Do you make a highly specific product that you adapt to each customer’s needs and requirements? This usually involves long iteration cycles that cost both time and money. Learn how the ZOELLER group now takes just days rather than weeks to develop and optimize its custom-made components.
How did 3D printing evolve at ZOELLER?
ZOELLER’s 3D printing operations have been dramatically improved by adding a BigRep ONE to their arsenal. The time spent creating parts for production and also allowing them more control over the process has led this company in particular, but others too who are looking at cutting down costs or becoming less reliant on outside providers-to see huge increases across all departments with no decrease whatsoever when using these machines! The ONE was soon upgraded to tandem mode, so that parts could be printed at the same time in order to further speed up production.
ZOELLER has also been using the BigRep PRO for two years now, and it’s allowed them to print more than twice as fast with improved precision. This machine is fully enclosed in order maintain consistent temperatures throughout its process; additionally they can handle an even wider range materials which means there are almost no limits on what kind of things you’ll be able produce when on the job.
Nowadays, ZOELLER prints not just prototypes, but also production equipment. Quantities range from 2 to 2,000 units, depending on the component. A 1 cubic meter build volume allows large parts to be printed in one piece, so there is no need for bonding. Alternatively, the large printing surface can be used to produce larger numbers of multiple small objects sequentially. ZOELLER now plans to print end-use parts in small runs in the near future. Some parts are reworked, e.g. primed and painted, and then subjected to weathering tests to examine their suitability for use in all weathers.
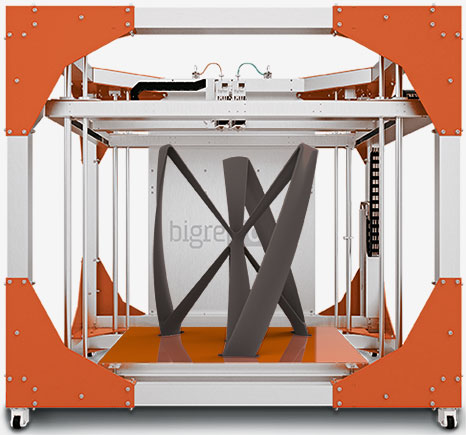
What experiences has ZOELLER had with 3D printing and its BigRep printers?
It was not difficult for employees to familiarize themselves with 3D printing. They were quickly able to learn what they needed to know, and the printers were integrated smoothly into existing production processes. This is partly due to the construction and design of the BigRep PRO and the BigRep ONE, and partly to the support provided by BigRep customer service. Marco Neuchel: “The BigRep PRO has been running for more than 300 hours now, and we have not encountered any problems so far. It is a really well-designed machine! And whenever we have a question about the printers or the printing process, we can get help on the phone or via email. We are completely satisfied with BigRep!”
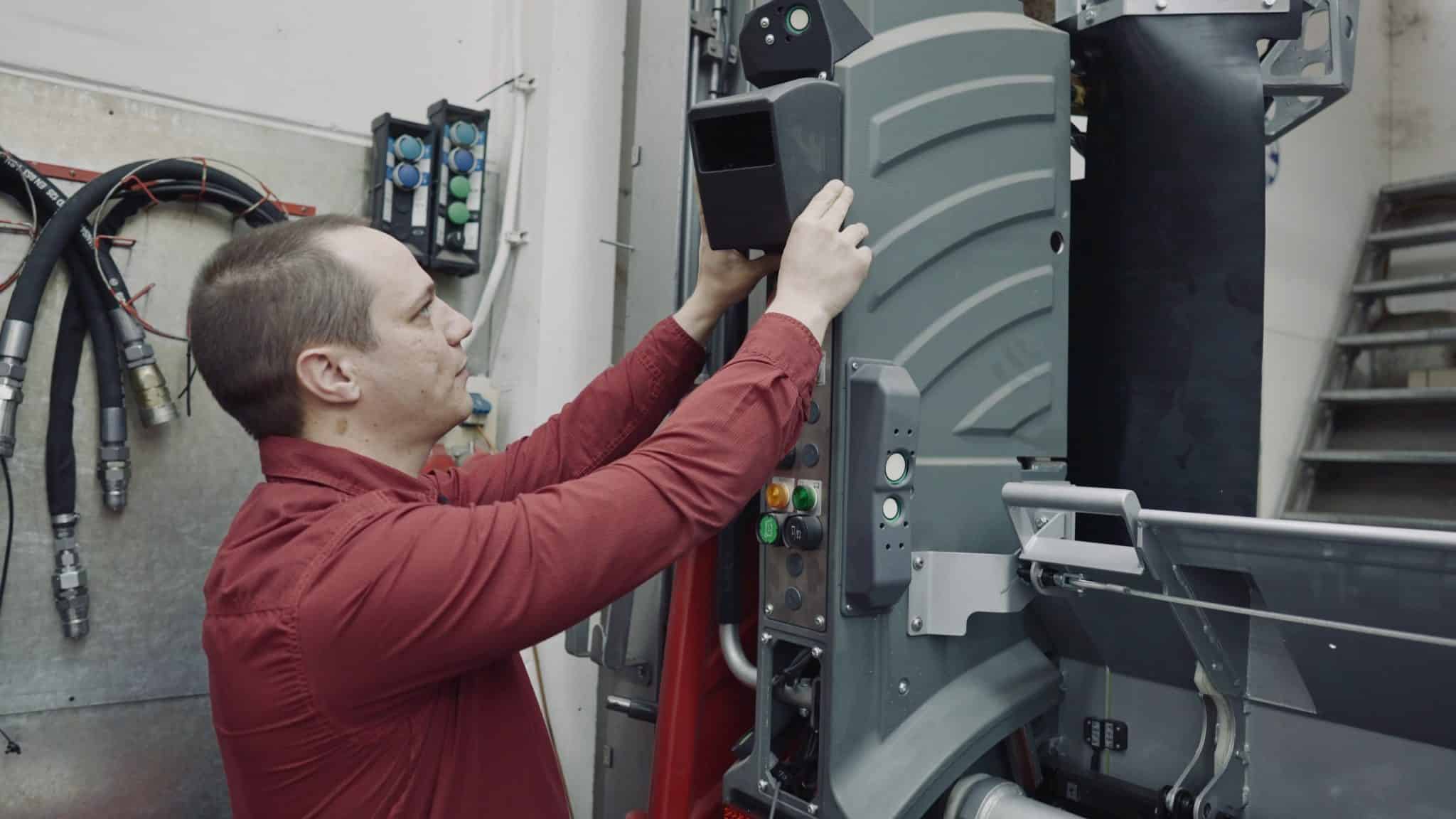
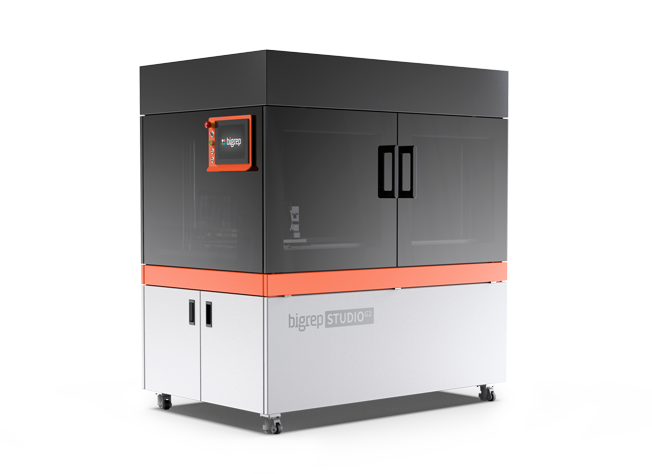
3D printing has taken root quickly at ZOELLER, and is now an integral part of the production chain. So it’s hardly surprising that Dr. Ferhadbegović is very pleased:
“3D printing has become an integral part of our development process. 3D printing is definitely the future for us!”
At NeoMetrix, everyday we push the limits and ideas of cutting edge 3D printing technology and we’ve been working with some of the biggest names in commercial vehicle manufacturing for years now. We can help you reduce your time to market by up to 80% while cutting costs and producing high quality product.
Original Article: https://bigrep.com/posts/fast-targeted-product-development-in-commercial-vehicle-manufacturing-through-3d-printing/
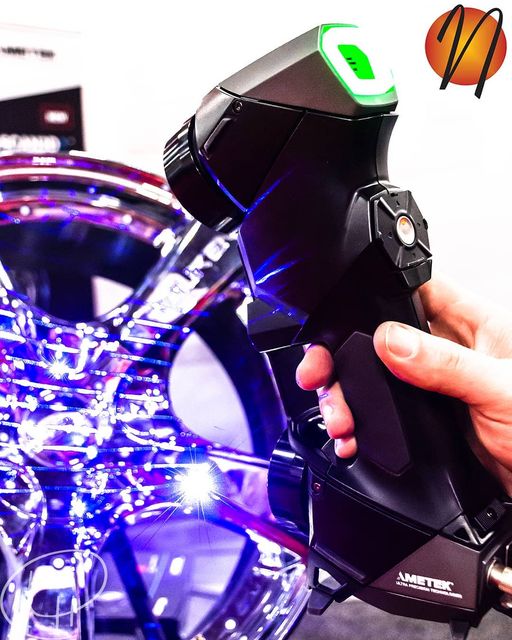
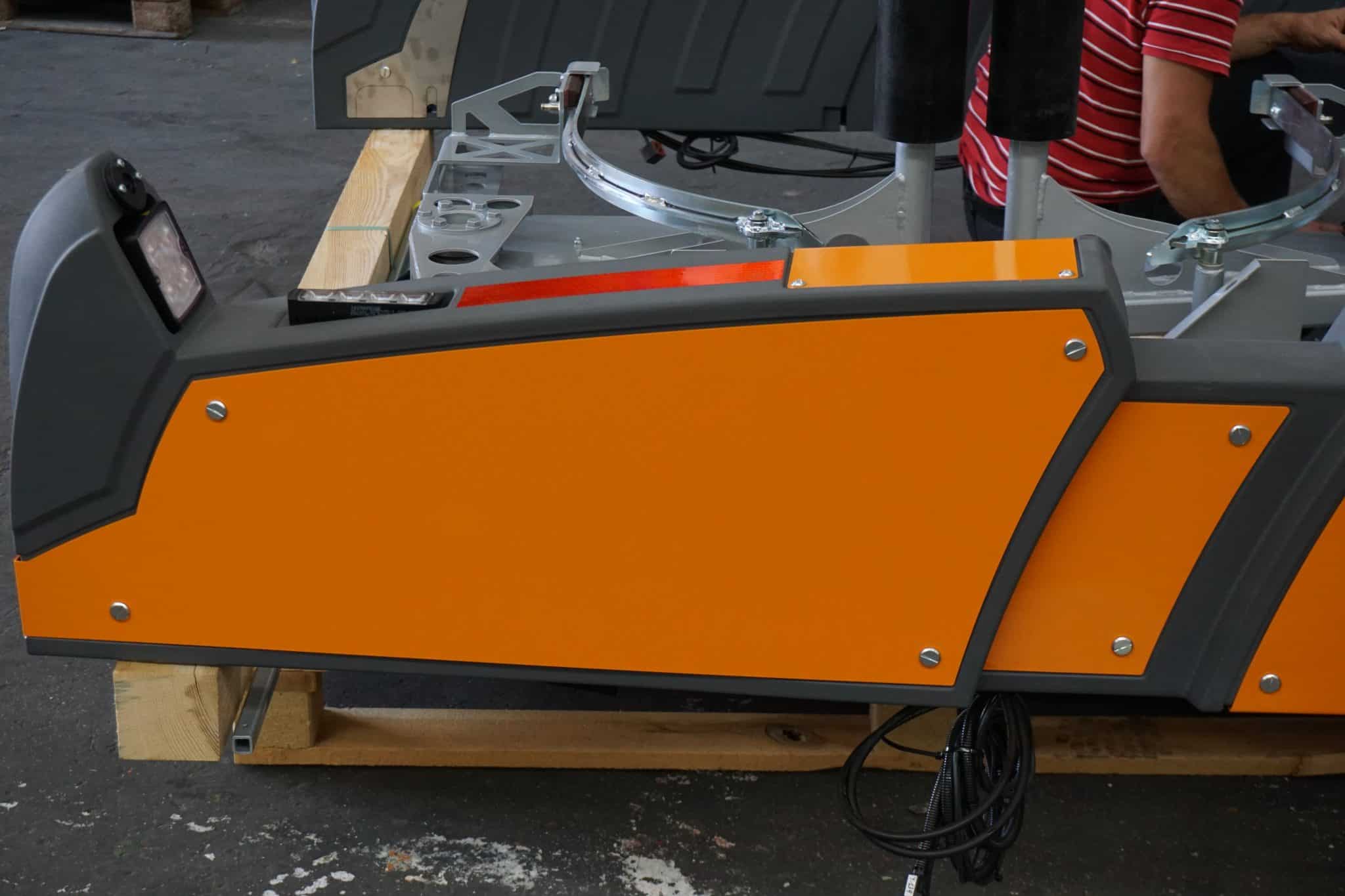