The game-changing impact of BigRep 3D printers in wind turbine manufacturing is reshaping the industry.
These printers introduced resilient plastic tooling that outperforms traditional steel, offering lightweight yet robust solutions that resist deformation and enable early fault detection crucial for precision assembly.
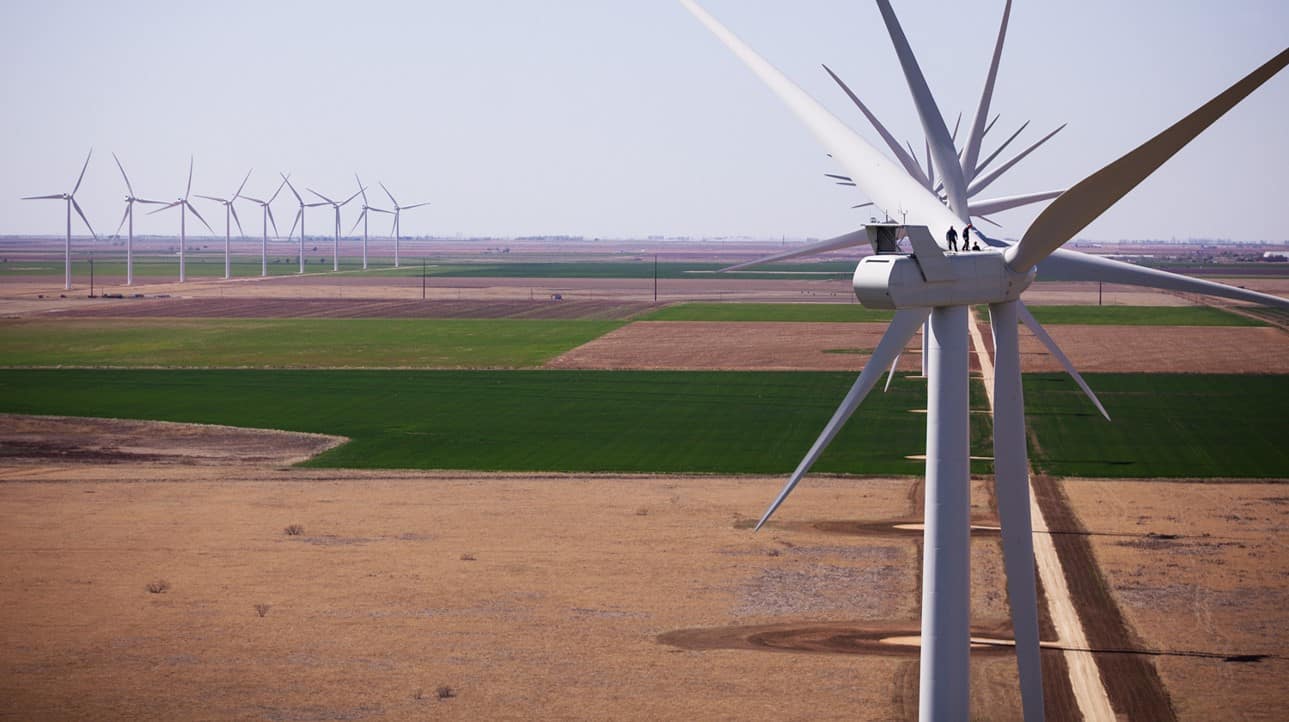
The transition to advanced polymer-based 3D-printed tooling has slashed lead times, reduced costs, and achieved precision surpassing traditional manufacturing standards. Moreover, specialized materials like High-Temp CF ensure stability amid environmental changes, while smart fixture integration enhances functionality and accuracy.
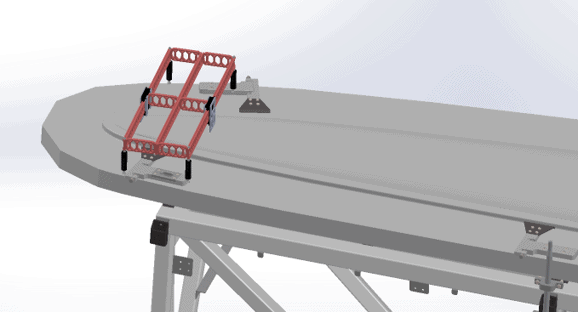
By replacing traditional steel tooling with resilient plastic counterparts crafted through additive manufacturing, Vestas advanced its manufacturing capabilities in wind turbine construction. What started as a project to create tools for assembly and QA for blade assembly then extended to the production of spare parts, streamlined supply chains, and later supported COVID initiatives.
With 3D printing, Vestas aligned their production process with their vision: sustainable energy solutions powered by sustainable manufacturing practices.
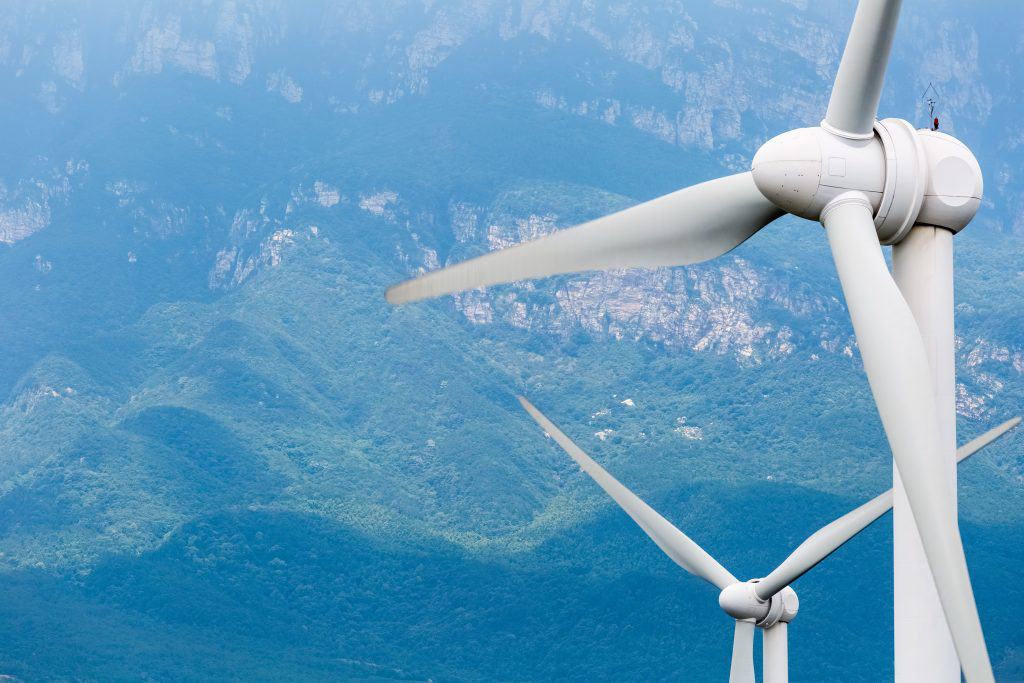
THINK BIG.
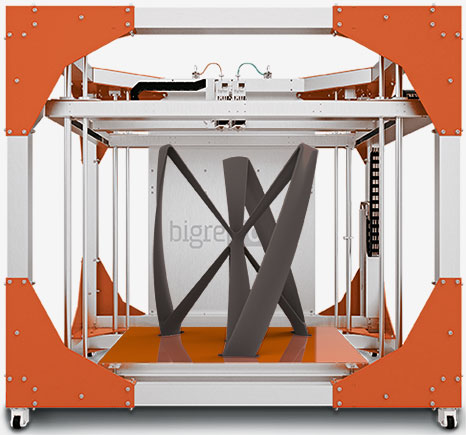
Large-Format Printers for Industrial Applications
Get Started Today!
We are excited to help you get the most out of your application. If any of our materials, equipment, or services can assist with solving your manufacturing design challenges, feel free to reach out! With additive manufacturing still in its infancy, there are many challenges ahead for this technology to be realized at full potential.
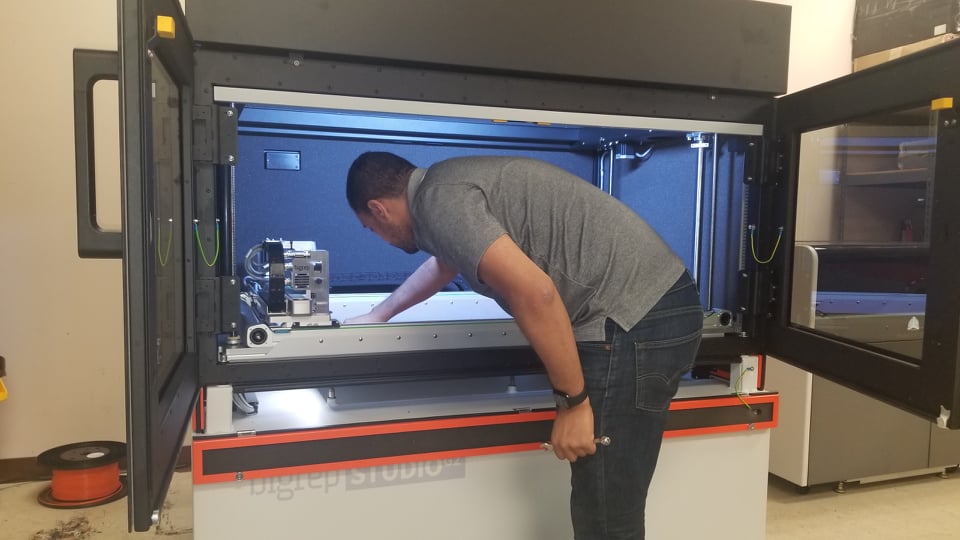
This article was originally published by BigRep – https://bigrep.com/posts/vestas-wind-turbines-3d-printed-tooling/