Members of USA Luge seeked to find the best ways to produce the fastest and most efficient sleds, so they embarked on a quest to find answers to the following questions:
- How can more comfortable sleds be manufactured to better fit each of the athletes’ bodies and enable them to drive their sled more precisely and ultimately, faster?
- How can the aerodynamics be improved to facilitate the athlete’s run down a track built with steep banks and inclines?
- How can equipment parts that performed well on particular tracks and in specific races be catalogued and reproduced quickly and easily?
In this article, you’ll learn all about the Olympic sport of luge and find out what it takes to win gold!
When 3D Measurement Technology Gives an Edge to Olympics Athletes
When American athlete Chris Mazdzer won the silver medal at the 2018 Games in PyeongChang, it was a historical first for USA Luge, as no athlete had ever medaled in the male singles luge event at the Winter Games. Before triumphing at the Olympics, Mazdzer and USA Luge went through many tests in their quest to go as fast as possible and reduce the wind drag to a bare minimum.
The sleds used by USA Luge are engineered and built with the assistance of the latest developments in design technology using specific manufacturing processes that are comparable to those used in Formula 1. These racing sleds are pieces of aerodynamic machinery built of fiberglass, composites and steel that ride on two highly polished runners and can reach top speeds of more than 140 km/h (90 mph) through hairpin turns, steep banks, and sharp declines.
[A Luge Sled: A High-Tech Machine]
With extensive research and emphasis on analytics and sport technology, luge sleds are designed for utmost aerodynamics, minimal friction, and top speed.
Tailored to ones specific body, based on his or her height, weight, and proportions, the luge sled consists primarily of:
- Two steels that are the only part of the sled that engages the ice. They are made of metal and are sharp enough to maintain control but not so sharp that additional friction is created.
- Two bridges connect the runners to and support the pod.
- Two runners (of kufens) that are usually made of fiberglass and are the sled’s main steering mechanism. The curved section (or horn) of each runner is flexible. Using their legs and ankles, sliders apply pressure to one or the other horn in order to steer through the course. (They can also steer by making small movements with their shoulders to shift their weight.)
- The racing pod is the platform on which the slider lies. It’s usually made of fiberglass.
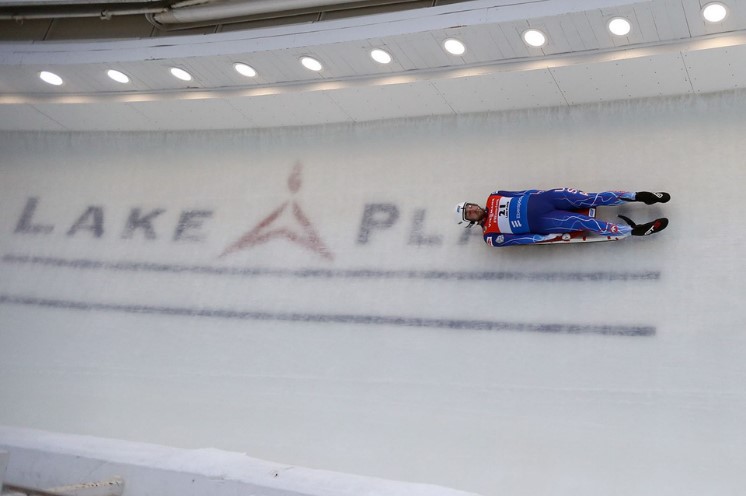
Advice and Support in 3D Scanning, 3D Modeling, and Reverse Engineering
In order to the USA to bring home medal in this sport, it is crucial to have a state of the art sled and equipment
Discussions between Jon Owen, Mark Grimmette, and the Creaform team about the idea of bringing 3D measurement technology into the design and development process of advanced luge sleds started during the International Manufacturing Technology Show (IMTS) a few years ago. USA Luge was looking for advice and support from a market leader in 3D scanning to increase the performance of their sleds by improving the athlete’s position on the pod and raising the aerodynamics. “Our goal remains to make the equipment more comfortable and more aerodynamic for our athletes,“ says Mark Grimmette, “so they can drive the sled better, easier, and faster and achieve the results that they want.“
Could 3D scanning be the solution to subtract those few precious tenths of a second needed to lead American sliders to the fastest time at the 2022 Games in China? In search of this answer, Creaform and USA Luge teamed up in the following projects.
Moreover, thanks to the HandySCAN 3D scanner and its blue laser technology, offering a mesh resolution of 0.1mm, the team could capture the finest details of the winning steels with the needed resolution to reproduce them for future races and, thus, repeat the previously obtained success.
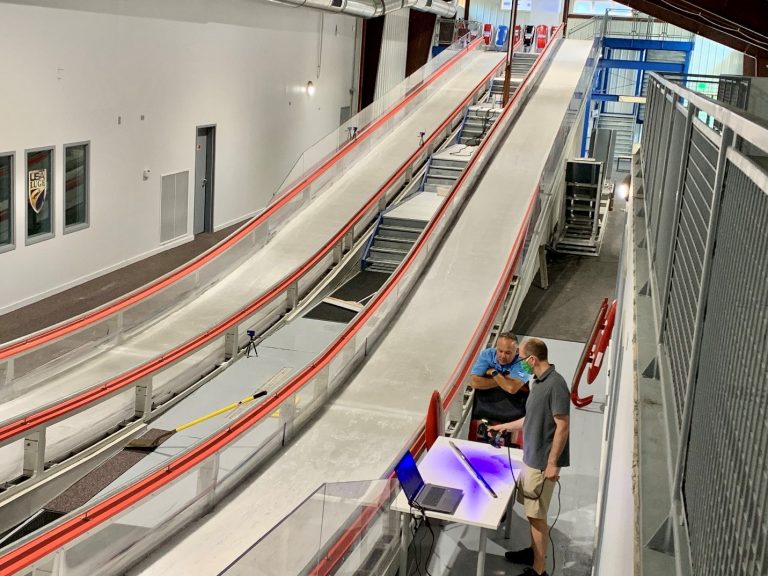
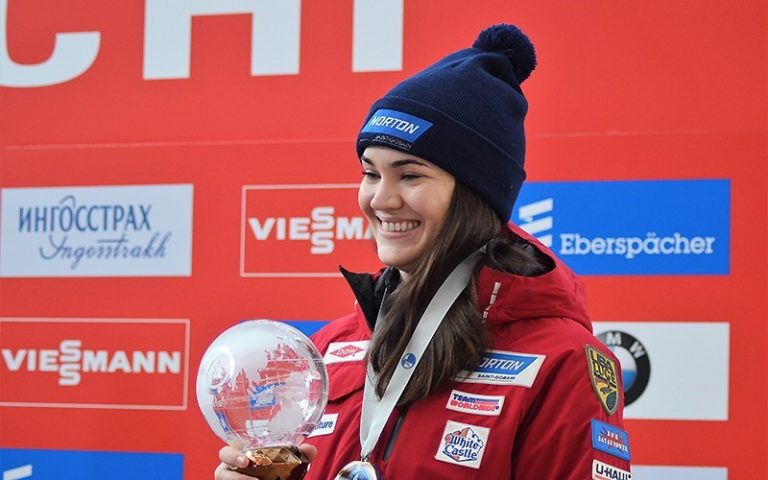
Project B: Improving the Aerodynamic Shape of each Athlete’s Pod with 3D Scanning and Additive Manufacturing
Prior to introducing 3D scanning into the manufacturing process, the task of tailoring the pod to the athlete’s body was done by hand, which required many design iterations to make the racing platform as perfect as possible. Then, the technical team built a mold from this custom-made pod to reproduce its exact shape for pods to be used in competition. Nevertheless, if the pod needed adjustments after testing the aerodynamics in a wind tunnel, the team didn’t have the ability to modify it.
“We do a lot of wind tunnel testing for aerodynamics,” says Jon Owen. “Every time that we are in the wind tunnel lab—in a controlled environment—and we have the number in front of us, without a race going on with the emotion and the fanfare, you know that if you could just tweak that and do that, it would enhance our performances. With Creaform handheld 3D scanners, this is exactly what is happening.“
Now, thanks to 3D scanning, the manufacturing process has become more efficient. After shaping the pod’s design by hand, the model is 3D scanned, and VXmodel scan-to-CAD post processing software is used to verify that all surfaces are nice and smooth, without defects, and symmetrical from left to right. If changes are needed—based on new aerodynamic information—they can be easily adjusted in the CAD model. Then, the technical team is able to 3D print the mold and build the pod, which is now more precise than it was with the old manufacturing process.
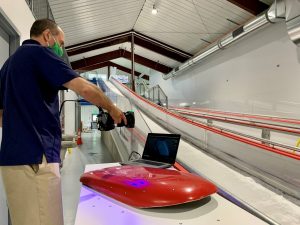
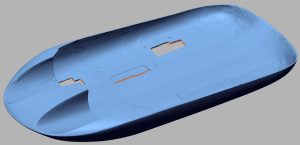
From 3D scanning nearby the track to CAD Model of the pod
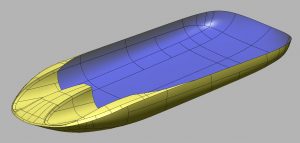
Project C: Building and Reproducing Complex Organic Shapes
Horns are unique parts, different for each athlete and difficult to reproduce due to their complex organic shapes. Because every slider has different leg lengths and foot shapes, especially in doubles, this particular part must fit perfectly. “Especially in that area,“ emphasizes Jon Owen, “because it is the first thing that the wind sees at the very front of the sled, everything needs to be as neat and tidy as possible.“
Using the HandySCAN 3D, Team USA has been able to scan these complex organic shapes easily in order to undersize and attach them to the rest of the runner and wrap them with carbon fiber. This is another step of the manufacturing process that was tedious before Creaform came on board. “3D Scanning is helping us to build and reproduce such complex parts in a much simpler, easier, and quicker way,“ adds Mark Grimmette.
Vision for the 2022 Winter Games in China
With the help of the metrology services and engineering services, Luge USA has been able to 3D scan their equipment in order to create molds using Fused Deposition Modeling (FDM) technology. The technical team has chosen 3D scanning and 3D printing technologies—through their collaboration with Stratasys—over more traditional molding methods because of their ability and flexibility to iterate more quickly and efficiently, letting the team try out a variety of different versions of a sled before setting off on the track for a competition.
“Creaform helps us fine-tune our product development process, and we couldn’t have done that without their help,“ adds Jon Owen. “We’re really excited about a long-term prospect for the future and how we can continue to improve our process and performance.“
The next two years will be very exciting, as new parts will be added to the sleds. Creaform is looking forward to seeing the performance of the athletes and the enhancements that portable 3D scanning technology will bring to the sled design and production.
Will USA Luge win the coveted gold, silver, or bronze medals at the Winter Games in China in February of 2022? For sure, Creaform will be tuned in to watch the competitions and cheer on the athletes.
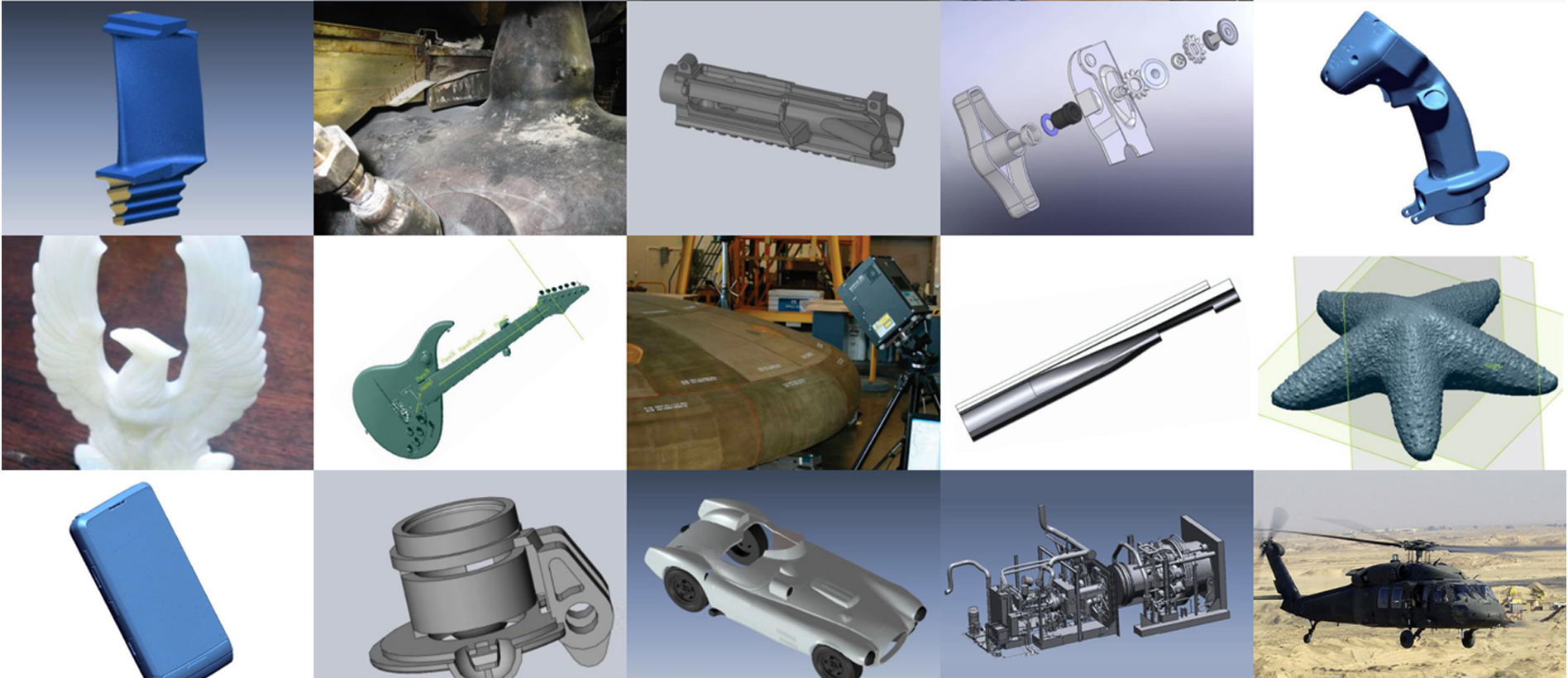