3D Scanning & Reverse Engineering a Custom Wrench Socket
The Problem:
Often, engineering and manufacturing teams find themselves in need of a custom tool to streamline their workflow. A machinist at one facility fabricated a custom wrench socket by hand for a specific purpose, cutting the metal until it gave him ample purchase on the part to apply torque. After the tool was created, it was desired to duplicate it in CAD, and therefore allow the simultaneous manufacture of multiples through automated machining instead of the single machinist spending his time repeating the process manually.Traditional Method:
Traditionally the machinist must either record all cuts made for the custom fitment of the tool, or measure the component upon completion. These measurements would then be used to redraw the geometry in CAD. On simple parts, this may work fine. On geometry that would be difficult to measure, this is a slow process, and care would have to be given to ensure such measurement were accurately taken.NeoMetrix Solution:
The customer’s wrench socket was scanned with Creaform’s HandySCAN 700 hand-held scanner. The 3D scanner required no surface preparation, and captured the complete geometry of the part very quickly. Creaform’s included software, VX Elements, generated a polygonal mesh to be imported into Geomagic Design X for reverse engineering. Using Geomagic’s advanced modeling tools, NeoMetrix Technologies‘ engineer quickly generated a solid model, ready to send to a machine for manufacture.NeoMetrix Advantage:
Certain measurements present a challenge to perform by hand, such as the exact depth of this socket which terminates in a radius. Tooling with many features may also be tedious to record, and therefore susceptible to human error. 3D scanning completely captures the entire geometry as it relates to itself within the accuracy specifications of the scanner (all measurements are within 0.0012″ with no measurement error stacking.) Geomagic’s feature extraction makes the process of recreating the geometry much easier than traditional means, as the surfaces can be modeled exactly how and where they sit in space, opposed to attempting to reference them from other features, then translate that to a 3D environment with no method to compare the two.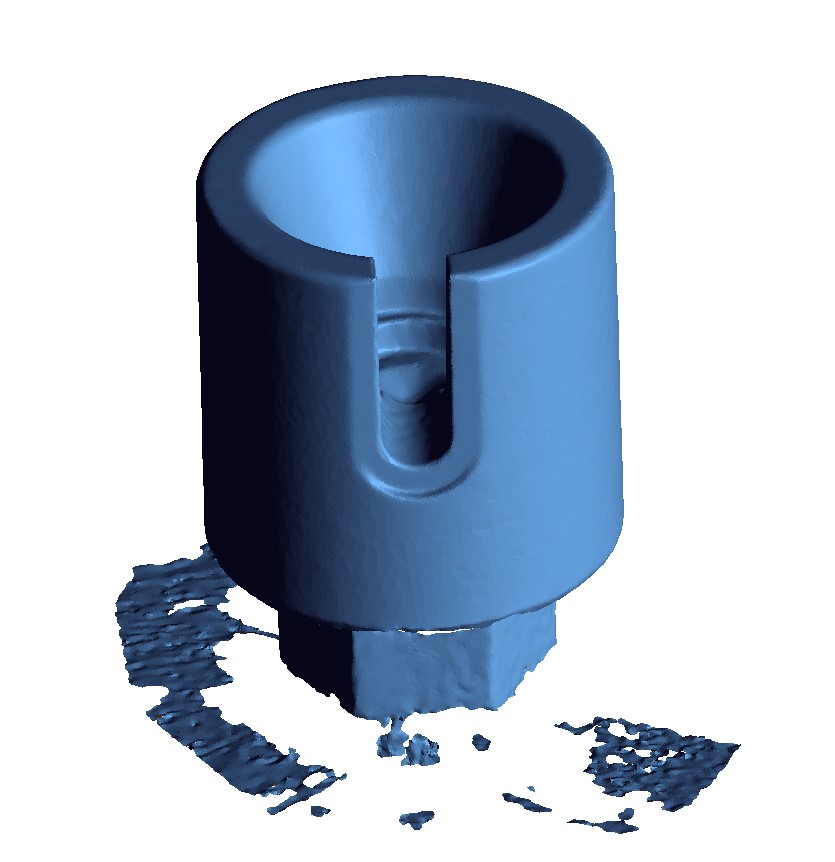
Custom Socket Wrench scanned data
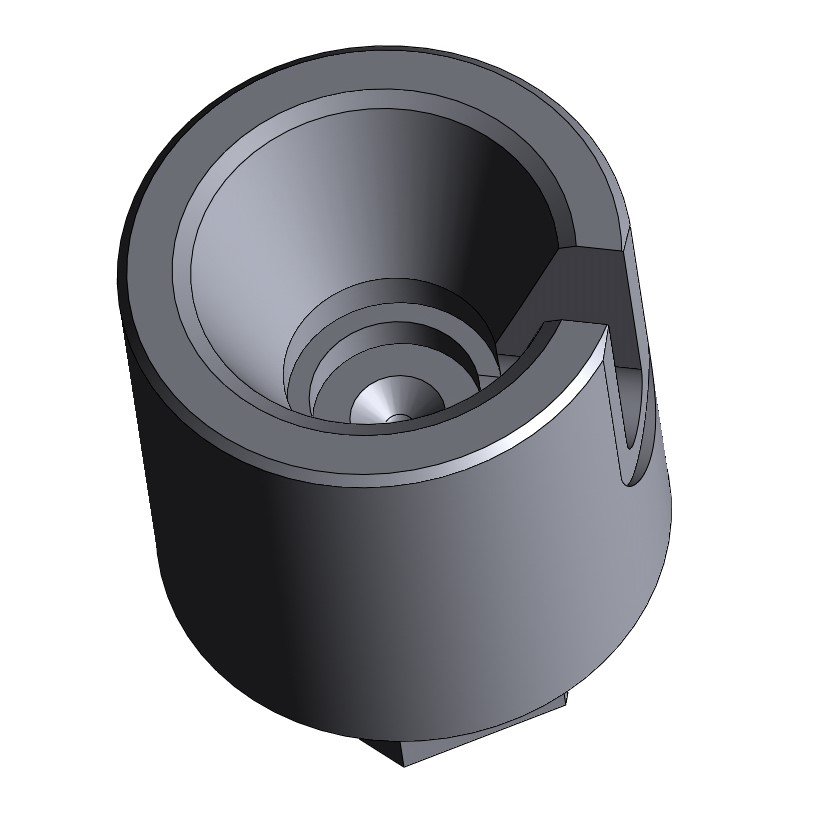
Custom Socket Wrench final CAD Model