Developing Replacement Parts for Food and Beverage Industry
Powered By NeoMetrix TechnologiesLeading food manufacturers operate a dynamic facilities that includes a state-of-the-art in-house R&D lab and test kitchen. Advanced 3D printing supports various manufacturing scopes, including developing parts for machinery, private label production, co-packing, and customized branding services.
One of the challenges faced in food processing operations can involve essential parts like a hopper saddle component—a critical part that undergoes significant wear and requires frequent replacement.
THE PROBLEM
Due to ongoing supply chain disruptions and tariff-related delays, obtaining timely replacements became increasingly difficult. With this part being essential for continuous production but not needed in high volumes, sourcing became a pain point. Businesses in the food and beverage manufacturing fields need a flexible, on-demand solution that could adapt to their changing production needs while maintaining the reliability that their equipment demands.
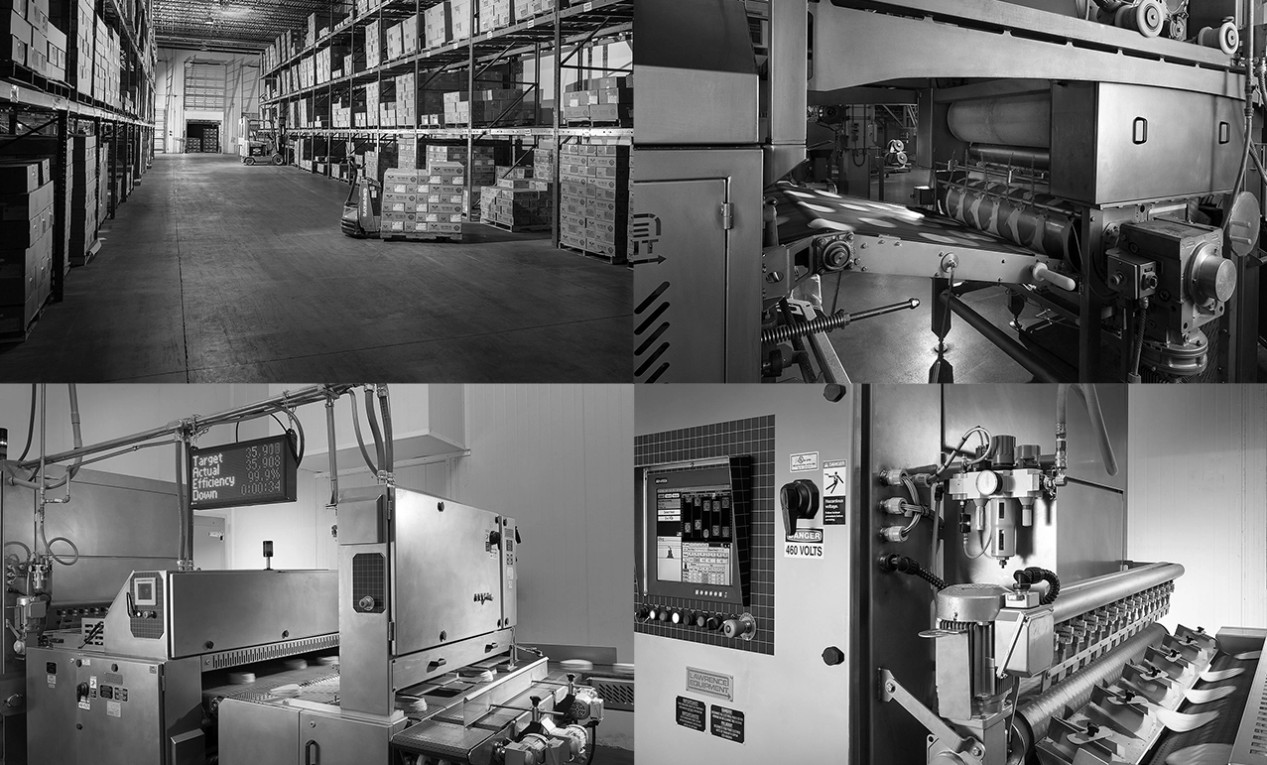
According to a recent report by SmarTech Analysis, the food and beverage industry is projected to increase its use of industrial 3D printing by over 400% in the next five years,
TRADITIONAL METHOD
Traditionally, companies relied on OEM parts that were either imported or produced by third-party machine shops. These parts came with long lead times, high costs, and limited opportunities for design modifications. The dependence on external vendors made it difficult to maintain uptime on machinery, especially when parts failed unexpectedly. The lack of customization also meant these components were not optimized for longevity or performance in their specific operating conditions.
NEOMETRIX SOLUTION
Businesses are now seeking to partner with NeoMetrix Technologies for services and equipment to so that manufacturers can produce in house. The part was designed with reinforcement layers in key areas subject to stress and impact, improving both durability and functional performance.
The replacement hopper saddle was printed using the INTAMSYS FUNMAT PRO 410, a high-performance industrial 3D printer with a build volume of 12 x 12 x 16 inches (305 x 305 x 406 mm)—an ideal size to accommodate larger, production-ready components like the hopper saddle. This allowed the entire part to be printed in a single build, eliminating the need for assembly or sectioning that could compromise strength.
Using Polycarbonate as the choice of material is suitable for parts in the food manufacturing industry due to key advantages:
1. High Impact Resistance
Polycarbonate is extremely tough—up to 250 times stronger than glass—making it ideal for functional parts that must endure mechanical stress or abuse.
2. High Heat Resistance
PC can withstand continuous operating temperatures up to 110–130°C, making it suitable for high-temperature applications like enclosures and fixtures.
3. Dimensional Stability
PC offers excellent stiffness and minimal warping, ensuring parts maintain dimensional accuracy under load or temperature changes.
4. Optical Clarity (when needed)
Certain PC blends can be printed with semi-transparency or optical clarity, useful in lighting, prototyping, or display applications.
5. Chemical Resistance
Resistant to many oils, greases, and solvents—making it a strong choice for industrial environments.
6. Flame Retardant Grades Available
UL 94 V-0 rated PC variants are available for applications requiring flame resistance, such as electrical or transportation components.
7. Machinability & Post-Processing
PC parts can be drilled, tapped, and machined after printing without cracking, giving engineers more flexibility in prototyping or production.
This service-based benchmark validated the use of additive manufacturing for an industrial food & beverage production environment. After evaluating the performance of the printed part and reviewing the range of 3D printing technologies offered by NeoMetrix, the businesses in this field are exploring long-term in-house additive manufacturing strategies.

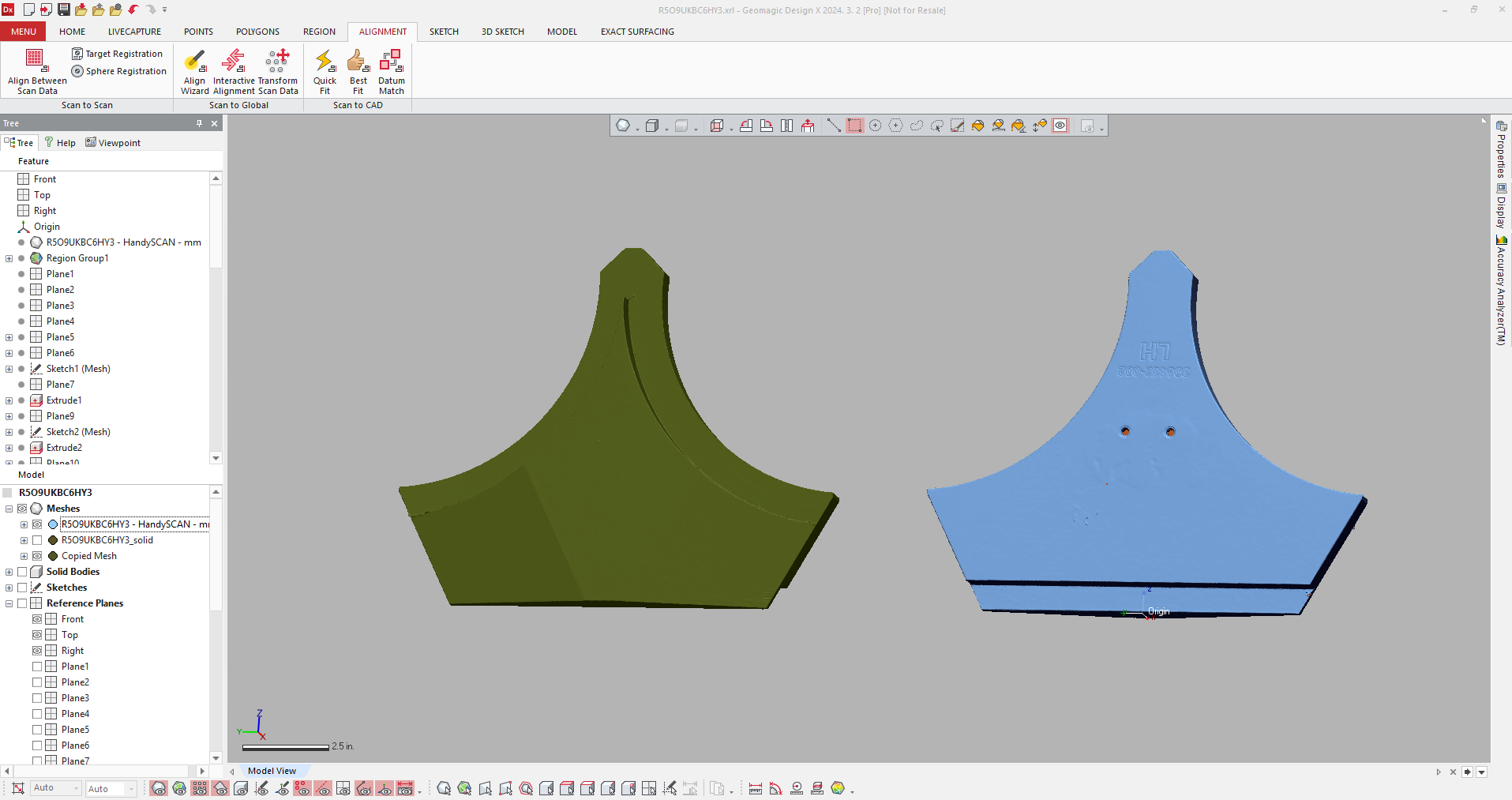
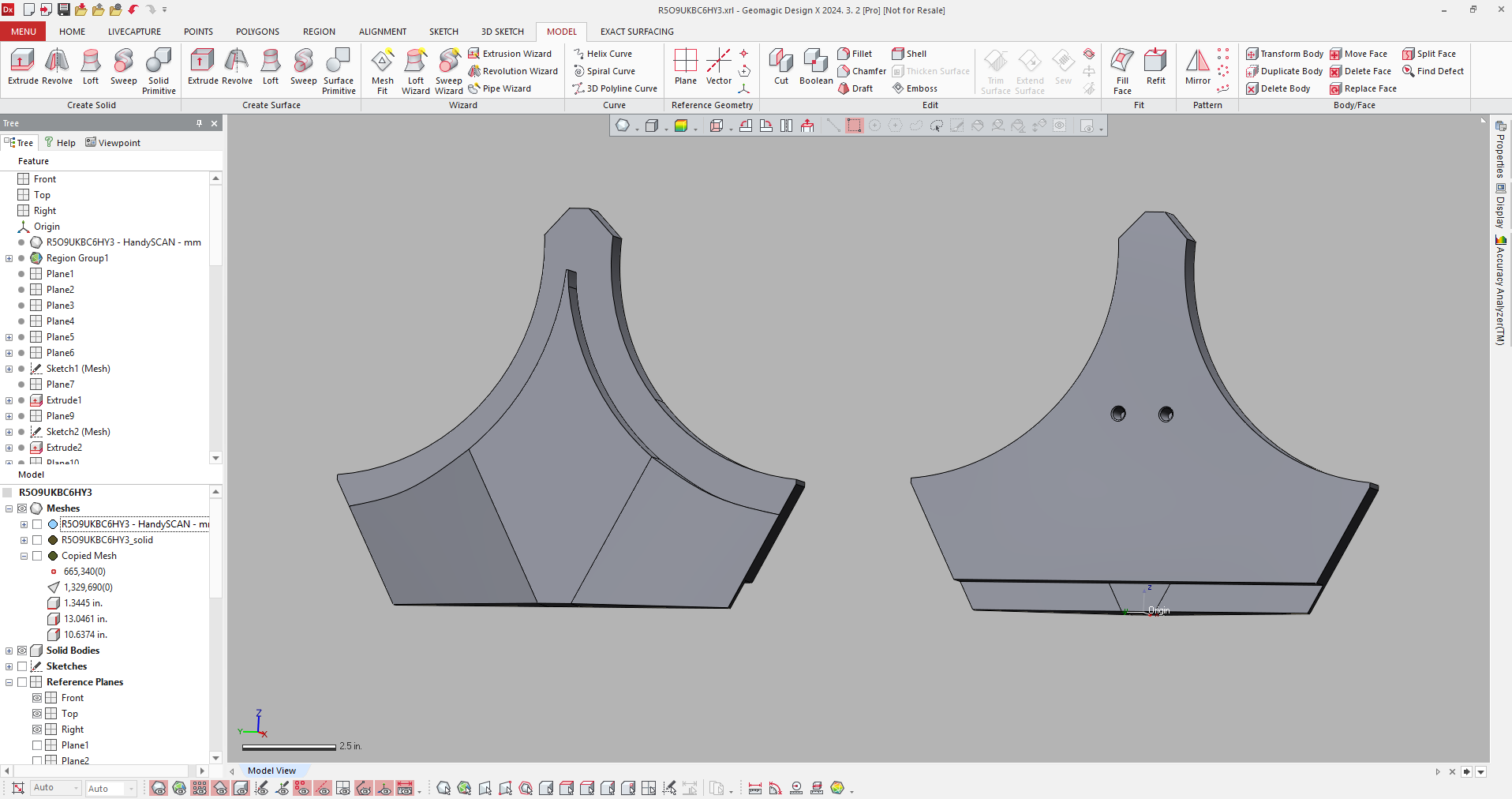
INTAMSUITE NEO – Slicing & 3D Printing Software
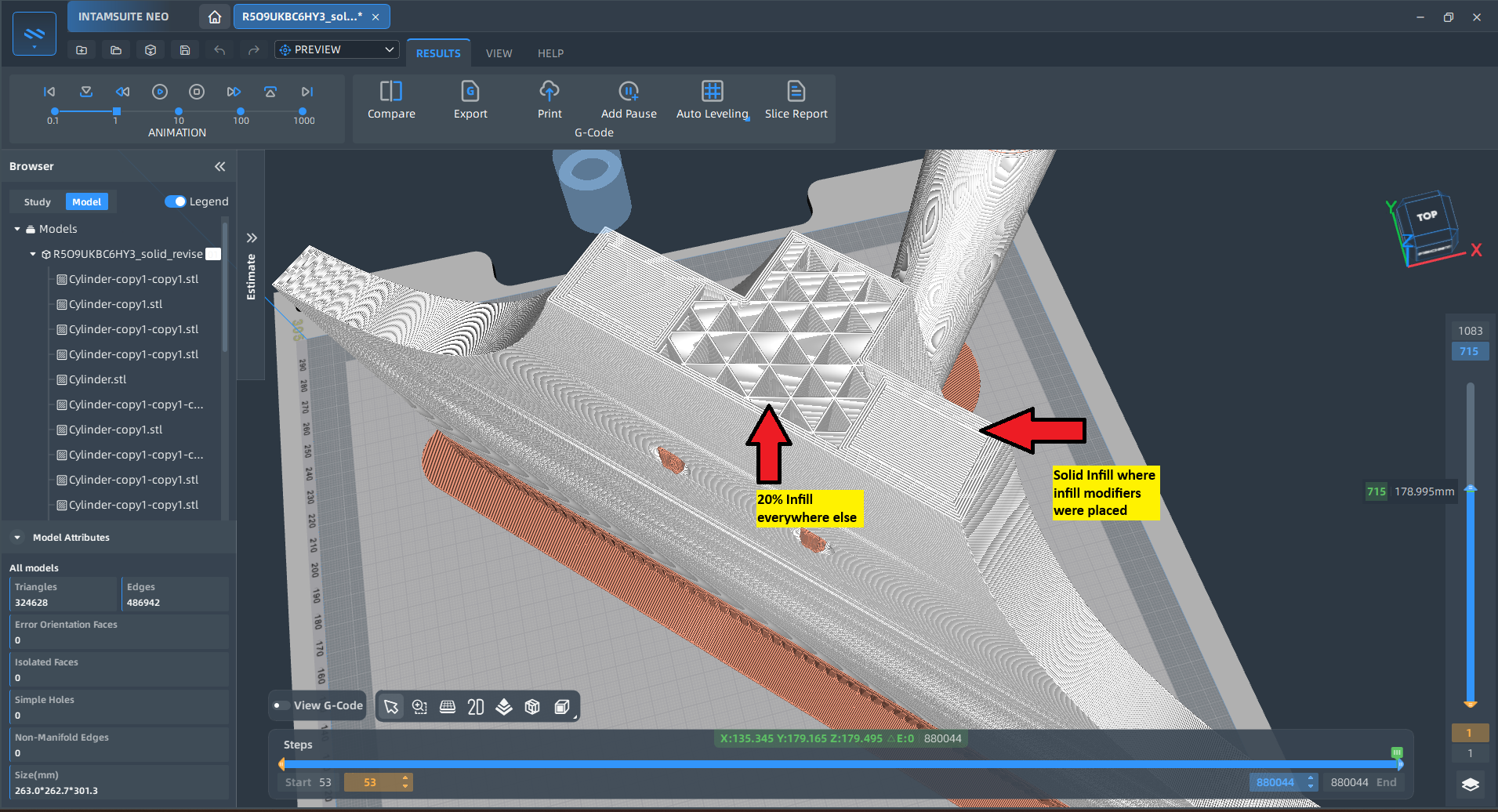
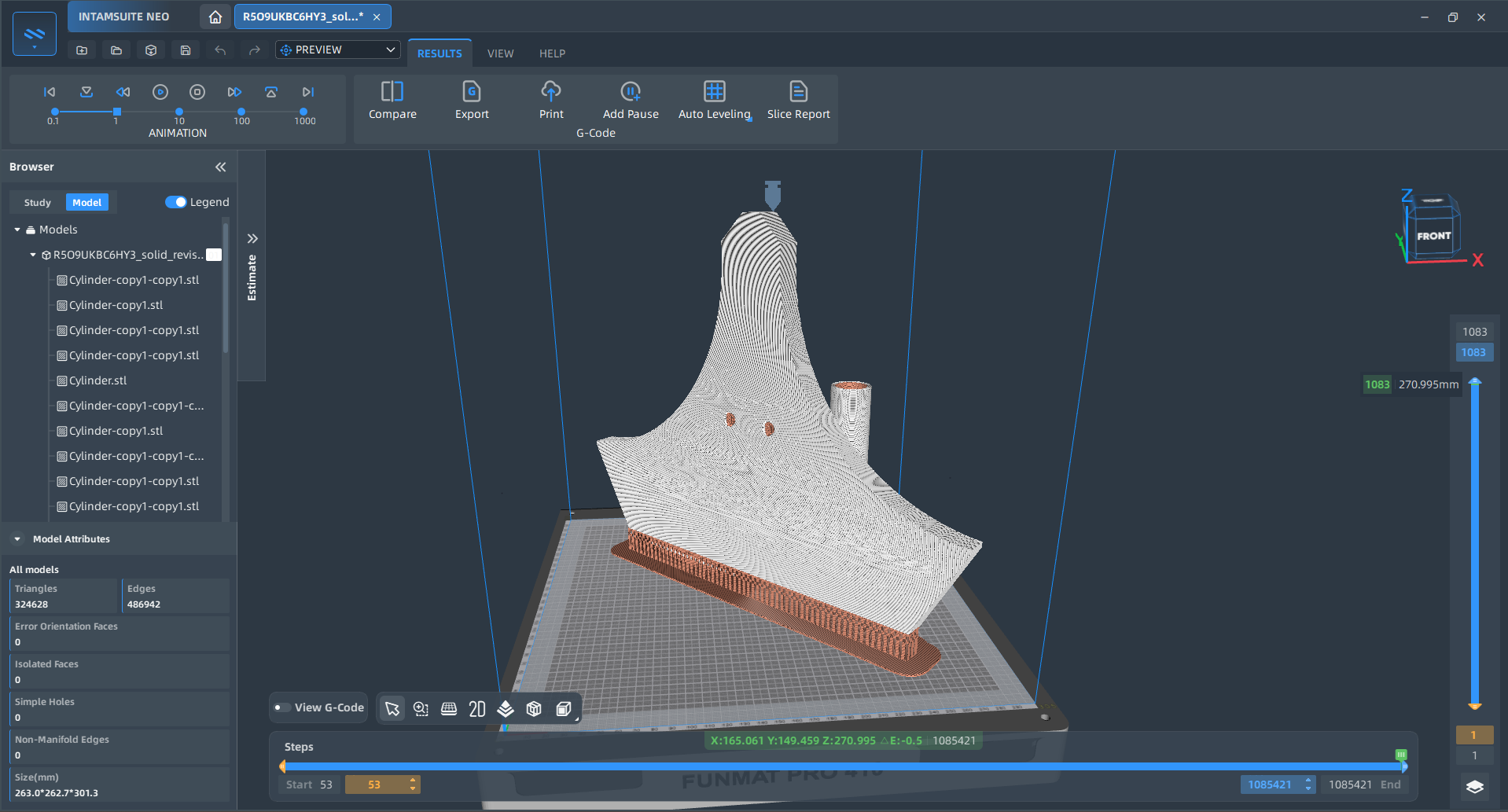
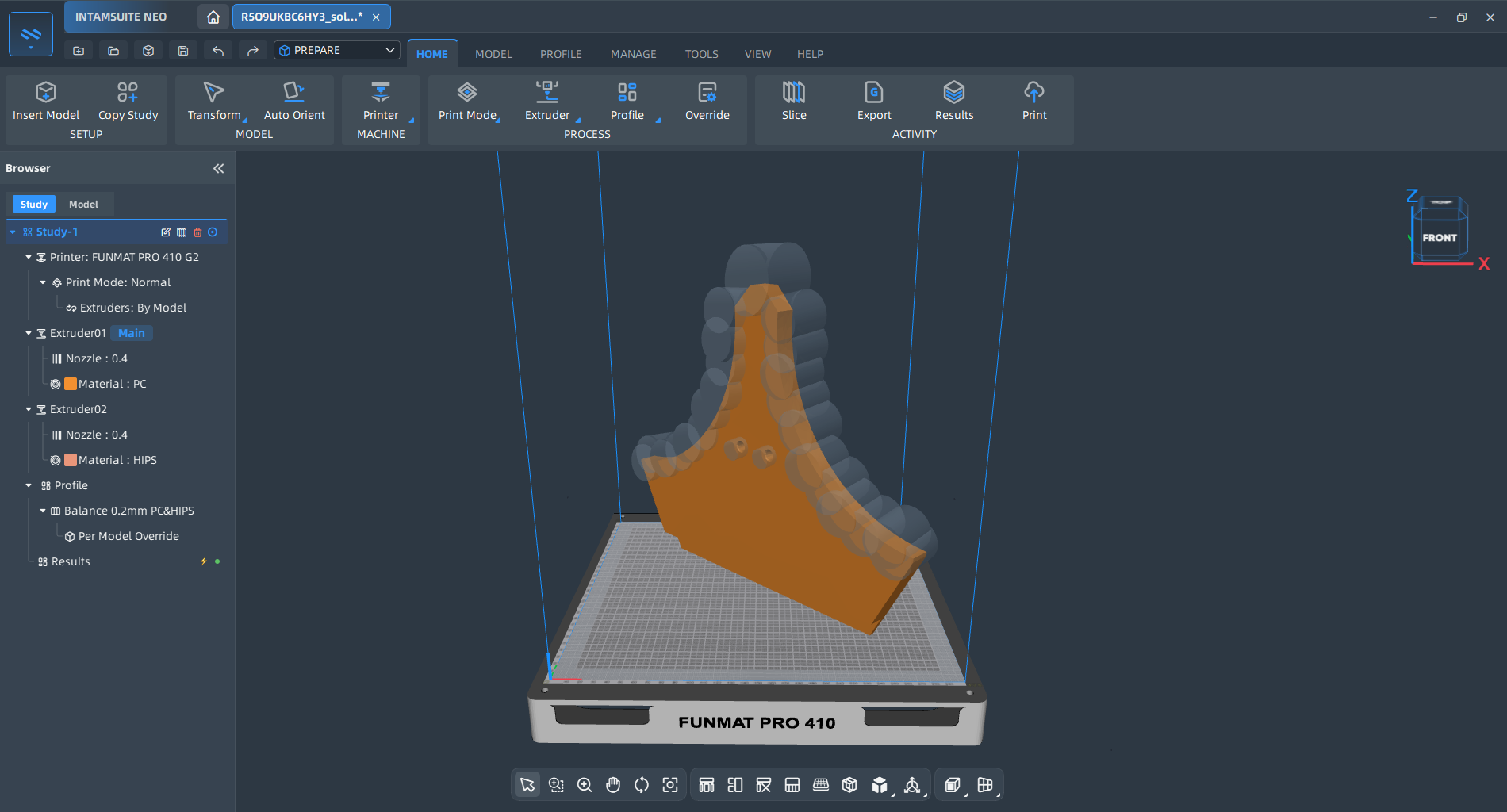
NEOMETRIX ADVANTAGE:
NeoMetrix provided a scalable solution that addressed both immediate needs and future growth:
-
Rapid Production Turnaround – NeoMetrix’s 3D printing services enables you to receive a functional prototype in days, not weeks.
-
Tailored Design Enhancements – Reinforced design elements optimized for durability and performance.
-
Equipment Expertise – By running a successful benchmark on any of our advanced 3D Printers, you can see the benefits of NeoMetrix’s extensive equipment lineup.
-
Path to In-House Production – Following the benchmark success, your business can began pursuing the right equipment
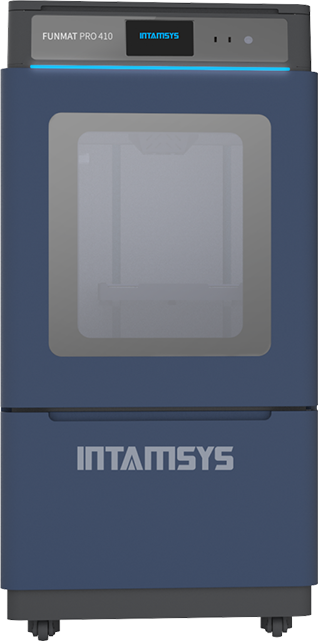
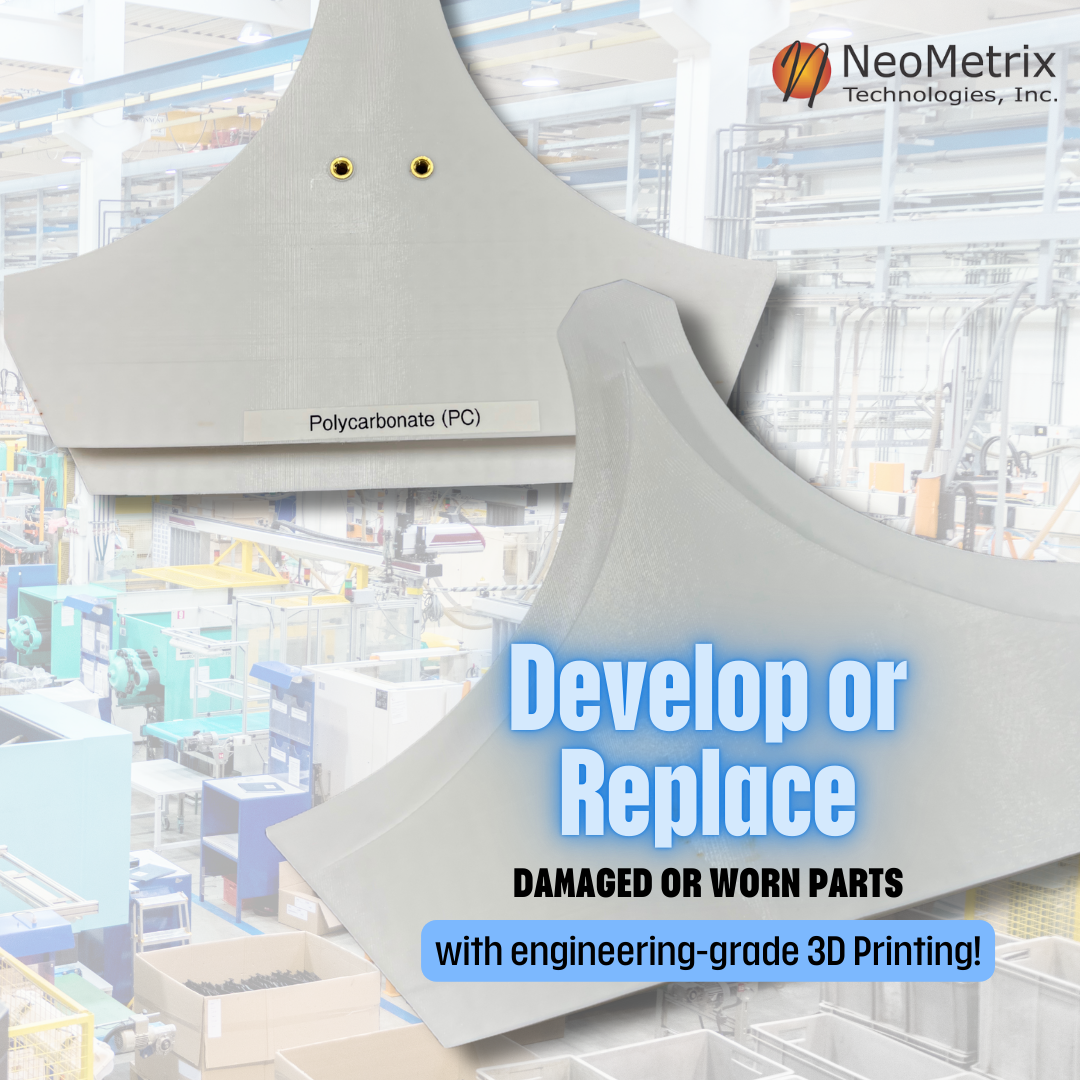
NeoMetrix has proven experience helping businesses in the food and beverage industry transition from traditional sourcing challenges to an agile, additive manufacturing solution. The benchmark part printed on the FUNMAT PRO 410 demonstrated the immediate value of 3D printing.
By 3D printing a benchmark part, our clients have a better understanding of how the part will perform before making a business decision to move forward purchasing equipment or partnering with us to outsource services.
3D Print a Benchmark Part for Your Business
See what materials and 3D printing technologies work best for your application.