The challenge of maintaining wind turbines is not an easy one. These machines are designed to operate for 20 years, but thanks in part because they’re now furnished with modern acquisition technology and advanced numerical models that can address any condition thrown at them – including heavy loads or bad weather patterns characteristic during extended periods where little activity occurs on-site (such as harsh winters).
Modern turbines are designed for long life and high output. A major part in their success is understanding how to maintain them so they can produce power without any problems or decreased efficiency, even as wear occurs on the components over time. The goal should be maximizing energy production while minimizing unforeseen negative impacts such as vibrations that may compromise integrity The operating conditions need regular monitoring because if something isn’t taken care of soon enough then it could lead directly towards lost functionality.
The Spanish company Nabla Wind Power is part of the Nabla Wind Hub group, an independent service provider that offers unique and multitechnology solutions for wind farms life extension, performance improvement and maintenance optimization.
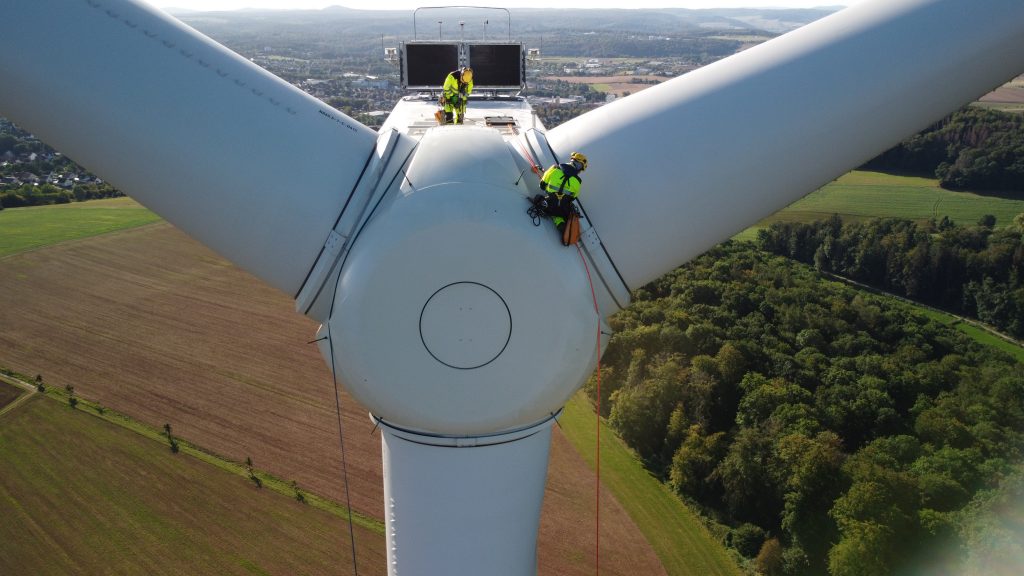
In 2020, Nabla Wind Power was asked to extend the blades of a wind turbine in order for it performance be increased by 10%. To do this they used digitalizing techniques that were originally designed with terrestrial laser scanners.
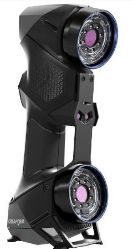
The best portable 3D scanner suited for this task was the HandySCAN 3D | BLACK. Thanks to its dynamic referencing feature, it can digitalize precisely in harsh conditions. Vibrations do not affect the results and the uncertainty of the measurements is far less than a millimeter. As the task had to be realized directly on the wind turbine, a Creaform Application Engineer trained two industrial climbers from the company Asaken and taught them how to use the HandySCAN 3D. Then the climbers went up to the top of the wind turbine at 130 meters, had to get out of the hub and rappel down to 65 meters above the ground.
The first thing to do was to stick targets on one of the rotor blades on the last 7 meters. These targets are used as reference points by the HandySCAN 3D. Then they started the scan. While one of the industrial climbers was wearing the laptop, the other was handling the scanner. Meanwhile, the Creaform Application Engineer was overviewing the scan from the ground via Teamviewer. At this height, wind conditions are always an issue and several times, it became so windy that the works had to be stopped due to the strong winds. Also, some technical issues of the wind turbine itself disturbed the scan process: for example, the rotor blocked and couldn’t be brought into a vertical position. But finally, the scan was performed successfully.

3D Scan Data of Wind Turbine Blade

CAD of the reversed engineered rotor blade in CATIA
Nabla’s Head of Operation, Eder Murga, was really pleased with results: “The handling of the provided service was professional, both from Creaform and Asaken. Despite the harsh conditions and many interruptions due to strong winds, everyone involved faced the change in conditions with great flexibility and, in the end, we managed to get the perfect results. A hand-held, self-referencing measuring system such as the HandySCAN 3D is the only way to carry out such a measurement in a harsh environment.”
Original Article – https://www.creaform3d.com/blog/at-lofty-heights-3d-scan-of-a-wind-turbine-blade/
Ask us about 3D scanning services and equipment!
Request a Quote or Speak with an Expert
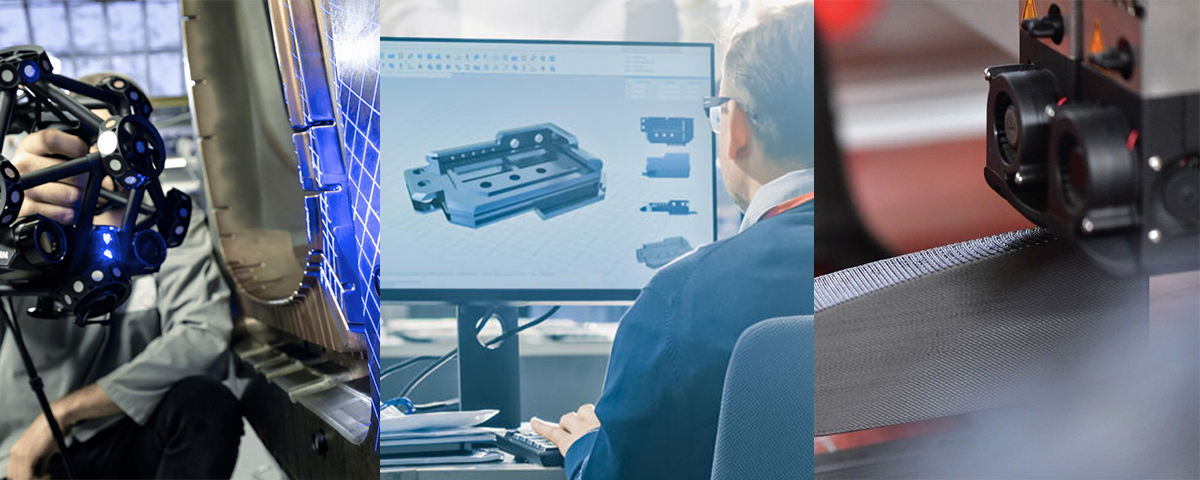