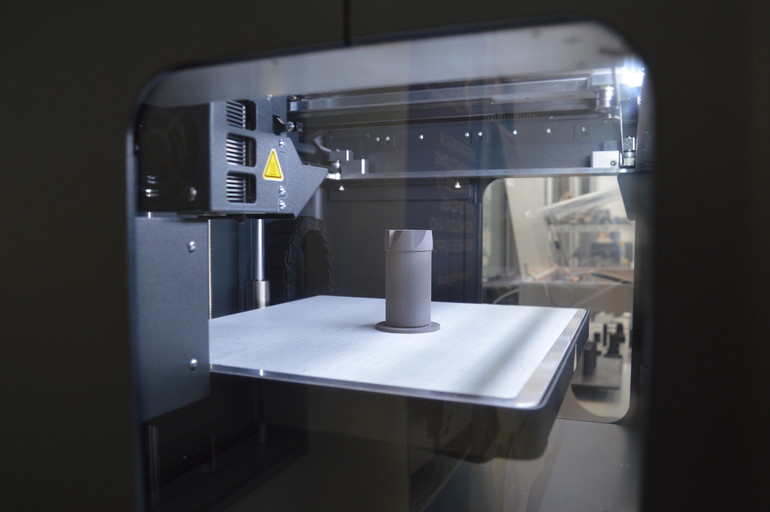
Medical supplies ranging from face masks to ventilators are in short supply. Despite big medical companies like GE ramping up production, the number of Covid-19 hospitalizations will exhaust the availability of FDA-approved ventilators and other medical gear.
At this time of crisis, the private industry is starting to step up. Already, major manufacturers like GM and Ford have spoken publicly about producing desperately needed medical equipment to help in the fight against this deadly pandemic.
But it’s not just these large carmakers that can play a vital role. The 3D printing industry can also be instrumental in the production of essential medical gear. We’re already seeing the benefits of the speed and innovation enabled by 3D printing.
For example, in Northern Italy, a local 3D printer designed and produced a replacement valve used for a lifesaving ventilator when the supplier to a major hospital ran out and had no way to quickly get more. Additive manufacturing presents itself as a critically important supply chain enabler. Where the supply chain for critical medical equipment is faltering, additive manufacturing can step in with speed, strength, growing scale and most importantly flexibility.
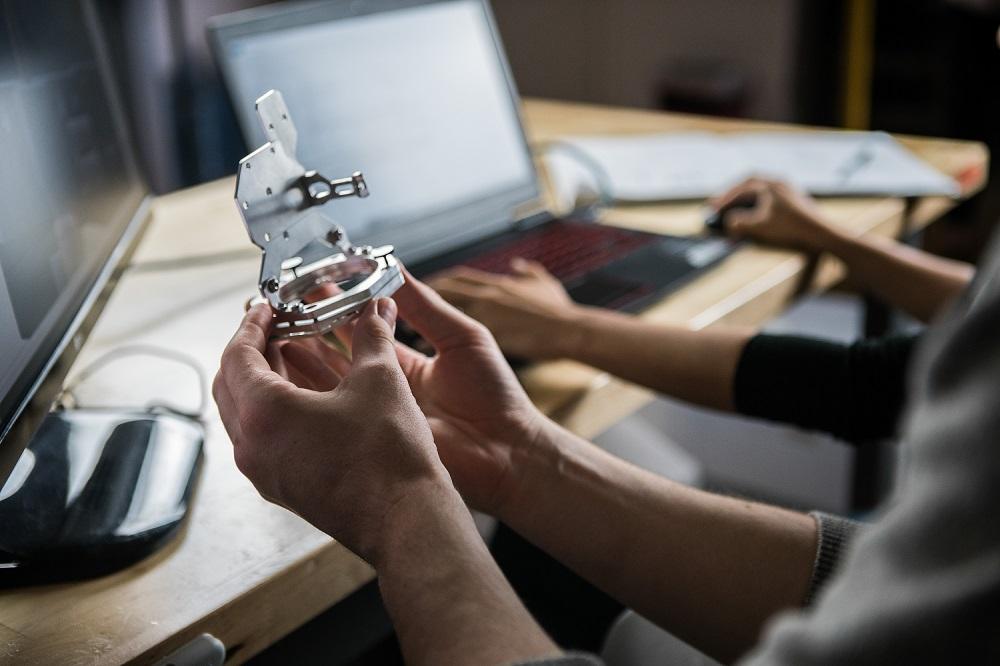
There are three categories in which additive manufacturing can play an immediate and critical role – as part of a coordinated effort with government, health authorities and medical equipment manufacturers to guarantee reproducibility of product quality to set industry specifications.
- Category 1 response: 3D printing for Personal Protective Equipment (PPE) such as face masks
- Category 2 response: 3D printing for Medical Device Component Manufacturing such as venturi valves and other components for ventilators
- Category 3 response: 3D printing for Building Ecosystem Components such as hands-free door openers
Additive manufacturing can be so effective in the fight against coronavirus: it doesn’t rely on a global supply chain. Traditional manufacturers in the UK are now stopping production as borders close to try to prevent the spread of the virus. That means there is no longer a seamless global supply chain to source materials.
Additive manufacturing, by contrast, enables a company to shift its sourcing of parts from remote locations like China to on-site production facilities. It also accelerates time to market, because 3D manufacturers can make needed parts in a matter of hours, solving the current problem of companies waiting in vain to receive parts from global suppliers. If companies can produce parts themselves, without relying on global suppliers, they’ll be in a stronger position to get their products to market and address this crisis.
Manufacturers should be working to identify which parts currently purchased from a third-party supplier might be better developed internally. Many manufacturers are working furiously to qualify new suppliers around the world and source the parts they need at the lowest price. But, with additive manufacturing, they no longer need to source those parts from different suppliers. Instead, they can simply search for the availability of materials and then begin the process of building those parts in-house. Not only will they reduce the time and money it once took to purchase and transport parts, but they will also greatly speed time to market, which is crucial in these unprecedented times.