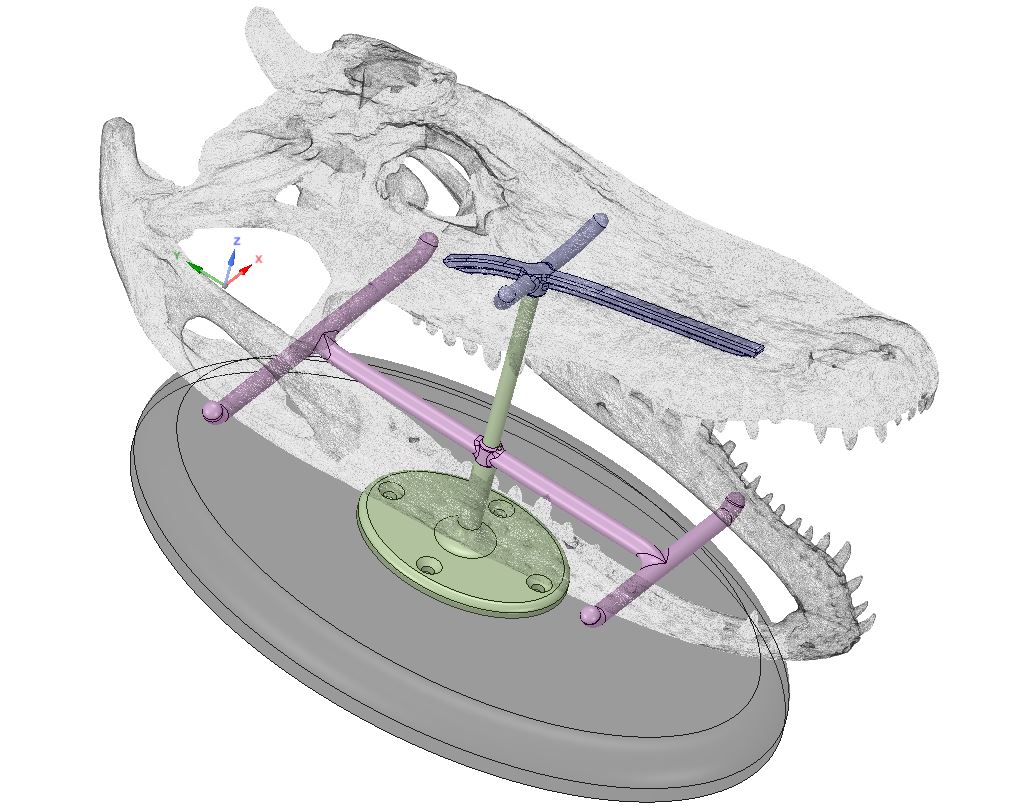
Alligator skull mount model
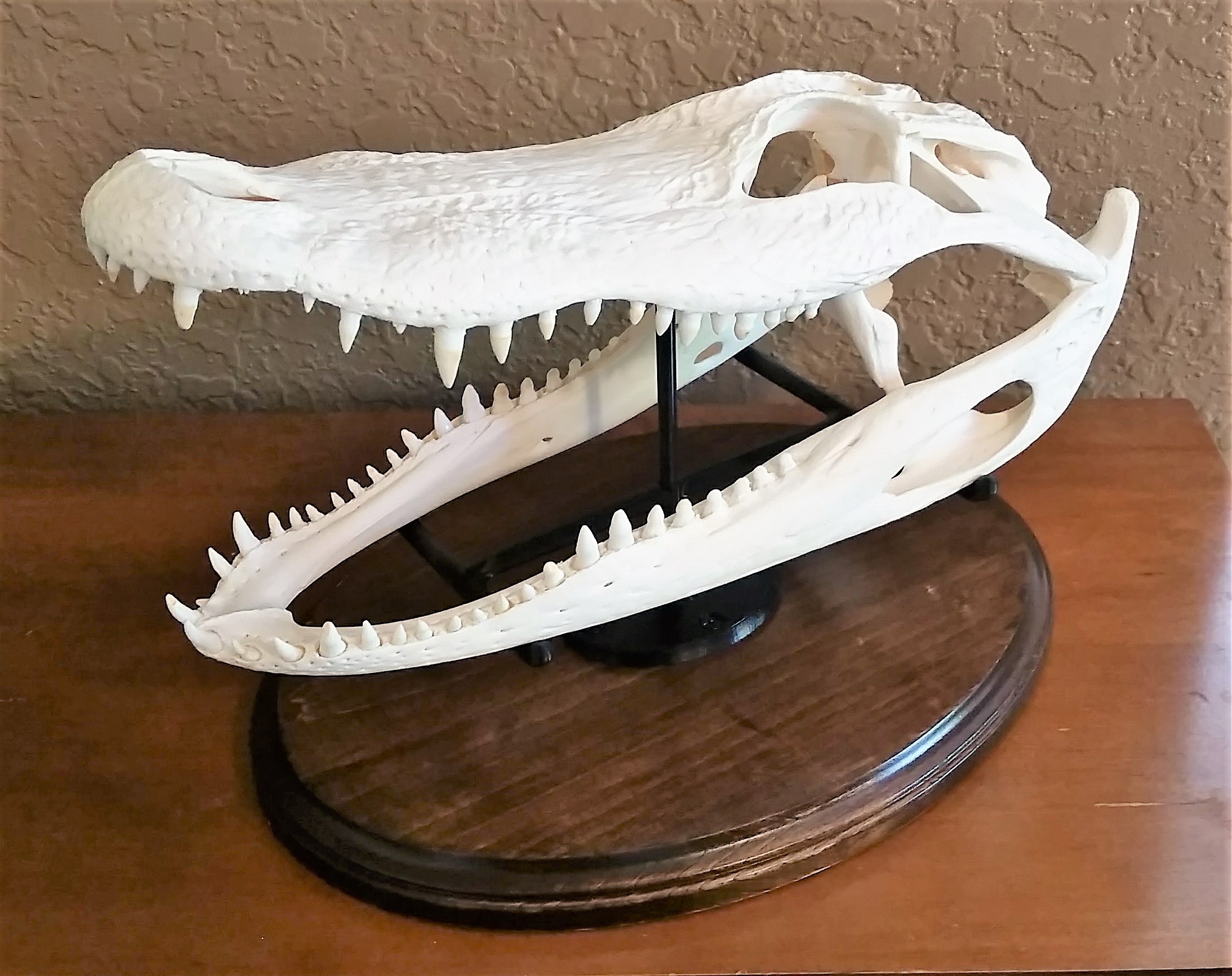
Assembled alligator skull mount