With the ability to complete complex tasks on it’s own and never getting tired, seasick, or needing to shelter in rough weather, AUVs are already revolutionizing areas such as archeology, where they have discovered shipwrecks like the USS Nevada.
A 3D-printed submarine was a logical next step that made complete sense, one the Navy took in 2017. Partnering with the Oak Ridge National Laboratory in notably landlocked Tennessee, the Navy 3D printed a submarine hull that was reportedly 90% cheaper than those constructed with traditional methods and was made in mere days.
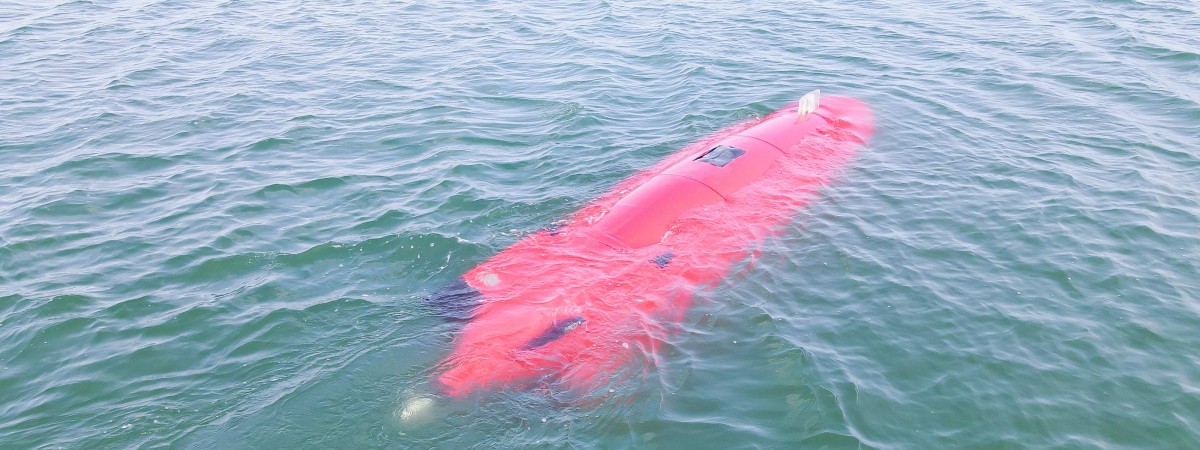
Credit: Dive Technologies
– ProHT (ABS-Like) – $129.95 for 2.5 kg Spool
– PLA – $72.00 – for 2.3 kg spool
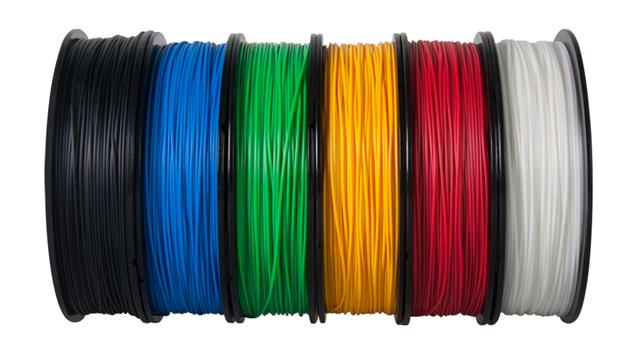
Prints using PLA, PETG, Pro HT, TPU, PA6/66
Design to Dive: The 3D-Printed Submarine
That was just a hull, however; DIVE-LD is a full-fledged, autonomous 3D-printed submarine, and the construction techniques being pioneered by Dive Technologies could be leading the (depth) charge.

Because of the speed and cost-effectiveness of 3D-printed submarine components like these, Dive Technologies can theoretically whip up any kind of sub relatively quickly. Credit: Dive Technologies
“Using large scale 3D printers, the Boston-based startup can slash costs, speed up production, and create any submarine imaginable in just a few weeks — from idea to fully-functioning prototype,” Popular Mechanics’ Hambling writes.
The key is skipping the costly, gigantic component known as a pressure vessel.
Submarines operate under immense pressures. To keep the sub and its squishy passengers from being crushed like a Twinkie under a watermelon, the submarine needs a stout steel inner hull to protect against the ocean’s powerful weight, known as the pressure vessel.
But there’s a way to skip this step. You just gotta cut out the middleman. Or crew, in this case.
“Using large scale 3D printers, the Boston-based startup can slash costs, speed up production, and create any submarine imaginable in just a few weeks — from idea to fully-functioning prototype.”
DAVID HAMBLING
Because there’s no one inside the autonomous DIVE-LD, the sub can allow itself to be flooded until the pressure inside its hull matches the pressure outside.
After the AUV systems are installed in the DIVE-LD’s skeleton, the exterior is then applied and finished, and you’ve got yourself a 3D-printed submarine.
“We went from an inventory of parts to a fully integrated AUV in three days, complete with a low-drag 3D printed skin,” Dive director of R&D Tim Raymond told Hambling.
Original Article: https://www.freethink.com/articles/3d-printed-submarine