It seems hard to believe that the first-ever 3D printer was created way back in 1983. In the intervening years, technology has clearly evolved, and new developments are announced almost daily. The truth is, the 3D printing industry already looks very different from the way it did 10 years ago. By the year 2030 it will be unrecognizable.
Speed and efficiency
Time-consuming and expensive manufacturing techniques have been superseded by fast, efficient, and cost-effective 3D printing and Injection molding processes. New developers can now get an injection molding quote and know almost immediately what it will cost to bring a new product to market. In addition, injection molding services offer minimum order quantities as low as 100. This allows fledgling companies to adequately test a product before launching.
Injection molding is the most cost-competitive technology for manufacturing high volumes of identical plastic parts. Once the mold is created and the machine is set up, additional parts can be manufactured very fast and at a very low cost. The recommended minimum production volume for injection molding is 500 units. At this point economies of scale start to kick-in and the relatively high initial costs of tooling have a less prominent effect on the unit price.
Limitless possibilities
In the early stages of 3D printing, it was assumed by many outside the industry that plastic would be the material used most predominantly. To an extent that misconception remains. The truth is, the integration of new materials is one of the most rapidly developing areas of 3D printing technology. Successful printing in metal has been a game-changer, and sectors such as the automotive industry are already investing in and benefiting from this technology. The advantages are clear to see, from the creation of prototypes and detailed scale models to faster assembly and reduced weight. Other materials currently being developed for 3D printing services include polymers, new alloys, glass, ceramics, photosensitive resins, composites, and even food.
Geometric complexity at no extra cost
3D printing allows easy fabrication of complex shapes, many of which cannot be produced by any other manufacturing method. The additive nature of the technology means that geometric complexity does not come at a higher price. Parts with complex or organic geometry optimized for performance cost just as much to 3D print as simpler parts designed for traditional manufacturing (and sometimes even cheaper since less material is used).
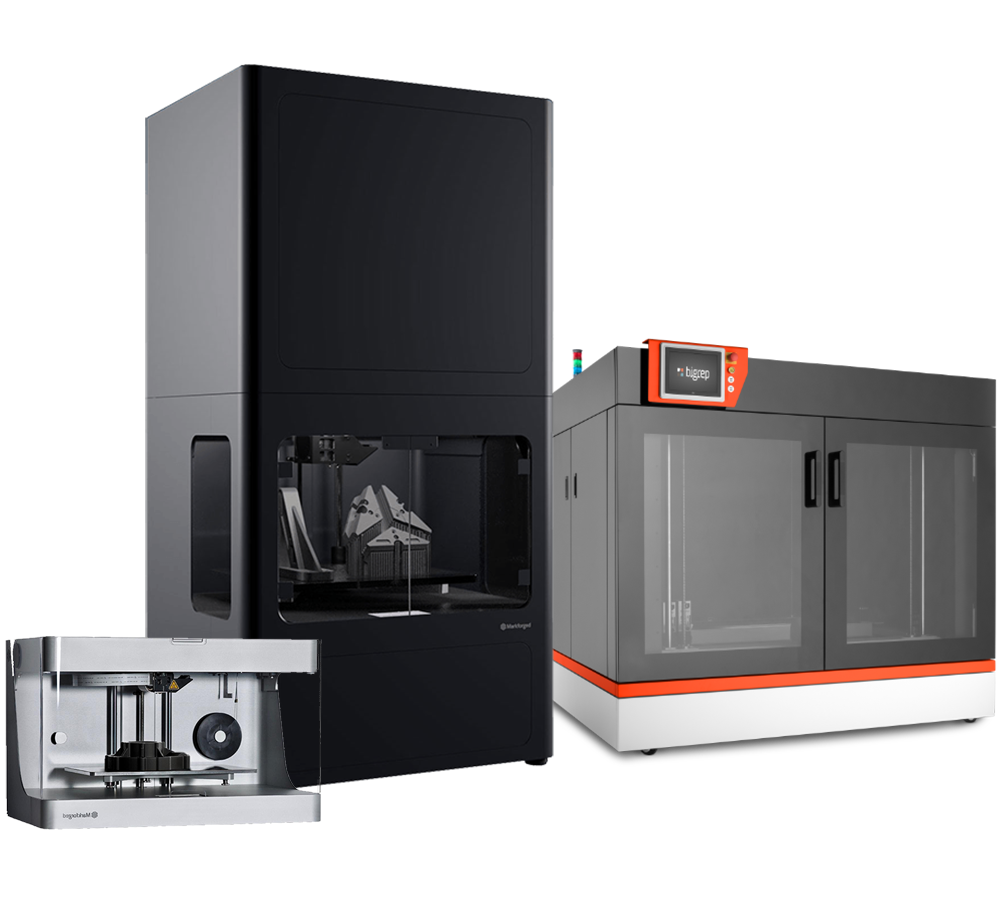
3D Printers from Markforged & BigRep
Very low start-up costs
In formative manufacturing (think Injection Molding and Metal Casting) each part requires a unique mold. These custom tools come at a high price (from thousands to hundreds of thousands each). To recoup these costs identical parts in the thousands are manufactured.
Since 3D printing does not need any specialized tooling, there are essentially no start-up costs. The cost of a 3D printed part depends only on the amount of material used, the time it took the machine to print it and the post-processing – if any – required to achieve the desired finish.
Low-cost prototyping with very quick turnaround
One of the main uses of 3D printing today is prototyping – both for form and function. This is done at a fraction of the cost of other processes and at speeds, that no other manufacturing technology can compete with:
Parts printed on a desktop 3D printer are usually ready overnight and orders placed to a professional service with large industrial machines are ready for delivery in 2-5 days. The speed of prototyping greatly accelerates the design cycle (design, test, improve, re-design). Products that would require 8+ months to develop, now can be ready in only 8-10 weeks.
Learn more about 3D printing processes commonly used for rapid prototyping.
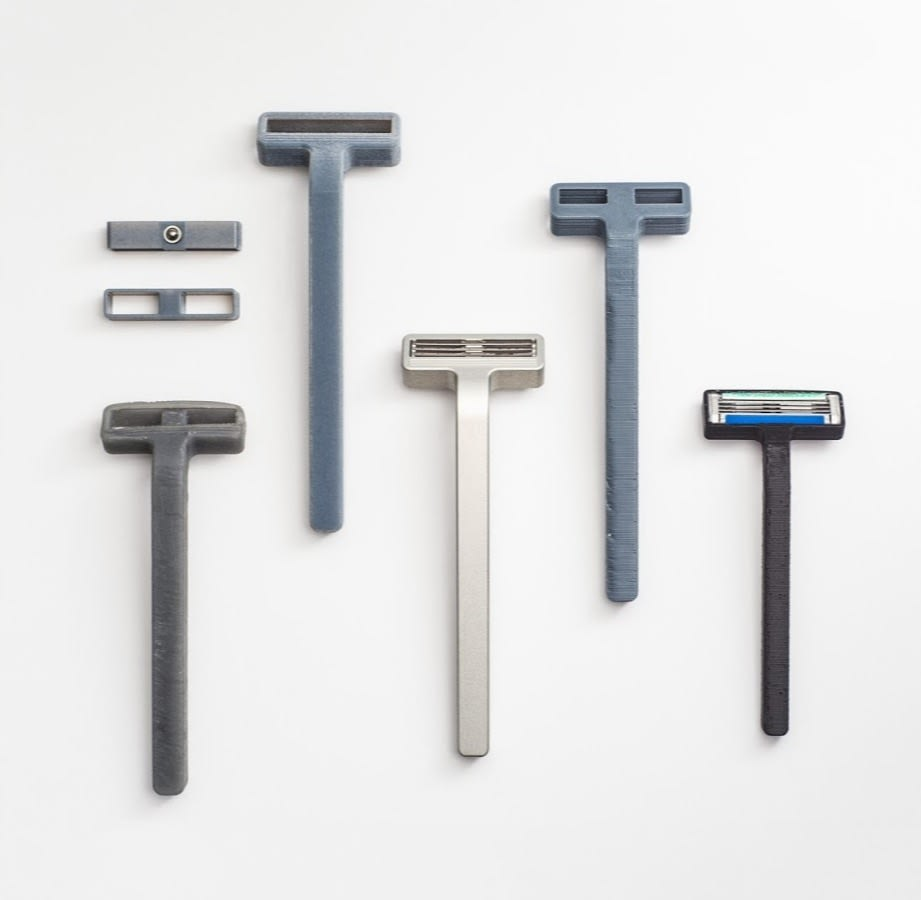
Cycle of a development process from prototype to final product.
Medical benefits
The field of medicine has been benefiting from 3D printing technology for over 20 years. Current thinking, however, is that the surface has been little more than scratched. Prosthetics and implants customized for specific patients are already being manufactured using 3D printing processes. Rapid development is also taking place in the fabrication of tissue and organs, as well as a host of other personalized medical items and apparatus. In addition, detailed and accurate anatomical models are revolutionizing the way medicine is taught. It has been estimated that the use of precise 3D printed replicas could reduce surgery time significantly for many patients.
Humanitarian uses
Alongside the obvious benefits to industry and medicine, 3D printing technology is now being explored as a potential aid to humanitarian issues. Intensive research is already taking place in the area of 3D printed food. Because cooking the food has so far been an issue, the idea of lasers within the printer is being investigated. Nutritional meals printed from cartridges of powder and oils are a potential solution, too. If mass-produced cheaply, these would be easy and inexpensive to transport. The lower cost and efficiency of 3D printing will also assist in the provision of homes and shelters in areas of humanitarian need.