3D Printed Angle Bracket
The Problem:
One of our applications engineers was assembling a custom rig out of 80-20 aluminum extrusion, when he ran into an issue. More corner brackets were needed than expected. The parts were out of stock, and backordered.
Traditional Method:
Traditionally, there would be 2 options when a metal corner bracket is unavailable. The first would be to simply wait for the part to come back in stock, but this can sometimes take weeks or even longer. The other option is to have the part custom machined. This is usually expensive and can also take a few days to receive the parts. This is not reasonable for a relatively inexpensive project.
NeoMetrix Solution:
With a quick google search, it was discovered that a CAD model for the bracket already exists. With our in-house printing capabilities, we could have new brackets in hand in a matter of a couple hours.
The first step was to pick a material and printer appropriate for the application. Since it is a corner bracket, intended for heavy use, Onyx material, printed on a Markforged printer is the best choice, as it provides a high amount of strength with no complicated post processing or modifications.
With this decision made, the CAD model was uploaded to Markforged’s Eiger 3D printing software. The software analyzes the model, and prepares it for printing based off of user defined parameters, such as material, resolution, infill, etc. Once saved, we were able to see how long the print would take, and how much material it would use.
NeoMetrix Advantage:
What would have taken days or even weeks to resolve, was able to be fixed in a few hours at the cost of only $2.70 in material. 3D printing relieves the stress of uncertainty from relying on outside suppliers or service providers by bringing the option to create components quickly and cost effectively in-house.
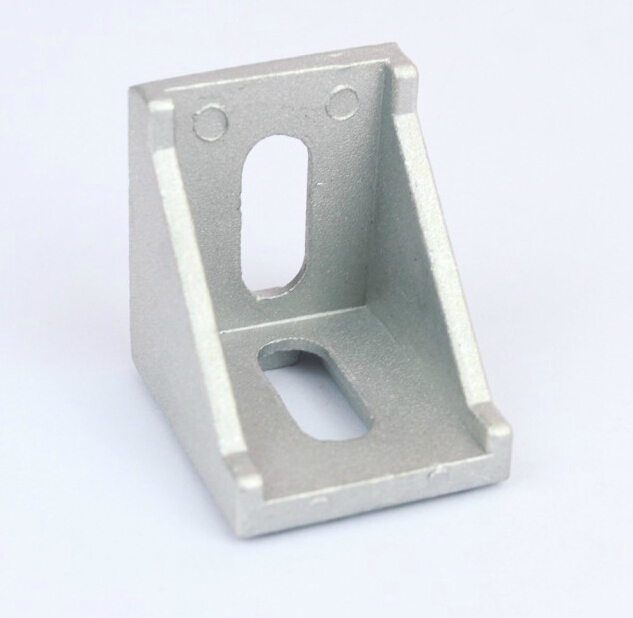
Original Aluminum Bracket
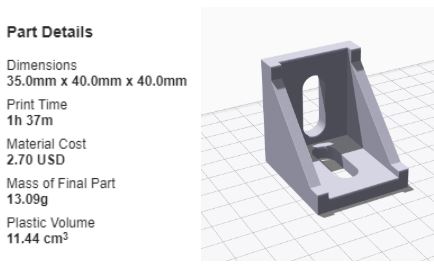
Build Time and Material Cost

3D Printed Parts Completed within Hours!
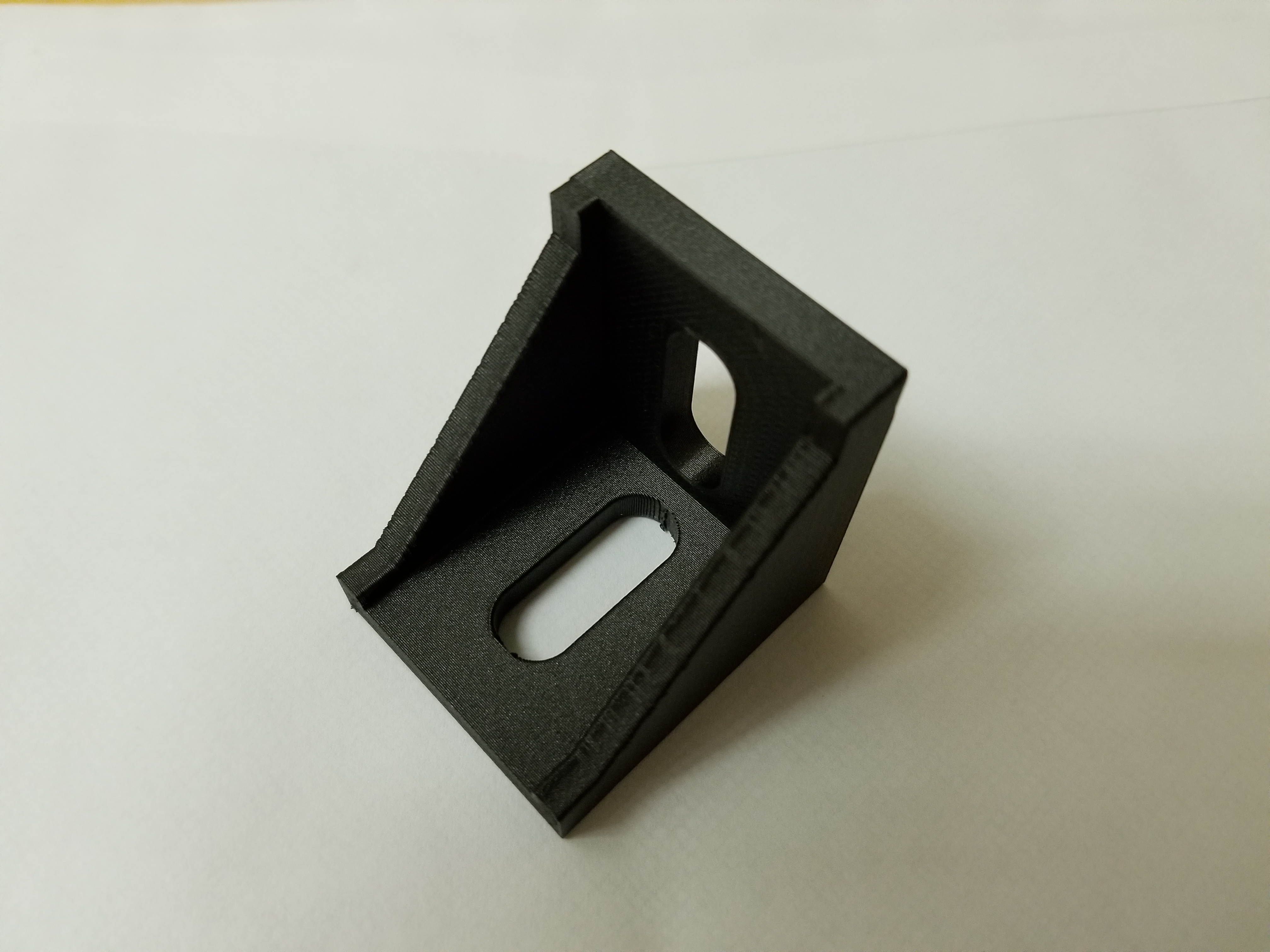
Final Product