Challenges: From the CAD files to the development of individual components, how can the performance of a sport motorcycle be translated from theory to practice?
Designing sport motorcycles for racing requires attention to detail. Designers and engineers must ensure that the physical parts comply with the CAD. To do so, they must scan the components, put them in STL data, and compare that with the CAD file. The scan-to-CAD comparison must be done seamlessly. Therefore, the scan quality must be impeccable in order to bring out the finest details, and the discrepancies must be quickly highlighted—with a colormap process—in order to be corrected.
Knowing that the driver’s body impacts the performance of a sport motorcycle, how can the ergonomics of the components and the complete vehicle be tailored to each racer’s specific physical shape?
The drivers must be in an optimal position to ride a sport motorcycle. The seat, steering bar, and pedals must be perfectly suited to their physiognomy, as must the position of the dashboard (and the navigation screens for offroad vehicles), which must be adapted to their eyes for optimal visual acuity. Therefore, to maximize the ergonomics, designers and engineers must use measurement instruments that can scan the whole bike, including the driver.

Knowing that aerodynamic parts require the design of complicated geometries, how can the product development team measure complex shapes and adapt their design while minimizing the number of iterations?
Aerodynamics is often the key to winning milliseconds on the racetrack. To get optimal parts, designers and engineers conceive complex shapes, test them in a wind tunnel or the racetrack, then make adjustments, test them again, and so on. This process may require several iterations. Minimizing the number of iterations is essential to achieving the required aerodynamics as quickly as possible. To do so, measuring a lot of data without programming or preparation on the complete surface (not just discrete points) enables designers and engineers to save time during the design process while obtaining parts of better quality.
Knowing that a sport motorcycle is made of a multitude of components that must all fit together, how can the product development team quickly and accurately check all of the parts regardless of their size, shape, and surface finish?
Inspecting all parts, regardless of their size, shape, and surface finish quickly and accurately and without surface preparation, is only possible with 3D scanning technologies. Available to all designers and engineers in the design factory, regardless of their knowledge or experience with 3D scanning, it can be brought to wherever the parts are (in the workshop, QC area, or at the
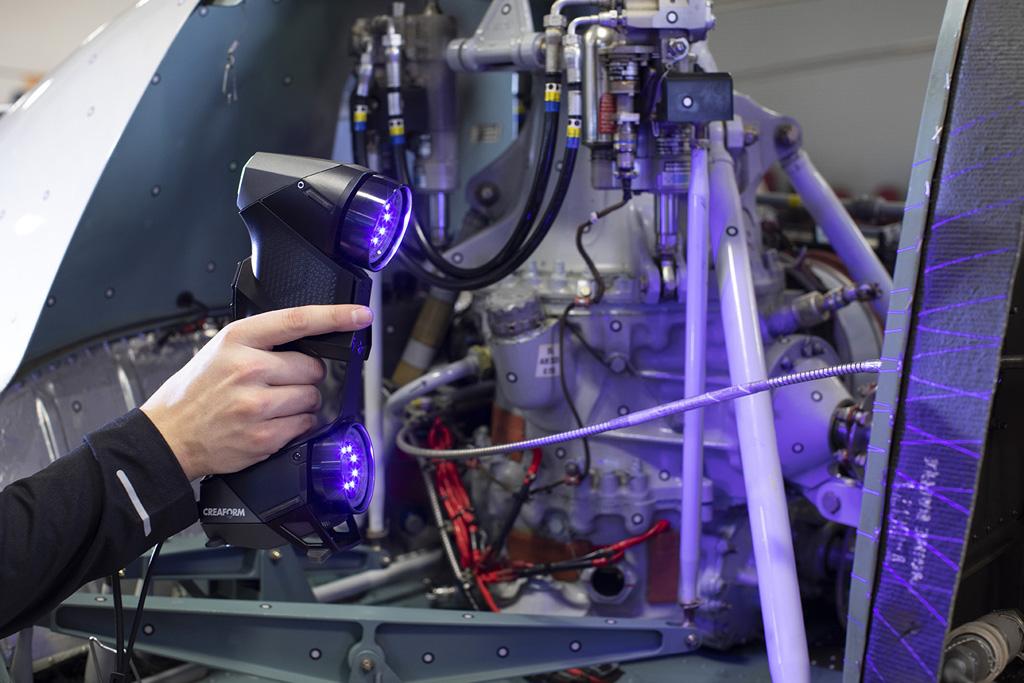
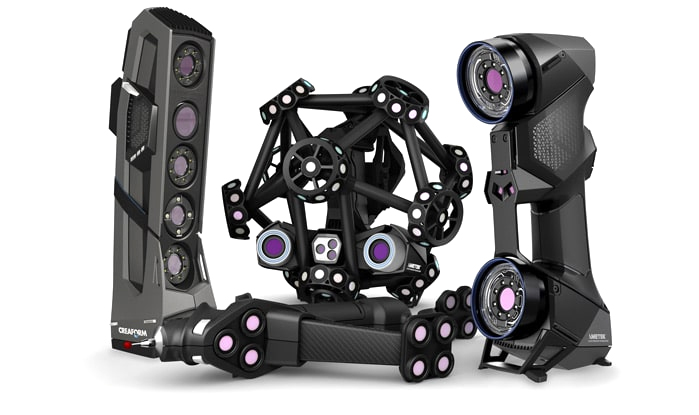
Solutions: High-Resolution, Versatile, Simple, and Fast 3D Scanning Technologies
The high level of detail is provided by high-resolution cameras for geometry and texture. For design and product development teams, the scan quality is essential in order to see the discrepancies between the STL data and the CAD file.
Versatility is made possible with advanced white light and optical technologies and limitless scanning volumes. 3D scanners can measure any part, regardless of size, shape, material, surface finish, and complexity.
Simplicity is illustrated with plug-and-play tools and user-friendly interfaces, where expertise and experience in 3D scanning are not required.
Speed is defined with the instant mesh feature, where the generated mesh is already lightened and processed, ready to be seamlessly integrated into reverse engineering, CAD, or 3D printing software.
Metrology-grade 3D scanners, such as the Go!SCAN 3D, as well as the software platforms VXModel and Polyworks, are good examples of these high-resolution, versatile, simple, and fast scanning solutions.
Benefits: With high resolution, versatility, simplicity, and speed, the design of sport motorcycles is optimized and tailored to the driver’s body for enhanced performance.
In addition to success on the world stage, the pleasure that riders experience while driving exceptional vehicles is the ultimate proof of the manufacturer’s realization. 3D scanning technologies contribute to the following benefits, all of which are essential to being victorious in the world’s toughest races:
- Better Performance
Building sport motorcycles for racing requires the design and development of complex geometrical parts with various shapes and surface finishes. With 3D scanners, engineers and designers now have the capacity to make adjustments to components that were simply impossible to measure before, adding performance and robustness to vehicles. - Design Tailored to the Driver’s Body
Thanks to their high resolution and portability, 3D scanners enable designers and engineers to scan the whole bike, including the driver. This way, they can adapt the design to the driver’s body, maximizing the ergonomics of the motorcycle and optimizing the driver’s position. - Optimized Design Process
Since 3D scanners can capture a lot of data on the complete surface (not just discrete points) without programming or preparation, designers and engineers save time during the design process by minimizing the number of iterations required to develop aerodynamics parts.
KTM AG designs, develops, and builds high-performance street and offroad sport motorcycles. Over the years, KTM has built a reputation as a fierce competitor on racetracks around the world. With an established presence in the offroad segments, KTM has progressed to become one of the world’s most innovative manufacturers of street motorcycles and now aims to be the world’s biggest manufacturer of sport motorcycles.
Because they are on a non-stop mission to develop, evolve, and improve their product range, KTM Motorsport’s design and product development team needs fast, versatile, and portable 3D scanners that can be used to scan everything everywhere. “For us, speed is also very important,” says Christian Schwarz, Quality Controller Motorsports at KTM AG. “We need to put the parts in STL data and compare it easily with the CAD files.“ It’s one of the reasons they have chosen the Go!SCAN 3D.
In addition, the selection of Creaform’s 3D scanning solution improved communication between the design, manufacturing, and quality control teams. Now, data can be exchanged easily. Closer networking occurs around 3D scanning, and it brings dynamics to the group. All teams can use scanned data and work together from the same information.
Now, KTM Motorsport’s design and product development team can make improvements by scanning almost every part and bringing the Go!SCAN 3D wherever they go. The benefits they get compared to before purchasing the Go!SCAN 3D are significant. “We can make adjustments to components where we had not previously thought of doing so before,” adds Sebastian Witt, head of Quality Management Motorsport at KTM AG, who was thrilled to show us their newest sport motorcycles.
Original Article: https://www.creaform3d.com/en/applications/design-and-development-high-performance-street-and-offroad-sport-motorcycles?utm_campaign=dm-20&utm_medium=social&utm_source=facebook