Problem:
Cell phone accessory makers require data in order to design their products. However, they normally do not have access to manufacturer’s CAD models. They also need an accurate method to ensure they can bring their products to market quickly with the fewest number of iterations possible in the design process.
Traditional Method:
Traditional methods of design often require purchasing costly cad models from cell phone manufacturers. If that was not an option, designers would attempt to design around a physical phone using hand measurements to create cad data. This was often inaccurate creating the need for multiple design iterations, which would increase the cost of prototyping and delay the time to market.
NeoMetrix Solution:
- Original phone scanned with Konica-Minolta Range 7
- Multiple scans are aligned together to form a single polygon mesh
- Data is aligned to a useful coordinate system.
- Cross-sectional curves are cut at specified locations, parallel to coordinate planes
- Bounding box is developed parallel to coordinate planes at extrema of scanned data
- Polygon mesh is exported as STL file
- Cross-sections are exported as IGES
- Bounding box planes exported as STEP
- Bounding box
NeoMetrix Advantage:
- Rapidly capture part geometry through 3D scanning
- Highly accurate data set from which to design new parts
- STL, and section curves can be imported into customer CAD system to serve as a template for new design
- Human error is eliminated in manually transferring hand-measurements in to CAD
- Initial designs are significantly more accurate, cutting the number of design iterations
- Fewer design iterations reduce prototyping costs, and improve time to market
Get Started Today!
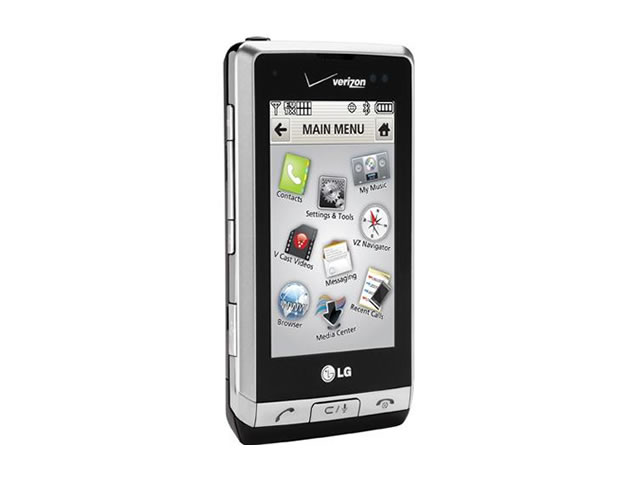
Figure 1 – Original Cell Phone
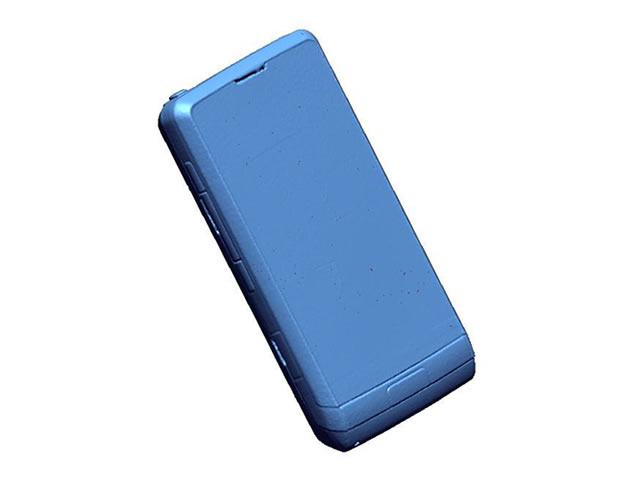
Figure 2 – STL file from scan data
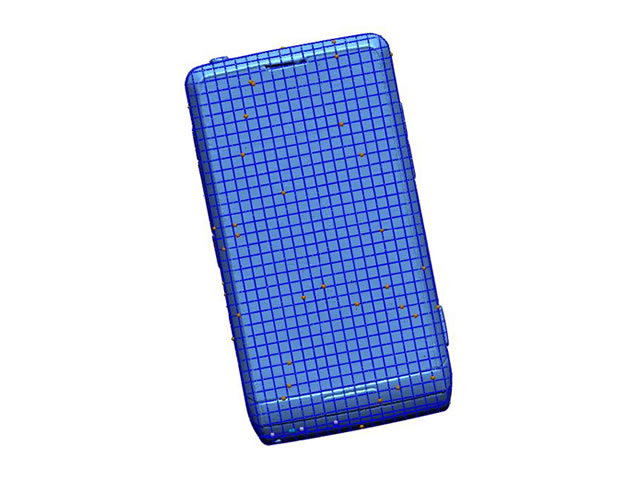
Figure 3 – section curves