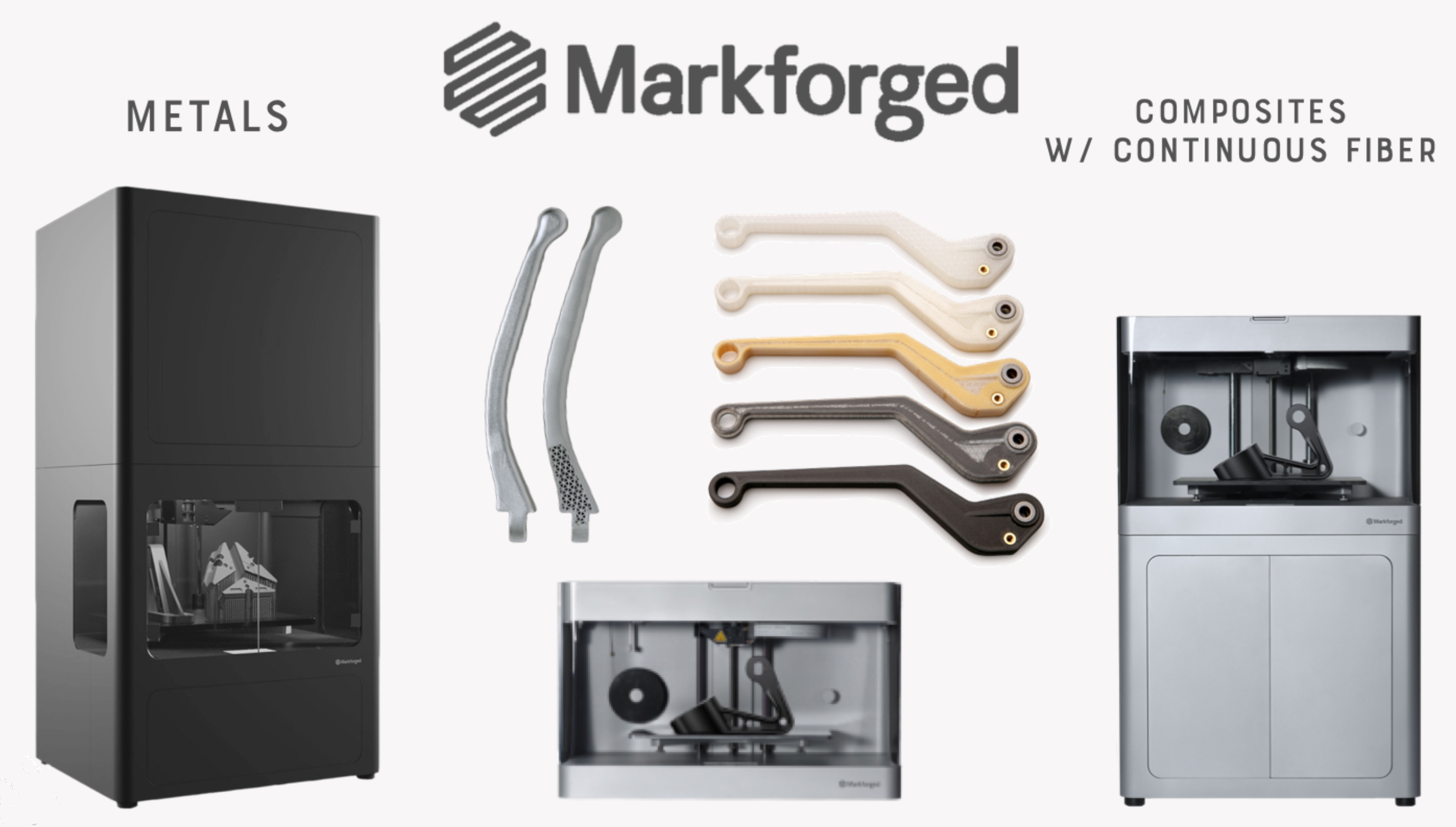
3D Printer Manufacturer Markforged was recently granted a patent for its multilayer fiber reinforcement design for 3D printing. This process takes fiber swaths with anisotropic characteristics and uses them to reinforce a matrix material, such as a thermoplastic, with the strength of this fiber. A comparable relationship would be rebar in concrete. Markforged’s printer lineup is based on the Fused Deposition Modeling (FDM) style of 3D printing; however, the patent goes beyond FDM, covering cured resins (SLA), laser sintering, and many other systems for “solidifying” a material. This patent prevents another company from using the same process and simply switching out the matrix material printing system.
Why is this technology important to industrial manufacturers? Prior to fiber reinforcement, access to strong, functional 3D printed materials was limited. The strongest of 3D printed plastics required serious capital investment and were often still not strong enough to replace previously metal parts. Printers were mainly used for prototyping applications or low volume end-use parts. Metal 3D printing was difficult to justify unless the company had a very complex, low-volume part with high-profit margins. Investments in these machines often were in the million-dollar range.
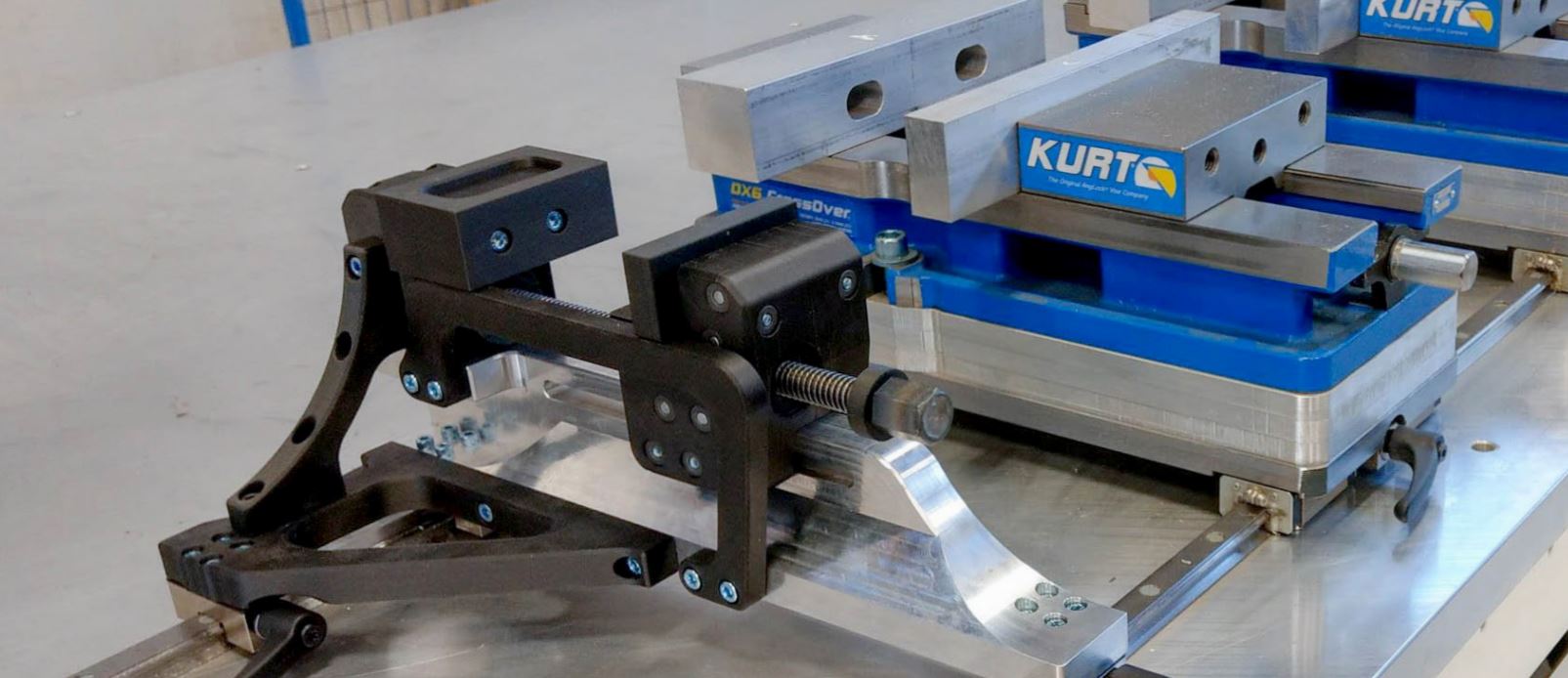
With the introduction of printed composites, companies now have access to metal-strength parts, without the million-dollar investment that was previously necessary. Materials like carbon fiber are stronger and lighter than 6061 Aluminum (a common material used for tooling). These fibers can be impregnated within a plastic matrix, giving access to the strength of the composites while also holding onto the advantages that accompany plastic 3D printing. Markforged is unlocking the capability to produce complex tooling, which rivals the performance of previously machined metal parts. With this new capability, Markforged has bridged the gap between metal and plastic 3D printing.
A machine shop in Saskatoon, Canada that invested in Markforged’s composite technology received a job that required new soft jaws and vises to be fabricated. These tools would hold a component while the mill cuts the part. To build this tool in-house, it would take $6,000 and they already had a 3-week backlog for tools. Utilizing continuous carbon fiber reinforced parts, the company 3D printed these tools in under a week for only $1,500. Not only did this free up their machinist’s time, but it also greatly improved their margin for this project.
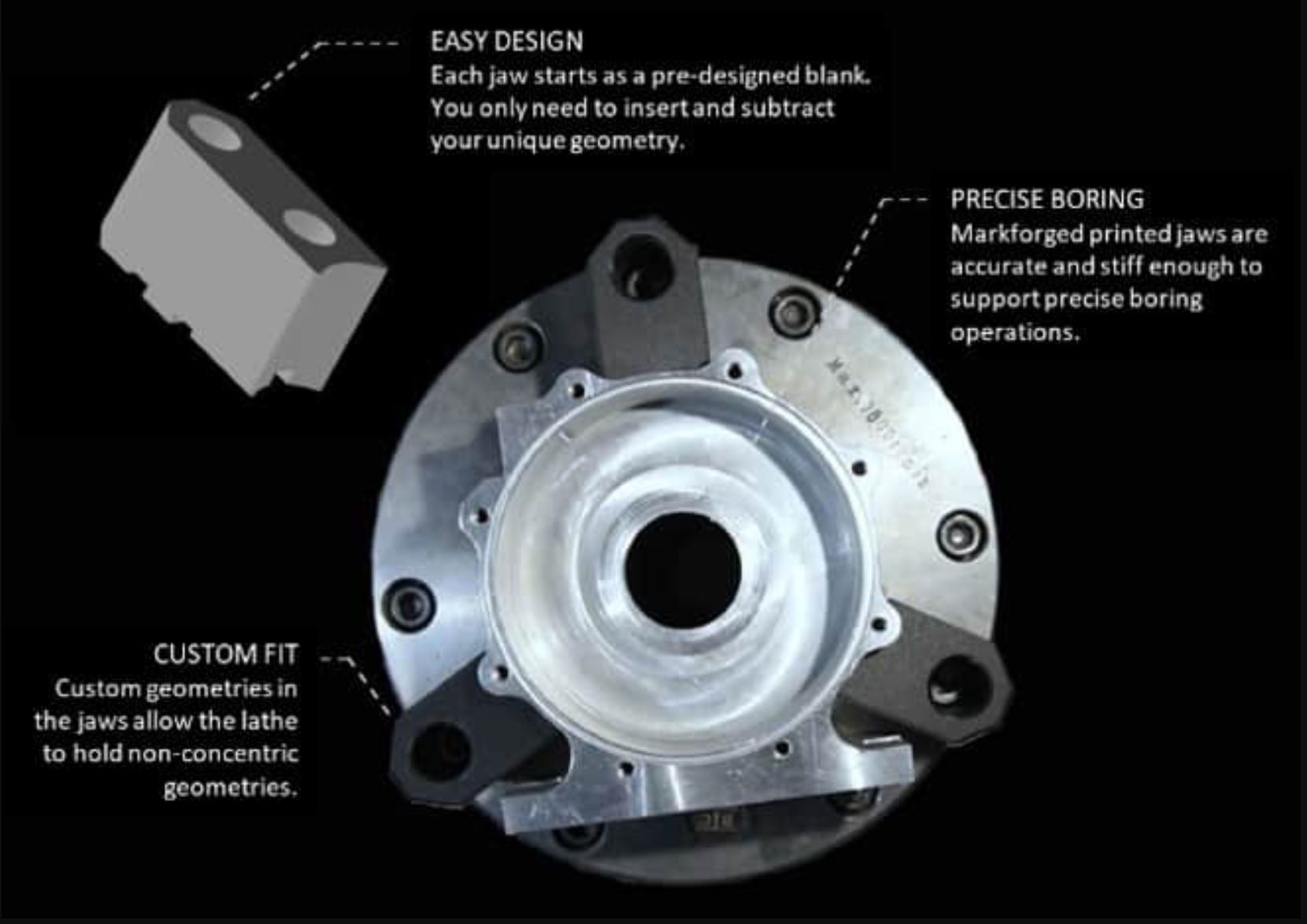
Tooling cost and lead times are often the factors that dictate whether or not a manufacturer will take a job. Markforged’s composite technology significantly lowers both of these factors for many tooling applications, allowing companies to take on more business and reducing production costs. Companies that adopt this technology have a significant advantage, as they can outprice and deliver quicker than the competition. They can also go through multiple tool iterations and end up with a better end product. technology.