With the advent of 3D printing, along with the latest manufacturing materials, innovators in the mobility space are now able to provide a greater level of independence and a better quality of life for amputees and those affected by neurological disorders.
Millions of people around the world depend on prosthetics and other mobility devices to negotiate the world around them. Yet access to prosthetic care and technology varies drastically from country to country. In fact, according to the World Health Organization,
“only 1 in 10 persons located in low-resource areas has access to adequate prosthetic technology.”
Not only are clinicians and engineers now able to push the boundaries of additive manufacturing to provide cutting-edge devices, they’re also able to create durable, high-functioning prosthetics more affordably, allowing more people from resource-starved areas access to greater mobility.
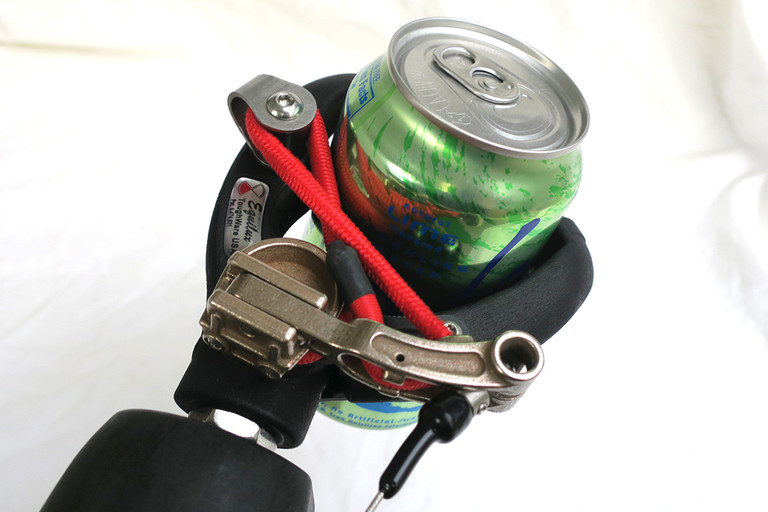
Toughware Prosthetics:
Bradley Veatch, President and CEO of Colorado-based Toughware Prosthetics, is committed to creating affordable and accessible prosthetics for the underserved amputee community.
For the better part of two decades, Veatch had been using the latest technology to design high-functioning prosthetics. He was extremely successful in the engineering sense, he recalls,
“but I had this device that was so expensive that there were probably ten people in the United States that could afford the thing.”
The experience taught him that the world didn’t need more sophisticated prosthetics, but rather more durable and accessible options. So he changed his direction and decided to focus on creating prostheses for people in developing countries. The new design is ideal for those living in developing countries who may rely heavily on physical activity for their daily needs, or who may not have a reliable power source or the ability to access to a computer – accessories mandatory for other, more complex designs.
“I wanted to actually focus on creating technologies that were appropriate and that could do what these people needed them to do, like swing a hammer, carry a 22-pound bucket of water, or lift a child,” says Veatch.
However, Veatch faced an issue: the more complex parts would need to be sent out to be prototyped, and he would have to wait upwards of six weeks to get them back, slowing down his entire design process.
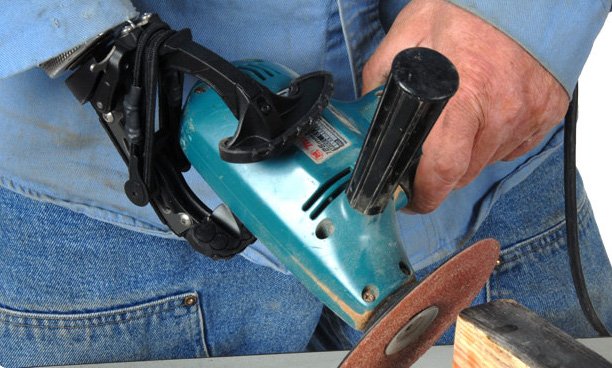
The Solution:
Veatch and his team discussed the potential of purchasing a Markforged composite printer, capable of printing in continuous carbon fiber.
“As we got further on some of our projects I became more interested because we needed high strength in some of the parts,” says Veatch.
When some budget became available, the team jumped on the opportunity and bought a Markforged desktop printer.
His Markforged 3D printer now allows Veatch to manufacture some elements of this design not only stronger, but also quicker. “I wasn’t interested in losing six weeks of schedule while things were made in a machine shop,” he says. “I’m actually able to get a lot more done in a much more concentrated timeframe. I can produce an engineering design … print and then begin running tests, sometimes even the same day. I can print what I need, when I need it, and continue with my iterative design process.”
Not having to machine prototype parts also keeps costs down for Toughware and its users. One prototype bracket, for example, was going to cost Veatch $65 to be machined out of aluminum, but was only a few dollars when printed using his Markforged composite printer, according to Veatch. “And I was able to put carbon fiber in it, which was really cool. So it was strong and just what I was looking for in the application time. And it only took five hours to print!” Veatch and his team are now able to quickly iterate on new designs, and don’t have to worry about higher costs or longer lead times