Integrating 3D printing into the automotive industry’s product development and prototyping workflows is now a widely accepted strategy to reduce costs and lead times. Despite the acceptance, later stages of industrial production remain ripe for additive manufacturing innovation. One recent area of rapid growth is in 3D printed production tools for use in serial production.
3D Printed Production Tools Reduce Workflows
Walter Automobiltechnik (WAT), a Berlin-based automotive manufacturer specializing in the production of vehicle frames, is dramatically improving workflows in their facilities with custom 3D printed tools. The production tools, created with WAT’s BigRep ONE industrial 3D printer, are implemented into quality assurance workflows, reducing time spent on control lines with simple jigs to help semi-automate quality assurance checks. The control systems have cut workflows in half, freeing employee time and reducing order fulfillment time.
The BigRep ONE v3 was created to make 3D printing for large-scale objects as easy as possible. Every detail has received our full expertise and experience — for better quality, higher speed, and increased safety.
By 3D printing jigs for their new control systems, WAT has sidestepped the significant costs traditionally associated with custom industrial tools. Rather than commission a machine shop to manually shape the jigs from aluminum or other metals, WATs BigRep ONE is used in house to innovate their workflows on demand.
“Because I can print one cubic meter, I can produce really large components – which you can see with these jigs,” said André Lenz, an engineer at WAT and the technician responsible for designing and printing useful parts for WAT’s Berlin facility. “If we had made them out of steel or aluminum, for example, it would have been incredibly expensive and above all heavy and made from multiple parts.”
Like many companies that add a large-format 3D printer to their roster of industrial equipment, the value for WAT hasn’t ended with their primary application. Lenz has been designing and printing helpful aids around the facility for everything from trays to sheaths for holding tools within easy reach.
For WAT, the decision to invest in a BigRep ONE for automotive 3D printing has been game changing. They’ve cut costs and reduced workflow on essential manufacturing processes to help deliver their product at the cost and within the time their customers expect. But quality assurance is just the beginning as WAT continuing to develop more additive manufacturing applications to create more efficient automotive manufacturing processes.
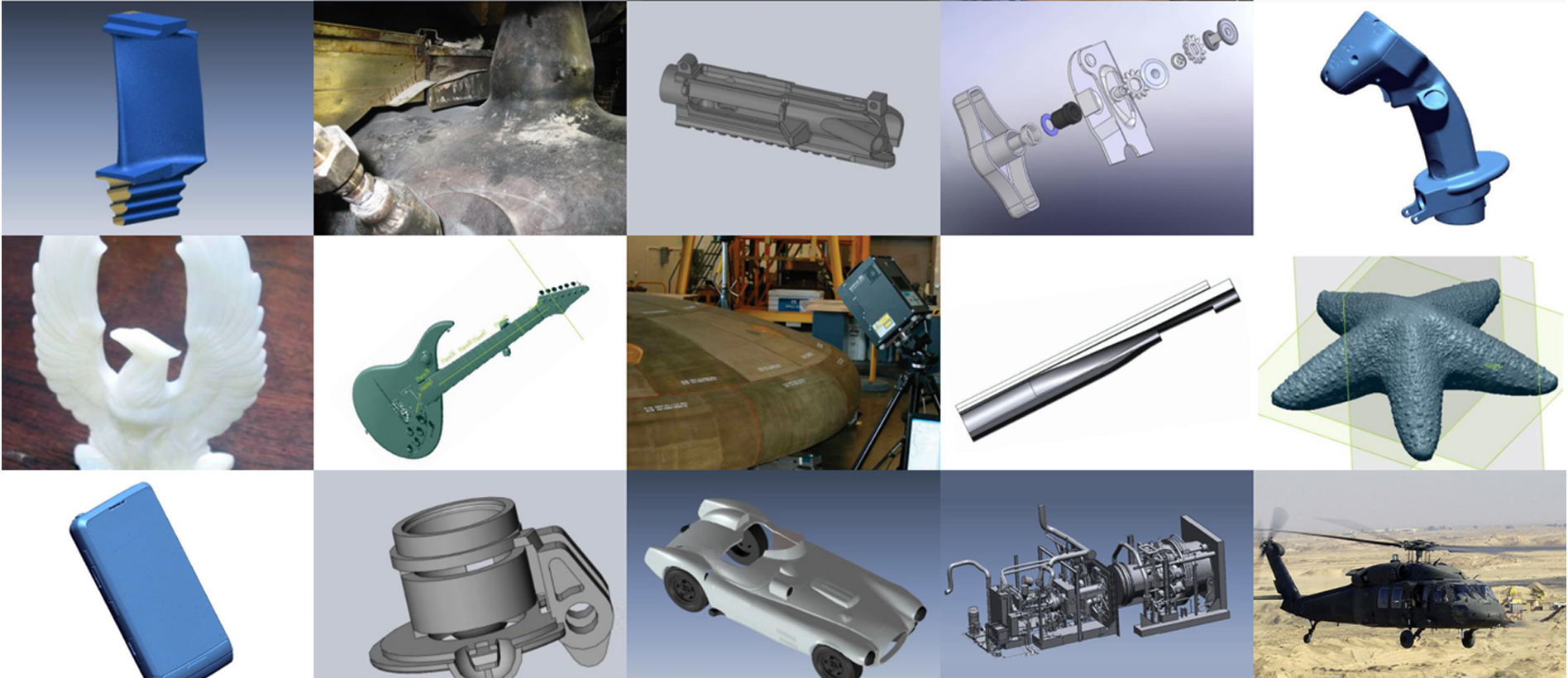