Reverse engineering allows manufacturers to understand how a part was designed in order to either replicate it, or make modifications or enhancements.
Reverse engineering is also known as back engineering. The reason? Reverse engineering teams work “backwards” from the original design process; they start with the end result, deconstruct the product, and carry out assessments and measurements in order to obtain the physical design information.
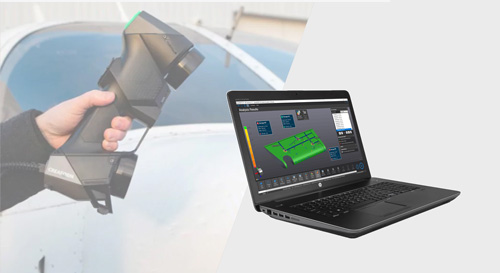
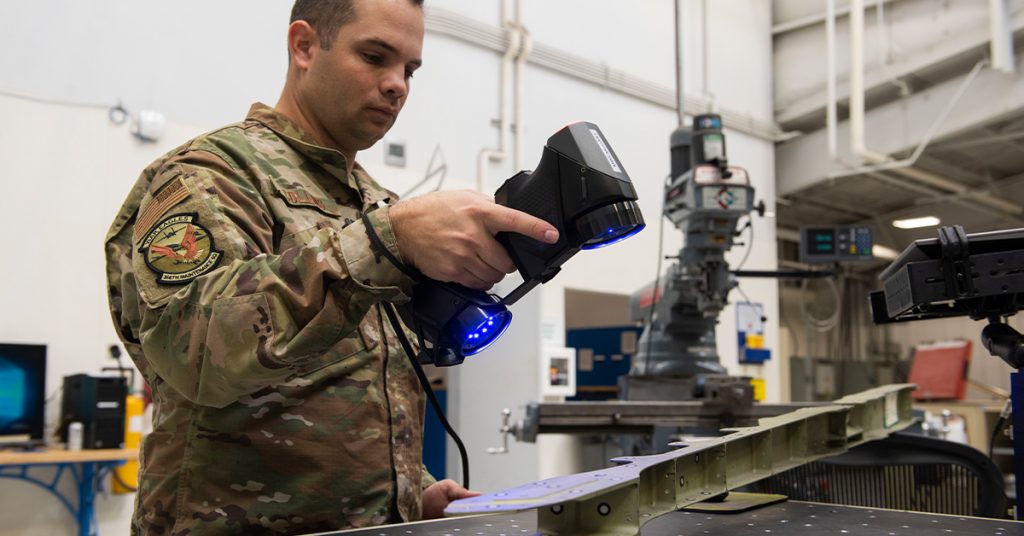
History of Reverse Engineering
While many people believe that reverse engineering started in the 18th century with the dawn of the factory system, this is not the case. In fact, reverse engineering has existed since the beginning when humans made things, such as wheels, carriages, and even architectural infrastructure. In order to recreate these objects, reverse engineering—as rudimentary as it was back in the day—was used. The object’s dimensions were taken, either as a whole or in parts, and rebuilt.
For example, the Roman Army, which did not have a standing navy until after the First Punic war, was able to reverse engineer a Carthaginian quinquereme in 264 BC. Thanks to the Romans’ renowned ingenuity, they created—and optimized a fleet of 300 ships in 3 months that was capable of out-matching the Carthaginian fleet in numbers and intricate naval manoeuvres.
Reverse engineering techniques have greatly evolved since those bygone eras. While reverse engineering may have started with military applications, it is now useful in many different fields, including manufacturing.
Over the years, many different technologies have been used by manufacturers in order to acquire measurements of an object and import them into CAD software for 3D modeling.
Coordinate measuring machines (CMMs), probe systems and robot-mounted articulating arms have been widely used for reverse engineering and eliminate the issues associated with manual methods. The choice of using one 3D measurement technology over another depends on the required tolerance levels, data density and speed, the part’s features, and the device’s line of sight and ease of use.
Nowadays, manufacturers are increasingly using portable 3D scanners for reverse engineering. The reason? They generate highly accurate, reliable and repeatable results, just like the aforementioned technologies. However, they are faster. They are also easy to use by operators of any skill level and 3D data of a part can be acquired right on the shop floor.
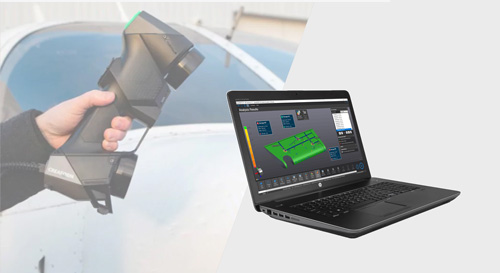
The most versatile 3D scanner on the market for inspection and demanding reverse engineering
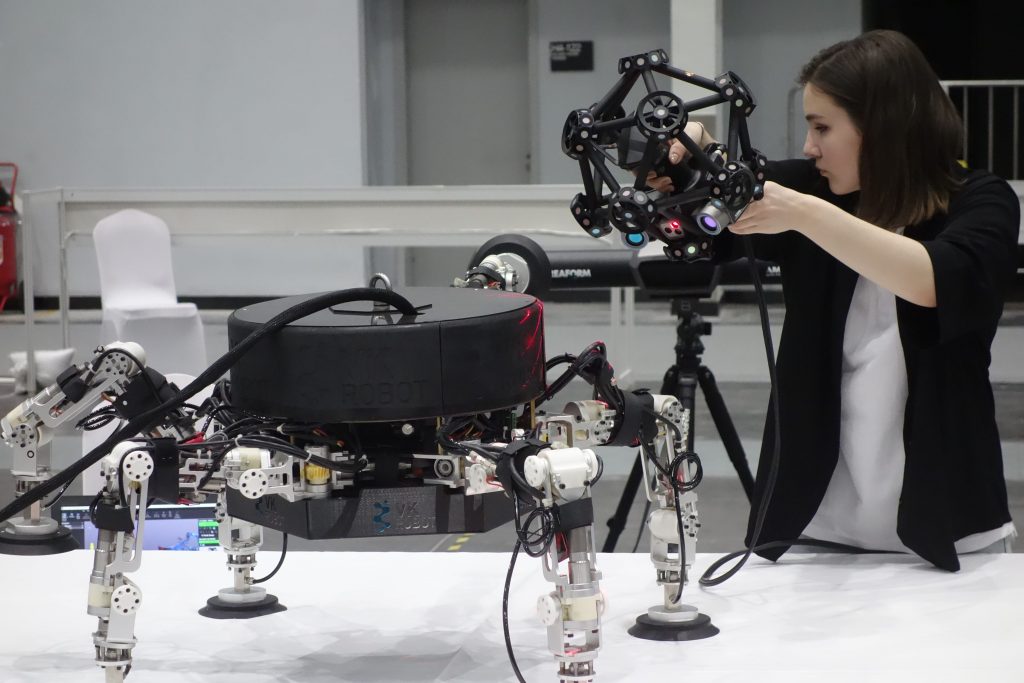
An Everyday Tool
For manufacturers, reverse engineering is a critical process. There are many common uses of reverse engineering.
Reverse engineering is often used when there is limited knowledge on a part’s engineering, the original documentation is missing, or if there are no 2D or 3D drawings/CAD models. Reverse engineering is particularly important if a part’s design information is only on paper or reliant on human memory.
Companies also reverse engineer parts when replacement parts from an original equipment manufacturer (OEM) are not available, either because the OEM no longer creates them or the OEM no longer exists.
Reverse engineering is also used to optimize assemblies for production and enhance products with new features.
Manufacturers also use reverse engineering techniques to improve a part that is failing, or reproduce handcrafted parts or assemblies.
Sometimes, reverse engineering is simply used to build a digital archive of parts or create a virtual environment for future reference.
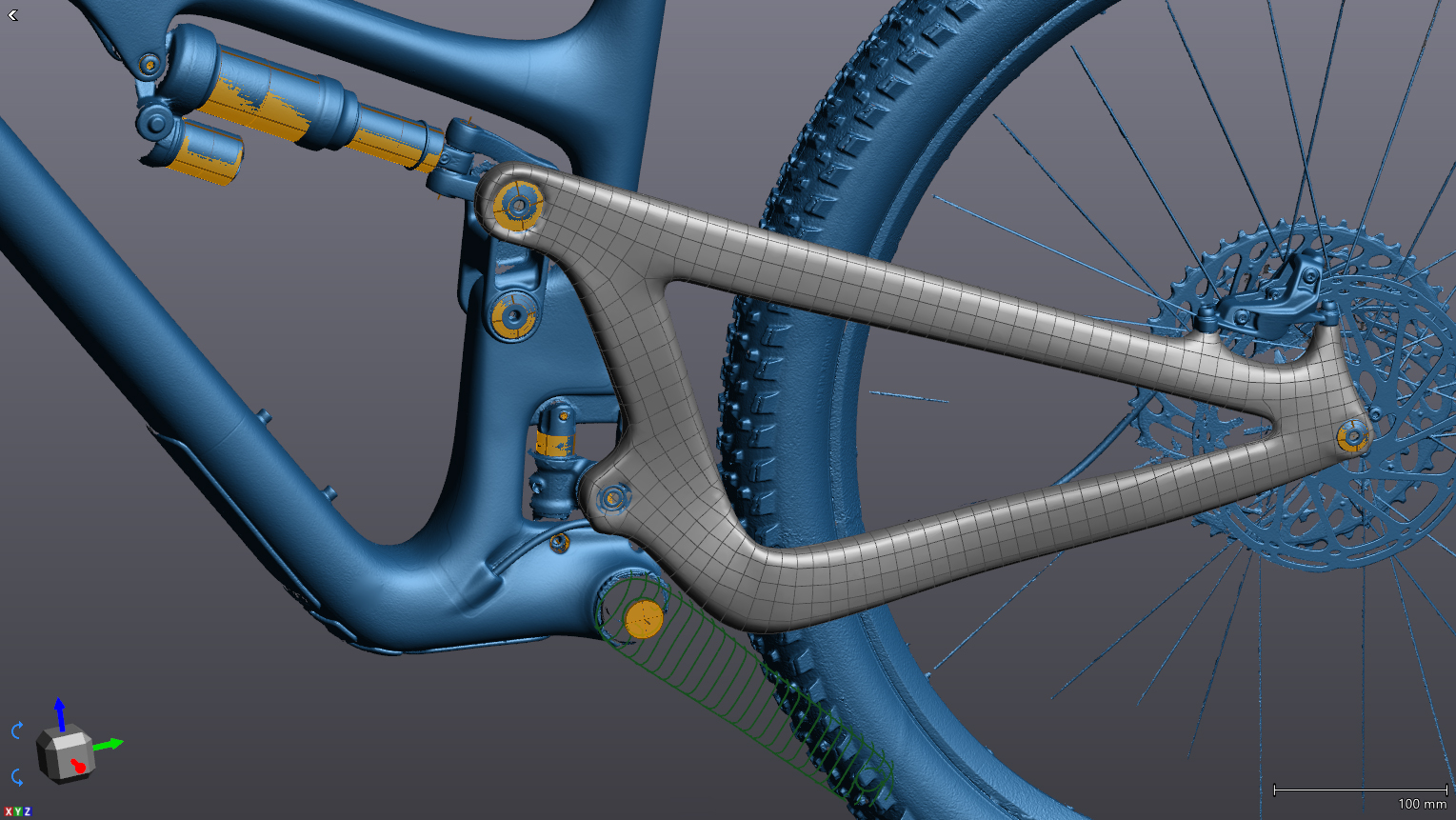
Benefits of Reverse Engineering
Reverse engineering is important for manufacturers in a number of ways.
Reverse engineering can reduce the risks associated with legacy products and products with vulnerabilities. Reverse engineering can reproduce replacement parts as well as identify and help to correct faults in products.
Furthermore, reverse engineering can accelerate product innovation. For example, an engineering team can explore designs of existing products and look for ways to increase their performance, upgrade features, or find ways to slash production costs.
Manufacturers leverage reverse engineering to quickly produce parts rather than purchase components from an OEM that may have long lead times and demand premium costs.
Reverse engineering can also be a key strategy in a manufacturer’s proactive maintenance plan. By reverse engineering critical components before they fail, a manufacturer can stock replacement parts and reduce unplanned downtimes.
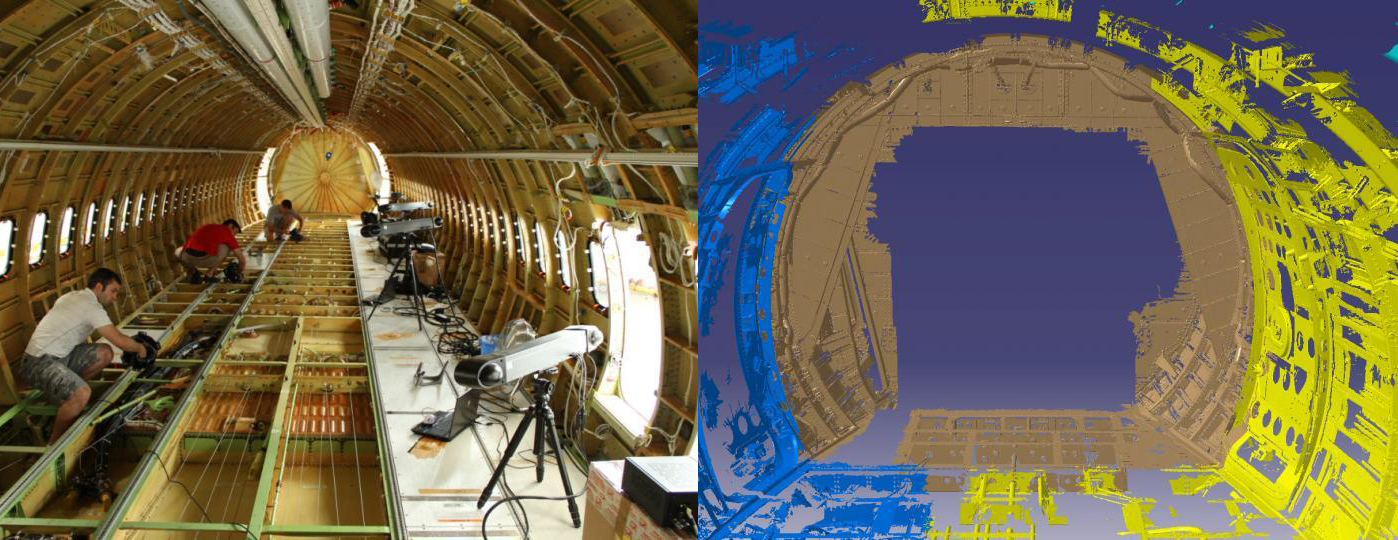
Aerospace industry
The aerospace industry uses reverse engineering to:
- Carry out aerodynamic analyses
- Develop maintenance plans for aircraft
- Add, enhance or fix aircraft components
- Tooling manufacturing
Automobile industry
Automobile manufacturers often carry out reverse engineering for:
- Studying the competition
- Digitalizing parts of older vehicle models
- Understanding issues with vehicle components
- Producing replacement parts
Tooling companies
Tooling companies rely on reverse engineering to make:
- Jigs
- Fixtures
- Dies
- Molds
- Parts for machine and cutting tools
- Etc.
Consumer goods
Manufacturers of consumer goods opt for reverse engineering to:
- Quickly develop prototypes
- Test and validate conceptual designs
- Analyze competitor products
- Documenting and archiving different design iterations
Art and heritage preservation
Experts in the art and heritage preservation sector depend on reverse engineering for:
- Recreating works of art for educational purposes
- The digital preservation of visual arts, like paintings, sculptures and ancient archaeological artefacts and historic buildings
- The restoration cultural artefacts
Let’s work together!
Learn more about our 3D Scanning Services
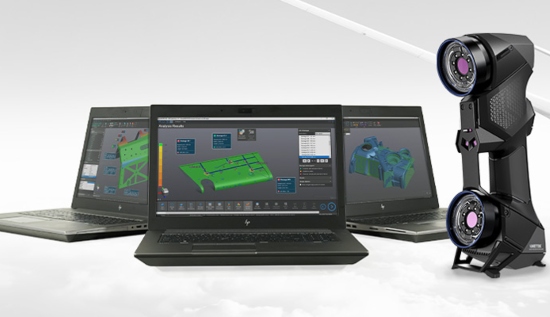