World’s longest plane digitized by the world’s smallest and most accurate handheld 3D scanner.
Scanning the world’s longest airplane in just 18 hours is a challenge, especially if the airplane, the scanning experts and the equipment have to be brought together. In this case the plane, a Jumbo 747-8, was in the US, the scanning team and the equipment in Europe.
After two months of preparation and meetings with Lufthansa to plan and organize the digitalization of the interior of the Jumbo 747-8 it was time to start the trip to the Boeing factory in Seattle.
Two Danish scanning experts and a team from Lufthansa met in Frankfurt to fly together over the ocean. In their hand luggage they were carrying two sets of an EXAscan , and HandySCAN 3D scanners from Creaform which made the trip even more advantageous: Not every day people try to carry such high-tech scanners through customs, so that you need to explain the systems and have to pass an explosive check. In short: You need to be at the airport in time, as you risk long hold ups or, even worse, miss the plane. But everything went well and 10 hours later the scanning team and the equipment arrived in the US.
Get Started Today!
The Digital Process
Once arrived at the Boeing factory, the first thing to do was to inspect the Jumbo during a cabin walk in order to plan the process of the digitalization. The scanning team had only a time frame of 18 hours to scan the interior of the new Boeing 747-8 for Lufthansa, who wanted to have a 3D model for marketing and training purposes.
For the global digitalization of the interior, two long-distance scanners were used. For a more detailed registrations of doors, panels, seats, bins and cockpit two EXAscan 3D scanners. The EXAscan belongs to the HandySCAN 3D family of Creaform and, with an accuracy of 0,040mm, stands out as the most accurate portable 3D scanner on the market today. With the EXAscan it possible to carry out exact 3D scanning projects with a level of details and accuracy that no other handheld scanning system can achieve. The integrated TRUaccuray Technology allows a dynamic referencing which makes it possible to move the part during the 3D scanning session, so that there is no need for a rigid set-up.
As it was not possible to scan at the same time a same area of the plane with the long distance scanner and a HandySCAN 3D scanner, the aircraft was divided into several sections: One person was for example scanning the 1st floor, another the business class or one of the three main parts.
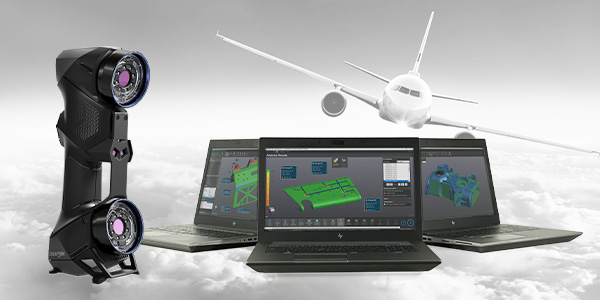
The HandySCAN 3D scanner works together with reflective targets which need to be positioned on the part to be scanned (a total of 5000 targets where used in this project). Serving as referential, targets were for example also placed on both sides of the aircrafts door and its frame. The door sides and the door frame where then scanned and three CAD files were generated which were then merged in the CAD software to one single file. The result was a complete 3D model of the door, which can then be used for inspection and fitting tasks.
“With the limited time frame this was not an easy project, but in the end we made it in 18 hours and everything worked fine. We actually felt like we were on a big team and everybody helped where it was needed.”
Ask us about 3D scanning services and equipment!
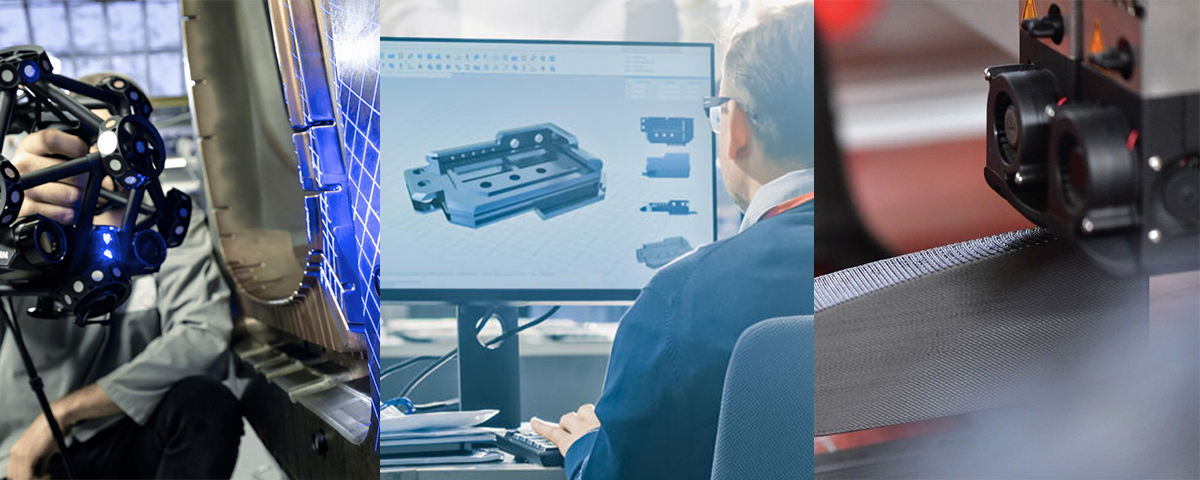